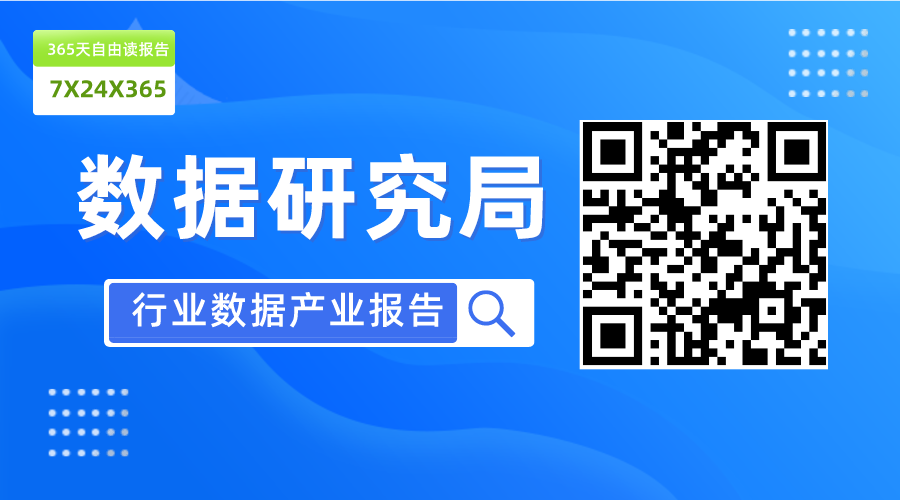
Energy Transition Outlook 2021TECHNOLOGY PROGRESS REPORTA review of 10 technologies setting the pace of the energy transition over the next five years.TECHNOLOGY PROGRESS REPORT Energy Transition Outlook 2021Remi Eriksen Group president and CEO DNVFOREWORDThe world needs to transition faster to a deeply decarbonized energy system, reducing emissions by around 8% each year to ensure an energy future in line with the 1.5-degree ambition set under the Paris Agreement. This urgent and complex challenge needs full energy-system thinking: understanding the timeline and interdependencies of technologies and policies. It also requires the courage to make difficult decisions.2ForewordTransitioning faster with full energy-system thinking This new technology report from DNV, a supplement to our main Energy Transition Outlook, is a contribution to a fuller understanding of the technologies driving the transition. In this report, we concentrate on the technologies at the forefront of the energy transition and share some of the insights we have on expected near-term developments.The technologies that have the potential to deeply decarbonize the world’s energy system are well known. They are those that can help to scale renewable power generation and extend its reach through the electrification of new sectors, and which can remove carbon from fossil fuel energy sources, before or at the point of combustion.The challenge lies in navigating how and when to implement these technologies, which are at different stages of maturity, and in managing how they interact and rely on one another. Understanding this will enable industry, governments, and those financing the transition to effectively prioritize their efforts, to achieve the emissions reductions required this year, next year, and every year through to mid-century.A lot can change in five years. It wasn’t that long ago that electric vehicles (EVs) were a novelty for early adopters. Now, the EV revolution is becoming visible, and by 2025 there will be 13 million EVs on the roads in Europe alone. In 2016, the variability of renewable sources of power was widely seen as a barrier to the transition; now, with rapid advances in battery technologies, and with other digitally-enabled demand response and network storage options, variability is increasingly seen as solvable. Less than five years ago, hydrogen was notreally on the radar as a key energy carrier; now, many roads to decarbonizing hard-to-abate sectors lead to hydrogen.As I have stated before in previous editions of our ETO, there is no silver bullet for reaching net zero emissions by mid-century. The world needs to act urgently on multiple fronts – a great deal more renewables, further improvement in energy efficiency, and carbon capture and storage (CCS). Existing competitive technologies, such as solar and wind power, need to take full advantage of the virtuous circle where cost decline both causes and is caused by the growing number of unit installations. For less-mature technologies, like green hydrogen, scaling from prototype to worldwide commercial ubiquity is critical.Crucially, these technologies are interconnected. For example, one cannot predict green hydrogen uptake without understanding developments in renewable sources of power, and an understanding of CCS is not complete without considering technical requirements for pipelines transporting enormous quantities of CO2.In this UN Decade of Action for delivering the Sustainable Development Goals, policymakers and industry leaders are more focused than ever on the climate challenge. To meet it, they will need forward-thinking policies, innovation, and the willingness to make substantial investments. They also need full energy system thinking to connect these aspects, which starts with an objective, realistic understanding of the technologies involved. That is what we aim to provide in this report, as we explore the outlook for ten key technologies in the transition, with a focus on developments over the next five years.3TECHNOLOGY PROGRESS REPORT Energy Transition Outlook 2021CONTENTForeword2Introduction41 Floating wind102 Developments in solar PV143 Waste to fuel and feedstock184 Pipelines for low-carbon gases24Energy infrastructure and nano materials 285 Meshed HVDC grids326 New battery technology367 Novel shipping technologies40Marine Fuel cells40Nuclear-powered ships448 EVs and grid integration509 Green hydrogen production5610 Carbon Capture and Storage 2.062References66Project team714IntroductionINTRODUCTIONThis report is part of DNV’s suite of Energy Transition Outlook publications for 2021. It focuses on how key energy transition technologies will develop, compete, and interact in the coming five years.Debate and uncertainty about the energy transition tend to focus on what technology can and can’t do. All too often, such discussions involve wishful thinking, advocacy of a favoured technology, or reference to outdated information. Through this report, we bring insights derived from our daily work with the world’s leading energy players, including producers, transporters, and end users. Each of the ten chapters that follow are written by our experts in the field – or, in the case of maritime technologies, on the ocean.Because the pace of the transition is intensifying, describing any given technology is like painting a fast-moving train. We have attempted to strike a balance between technical details and issues of safety, efficiency, cost, and competitiveness. Transition technologies are deeply interlinked, and in some cases interdependent; any discussion on green hydrogen, for example, must account for developments in renewable electricity, hydrogen storage and transport systems, and end-use technologies such as fuels cells.Our selection of ten technologies is not exhaustive, but each of these technologies is of particular interest for the pace anddirection of the energy transition. They range from relatively mature technologies like solar PV, to technologies like nuclear fusion which are some distance from commercialization but which have current R&D and prototyping worth watching. Together they cover most, but not all, key sectors. We describe expected developments for the coming five years which, to a large extent, will determine how the energy transition unfolds through to mid-century. As such, this Technology Progress report is an essential supplement to our main Energy Transition Outlook forecast.Our aim is to make an objective and realistic assessment of the status of these technologies and evaluate how they contribute to the energy transition ahead. Attention to progress in these technologies will be critical for anyone concerned with energy.Driving Trends In addition to the all-encompassing goal of decarbonization, there are other current trends affecting development and changes in the energy system. Universal access to modern, clean, and safe energy is a key Global Goal. Digitalization, and efforts to tackle local air pollution, are also pushing energy technology progress.TABLE 1 Energy transition technologies described in this reportEnergy production Floating WindEnergy transport, storage, and distributionPipelines for low-carbon gasesDevelopments in solar PVMeshed HVDC gridsWaste to fuel and feedstockNew battery technologyEnergy use and conversionNovel shipping technologiesEVs and grid integrationGreen hydrogen productionCarbon capture and storage5TECHNOLOGY PROGRESS REPORT Energy Transition Outlook 2021FIGURE 1Energy Transition Outlook model showing the interconnectivity of energy systems and technologies16M FOSSIL FUT NGPopulationAutonomous and communaldrivingBattery sizeROTARDANSPORTaxTravel distance per vehicleLifetimeRangeFuelling and repair availabilityVehicle Vehicle utility demandRetirementsVehicle sales by typeInvestment costRefueling speed Use of fast rechargingGovernment supportOperatingCost ofcostownershipUnit energy use of new vehiclesFast recharging densityVehicle fleetEVs and grid integrationEnergy use of vehicle additionsCumulative EV salesEL EXTRACTIONResourcesFossil fuel productioncostFossil fuel demandFossil fuel supplyby type and regionPipelines for low-carbon gasesEnergy pricesGDP per capitaAviationenergy demandEnergy use of fleetMaritime energy demandNovel shipping technologiesRail energy demandEnergy demand by energy carrierBUILDINGSDemand feedback process details not shownANUFACTURICarbon capture and storagePower grid strengthMeshed HVDC gridsBattery priceElectricity demandFirm capacity demandGridinvestments AccumulatedstorageFirmadditionscapacityavailabilityCapacity RetirementsStorage additionsGreen hydrogenElectricity priceAvailableInstalledPower station additionsby typeProfitabilitycapacityShare of variable renewablesin capacityLevelizedAccumulatedSubsidy cost ofadditionselectricityCapital costProfitability of storageVariability in electricitypricestorageGeneration hoursWaste to fuelDemand feedback process details not shownGreen hydrogenFloating WindVariable costReceived electricitypricePOWER SUPPLYVariabilityin electricity demandNew battery technologiesDevelopments in solar PVIntroductionDriven by these efforts, the energy system is transitioning from one reliant on fossil fuels to one based on a diverse range of technologies that emit significantly less CO2. Much of the progress so far has been enabled by progress in technology, a process sometimes described by economist Joseph Schumpeter as “creative destruction". New innovations are replacing existing ones that are rendered obsolete over time. Just as the horse and buggy was replaced by Ford’s Model T, last century’s internal combustion cars are being replaced by Ford’s Mach-E and other EVs. In our Energy Transition Outlook publications, we describe our best estimate of the energy transition to 2050. Each coming decade will see major transformation of different parts of the energy system. Perhaps the 2020s will be remembered as the 'technology decade' which gave rise to several technologies – at different stages of readiness – that impacted the energy transition profoundly in the years to 2050.Selection criteria There are two selection criteria for how we choose a technology for inclusion in this report. First is whether it will lead to an observable shift in the energy system. We measure this on the basis of how quickly the technology is being deployed and whether costs are expected to fall over the next five years. Many of the technologies described here have already seen big reductions in cost and will double in capacity many times over the coming decades. Thus, there will be observable shifts in the energy system.The second factor is how the technologies interact with each other, sometimes referred to as sector coupling or energy value-chain integration. The overlapping and supplementary nature of several technologies can combine to create a step change and accelerate the creative destruction of existing technologies and pave way for the entrance of something new.The technologies that meet these criteria span the energy system: production, transport, and storage of energy, and the use and conversion of energy into useful services.Step change tends to happen when technologies combine. Floating offshore wind alone can provide electricity to the grid, but interconnected with a meshed offshore grid, new integrated battery technologies,connected EVs, and green hydrogen production, can improve the flexibility by an order of magnitude and accelerate the usefulness and competitiveness of the whole system.Step change tends to happen whentechnologies combine.For hard-to-abate sectors such as shipping, there are limited options for reducing emissions while still servicing the global demand for goods. Thus, new propulsion technologies using hydrogen fuel cells and nuclear have potential. The development of maritime technologies seldom happens without complementary development on land. In the case of fuel cells, an infrastructure of low-emission hydrogen must be built and the whole value chain of such technologies will need integration. For nuclear technologies to develop, new and emerging advancements in Small Modular Reactors (SMRs) must be successfully deployed on land, where their first challenge will be competing with land-based solar PV and wind. All the technologies described here are connected and both compete with and depend on each other. Thus, we can use our system dynamics diagram of causal loops describing parts of our Energy Transition Outlook model to show how connected the energy system and the technologies are (Figure 1). Note, the diagram only shows high level interactions between transport demand and the power system. Other major demand sources are not detailed.Costs For any given technology, costs tend to decline at a constant rate with each doubling of accumulated capacity. This is called the Cost Learning Rate (CLR). Each doubling of the installed capacity of a technology takes longer, progressively slowing the annual rate at which costs will decline. CLRs come from core technology improvements based on research and innovation (e.g., around material choices or modal shifts from combustion engines to electric ones). CLRs are also driven by more effective production, where learning-by-doing and experience from increased deployment improves over time. Economies of scale, where the cost of producing7TECHNOLOGY PROGRESS REPORT Energy Transition Outlook 2021the initial unit compared with the nth unit of a component fall over time, also play a role. CLRs tend to be self-reinforcing: cost reduction both causes and is caused by the growing number of unit installations.The CLR associated with core technologies tend to be higher than that of supporting technologies. Thus, technologies that mainly comprise ‘core’ technology (e.g., batteries) tend to have higher learning rates.Cost Learning Rates tend to be selfreinforcing: cost reduction both causes and is caused by the growing number of installations.For example, PV panels – a core technology – have a CLR of 28%, while the balance of supply (BOS) materials tend to be more settled technologies and have a CLR of only 9%. Notably, technology costs tend to fall at constant rates relative to deployment while other costs, e.g. labour, do not. Thus, the operation and maintenance cost curves for wind and solar PV are around half, at best, of the technology learning rate, and installation learning rates are even lower.In some industries, for example extractive industries, costs rise with time because the easy deposits tend to be accessed first. Similarly, for some renewable energy technologies, the most favourable spots for installation are used first with decreasing yield over time as more capacity is built out (Figure 2). This ‘stress’ driver contributes to the improvement and progress of technologies.FIGURE 2 Cost learning ratesCostNovel technologies (e.g. Floating wind)New technologies (e.g. Batteries, PV, Onshore wind)Established technologies (e.g. Oil and gas development, Combustion engines)Development and pilotScaling up production8Cost reductions continue, but possibly countered by other factorsTechnology maturityIntroductionTABLE 2 Global growth of new technologies – based on Energy Transition Outlook 2021Technology Number of passenger EV sold per year Installed solar PV capacity (GW) Floating offshore wind installed capacity (MW)2015 300 000 200 6.32020 2 000 000 600 55.32025 20 000 000 1 500 1 400Speed of transition It takes time for a new technology to replace an existing one, especially when considering the scale and size of the global energy system. However, compound growth of a new entrant will eventually change a system of any size. For instance, passenger EV sales numbers were barely noticeable in 2015, with less than 300,000 sold annually, but by 2025 we forecast the number of new EV passenger vehicle sales to reach almost 20 million per year, more than a 20% global market share of new vehicle sales.Today’s increasingly mission-oriented energy transition differs from previous transformations of the energy system. The Paris Agreement and Sustainable Development Goals combined with green initiatives and COVID-19 stimulus packages, will intensify government action and policies on climate, energy, and technologies targeting structural energy-system changes that address planetary, economic, and human development risks. The use of near-term policy action to fulfil long-term goals is unprecedented and differentiates the current energy transition from previous ones that have mainly been driven by market forces.The use of near-term policy action to fulfil long-term goals is unprecedented and differentiates the current energy transition from previous ones that have mainly been driven by market forces.The global finance industry is adding momentum to decarbonization. Green bond issuance is at record levels and companies addressing decarbonization are rewarded with high share prices and grow rapidly. The Taskforce on Climate-related Financial Disclosures (TCFD) identified climate change as a top risk to the global economy and suggests companies use scenarios to better evaluate their business model related to changes in climate, policies, and technologies. The challenges and opportunities facing the finance community in supporting an affordable, accelerated and just transition will be addressed in more detail in our upcoming publication, Financing the Energy Transition, published in September along with our main Energy Transition Outlook 2021.No silver bullet This report describes most of the technologies that all net-zero commitments and pledges towards a Paris-compliant future will aim to use. No single technology can solve the challenge, rather they will need to work together. The focus going forward will no longer be the competition between fossil and non-fossil solutions, but rather how to accelerate the uptake of new decarbonization technologies. All of these technologies, with the exception of nuclear fusion, also play a role in our upcoming Energy Transition Outlook 2021 where, with other parameters, they interact in our system dynamics model all the way out to 2050, and we describe the effect this has over a 30-year timeline. However, the next few years will be pivotal for these technologies. If we are to have any chance of reaching the ambitions of the Paris Agreement, these technologies must be scaled and the transition to a low-carbon future accelerated now.9TECHNOLOGY PROGRESS REPORT Energy Transition Outlook 20211 FLOATING WINDFloating wind turbines give access to abundant wind resources over deep water – at least four times as much ocean surface space compared with bottom-fixed wind. This gives an increased flexibility in site selection including the possibility to take advantage of areas with higher wind speed and areas with lower social and environmental impact. In the next five years we expect to see significant technology development in floating wind to reduce cost, scale, and increase applicability.10Floating wind 1Potential for growth DNV projects that floating wind will contribute 250 GW, some 2% of world’s electricity generation, by 20501. This corresponds to a development of more than 3,000 times the size of Hywind Tampen, the world's largest floating offshore wind farm currently under construction in Norway, or 15,000 turbine units.Floating wind can bring clean energy to coastal communities previously unserved by wind power, for example some of the mega-cities in Asia Pacific. But there are also other aspects that generate interest in floating wind, such as the opportunity for oil and gas and maritime players to transfer their skills, vessels, and yards into a new, growing industry as well as the option of using floating wind to power oil and gas installations to reduce their CO2 footprint.Current status and cost Two European floating wind farms, Hywind Scotland and WindFloat Atlantic in Portugal are now up and running and provide evidence that floating wind is technically feasible. Hywind Scotland, which has been in operation since 2017, has achieved the highest average capacity factor of all offshore wind farms in the UK which indicates that floating wind can perform as well as, or even better than, bottom fixed offshore wind.The main issue with floating wind is, however, cost. While bottom-fixed wind currently has projects with a levelized cost of energy (LCOE) below 50 USD/MWh, the first floating wind farms have seen LCOE exceed 200USD/MWh. Much of this is due to the small size of the first floating wind farms and the immaturity of the technology and supply chain. There are, however, some characteristics specific to floating wind that impact cost and which require attention. While the steel mass for a foundation used for a bottom-fixed wind farm with 8 MW turbines could be typically around 1,000 tonnes, the floating wind structure could require more than 2,000 tonnes of steel for the same turbine size. Further material is needed for anchors and the mooring system. In addition to requiring potentially more than double the amount of steel, the structures themselves are more complex to design and fabricate, especially compared with monopiles. Other aspects contributing to higher costs are dynamic cables and the added maintenance of the floating structure and mooring system.New and improved design New and improved floating wind designs will contribute to cost reductions. By 2025, the Hywind spar will have benefited from three previous iterations with one prototype and two pilot wind farms, and the WindFloat semi-submersible will have reached its fourth iteration with one prototype and three pilot wind farms. In France, the Ideol barge – the SBM tension leg platform and the Naval Energies semi-submersible – is expected to have been tried for the first time in a wind farm configuration. In this period we will also see some additional concepts tested as full size prototypes such as the TetraSpar which differs from the other concepts due to its modularization and simple assembly, and OO Star which combines the flexible semi-submersible concept with concrete fabrication.Technology providers with assets already deployed clearly have a head start in terms of experience, but we also expect many technology developers to rival them with new concepts. There are currently more than 40 floating wind concepts under development, and new concepts are frequently being announced. Several of these are based on similar designs to the leading concepts but challenge them on factors such as mass and fabrication approach, while other concepts have more radical changes such as a turret mooring system, multiple turbines on each floater or combining floating wind with wave devices or hydrogen production.Common to all the concepts is the mooring system, and significant development in this area is expected. This will be both in optimization of currently-used technology, and through the introduction of new technology, materials and methods for floating wind such as synthetic ropes, load reduction systems, integrated tension monitoring systems, quick connection systems and shared mooring.Expanding application Expanding the application of floating wind to new markets and conditions will also require technology development. Larger floating wind farms, further from shore in deeper waters, will require floating substations, with development of dynamic cables with higher voltage and power levels than currently available and electrical equipment, such as transformers and switchgear, suitable for the typical11TECHNOLOGY PROGRESS REPORT Energy Transition Outlook 2021movement of a floating unit. Global deployment of floating wind will also require an increase in the water depth envelope to use floating wind on sites of 1,000m but also at shallow sites down to 40 m. Consideration towards special weather conditions such as hurricanes and typhoons will be relevant in certain markets. Concrete floaters will have a role, as they allow for more local fabrication.Scaling Over the coming years, floating wind will scale both in turbine size and wind farm size. Technology providers will test their solutions with turbines potentially larger than 20 MW, which could lead to design modifications beyond increasing the size of the structure to cope with the added loads.With the larger wind farms, new ways of installing, fabricating, and operating the floating wind turbines will be needed. For installation and fabrication, we expect developments in serial installation and fabrication. For operation, there will be advances in condition-based maintenance, use of digital twins, risk-based inspection, robot inspection of the floaters and mooring system, and in the development of methods for major replacement of turbine components offshore. In 2025 an increasing number of floaters will be in operation, allowing the industry to learn more about day-to-day operations, wind turbine performance and events such as major component replacement. Those learnings will undoubtedly spur new developments.The common success of the industry is dependent on sharing operational data and lessons learned, and developing and agreeing on international rules and standardsChallenges that need to be overcome DNV expects the cost of floating wind to reduce by 70% as 2050 approaches (Figure 1.1), ending up with only a small premium in LCOE compared with the bottom-fixed wind average.There are some early signs that we are on the right track. Investment cost per MW for Hywind Tampen, is 40% lower than Hywind Scotland installed in 20172. The French government set the target price for the next round of floating wind farms in South Brittany and Mediterranean at 120 EUR/MWh and 110 EUR/MWh, respectively. This is half the tariff of 240 EUR/MWh which the first four 24-30 MW pilot wind farms are receiving3.There are, however, some potential challenges that may impact cost reduction. While it is encouraging to have so many new floating wind designs being tested, the risk is that the wide range of design concepts could also be a barrier for the needed cost reduction in the industry. The number of different fabrication approaches and shapes makes it difficult for the supply chain to provide efficient fabrication facilities and for turbine manufactures to make an optimal turbine. Standardization of concepts or elements of concepts could contribute to faster development. Lack of industry cooperation, increased local content requirements and country specific regulations represent other potential challenges for the industry that could hinder globalization.The common success of the industry is dependent on sharing operational data and lessons learned, developing and agreeing international rules and standards, and engaging in joint industry projects to solve technical challenges.DNV perspective Floating wind has great potential. Enabling this potential requires the industry to tackle a range of challenges to expand application, scale and reduce costs without compromising safety. With the combined experience and eagerness from the players in the oil and gas, maritime and offshore wind sector, DNV believes that technical and cost reduction challenges can be overcome. However, as with most industries, the real results come from deployment, and this is where policymakers have a role to play. Long-term targets, clear regulations that do not hinder international cooperation, and incentives will give the supply chain the predictability to attract finance, allow for globalization and the industrialization of the technology, and push floating wind costs down quickly to competitive levels.12Floating wind 1200‘100‘88 MW 020223,000x250,000 MW203020402050Our projections are that offshore floating wind will grow to reach a total capacity of 250 GW by 2050 – almost 3,000 times the size of Equinor's Hywind Tampen, enteringinto operation in 2022. (Image: courtesy, Equinor.)13TECHNOLOGY PROGRESS REPORT Energy Transition Outlook 2021Bifacial solar panels2 DEVELOPMENTS IN SOLAR PVSolar photovoltaics (PV) are the world’s fastest growing renewable electricity resource. This growth is expected to continue to accelerate in the coming decades, with PV electricity generation expanding 30-fold from 0.8 PWh in 2019 to 22 PWh in 2050.Since their creation at Bell Labs in 1954, silicon solar cells and their corresponding PV modules have become a defining part of the energy transition, bringing clean, renewable energy to power grids and homes around the world2. Underlying this revolution are ongoing technological innovations to both PV modules and systems that we will discuss in this chapter. Storage solutions that mitigate the variability of and add value to solar energy assets are addressed in chapters 6 and 8.State of the solar PV market Today’s PV systems use either crystalline silicon or thin film technologies. Crystalline silicon cells – in either monocrystalline or polycrystalline form – have been the workhorse of the solar industry for decades. Their primacy began to be challenged from 2007 onwards3 with the introduction of thin film modules, made by depositing a thin film of photovoltaic material (typically amorphous silicon (a-Si) or cadmium telluride (CdTe)) on14Developments in solar PV 2a substrate such as glass, plastic or metal. Crystalline silicon PV modules continue to dominate today’s market, although thin film PV modules have seen similar cost reductions and capacity expansion.The precipitous drop in the price of both PV technologies over the past decade has led to the rapid acceleration of PV deployment. This in turn, catalysed corresponding market dynamics that drove down the cost of other hardware components, including inverters as well as racking and single-axis tracking systems. In addition, lessons from the integrated circuit and electronics industries have continuously improved PV material and component quality and lowered costs. New PV technologies are expected to continue these trends, making PV energy the lowest-cost power source in nearly all markets by the end of the decade4.Our 2020 ETO model predicts installed solar capacity to double by 2025 and quadruple by the end of the decade leading to installed global capacity of nearly 3,000 GW by 2030 (Figure 2.1). Over that time, PV will account for the largest share of new capacity ahead of onshore wind (Figure 2.2).Improvements in crystalline silicon PV Crystalline silicon PV module technologies — including advanced silicon doping and cell technologies, cell interconnection, larger format cells and panels, and bifacial modules — are developing rapidly.Over the past few years, much of the supply chain has transitioned to more efficient passivated emitter rear contact (PERC) technology through upgrades to existing lines and the build out of new manufacturing capacity. The industry’s transition to PERC has allowed for rapid deployment of bifacial cell and module technologies that increase power generation by collecting energy from both sides of the panel. Bifacial modules are becoming popular in numerous markets due in part to the moderate increase in energy yield. Many manufacturers use dual glass architectures for bifacial modules suggesting improved reliability allowing them to offer better warranties. However, several manufacturers offer transparent polymer backsheets instead of glass to benefit from bifacial gain without increased module weight5.Heterojunction and passivated contact technologies such as tunnel oxide passivated contact (TOP-con) add15TECHNOLOGY PROGRESS REPORT Energy Transition Outlook 2021advanced thin layers to the surface of "n-type" PV silicon wafers. This produces still higher cell efficiency and increases in the power output of PV modules, helping to continue to drive PV performance gains well into the coming decade.Further improvements come from cell interconnection. The loss of light transmission due to cell busbars, the metallic strips that conduct the current generated by the PV cell, limits PV efficiency. New multi-busbar (MBB) crystalline silicon modules allow for many thin wires and reduce resistance losses across cells and modules. Additionally, many manufacturers have developed half-cell modules to further reduce resistance losses and enable new module configurations. Both MBB and half-cell modules also reduce metallization costs and losses from shading and microcracks while further reducing cost and increasing both module performance and reliability.Finally, new larger format cells and modules are expected to further reduce cost across manufacturingand system installation as well as increase the power output of modules. A move toward larger cell and module formats is expected throughout the coming decade as manufacturers continue to optimize designs and reduce production cost.Thin film module improvements Thin film PV technologies have also moved toward larger format modules to improve compatibility with racking and single-axis tracking products and thus reduce module cost. Improvement in thin film solar cell technologies have come from changes in composition and contacts that increase cell current, voltage, and overall efficiency, thereby ensuring continuous improvements in power output. Further enhancements may include tandem cell configurations, discussed below.PV system technologies New inverters, trackers, and racking solutions for whole PV systems are increasing system performance and yield thereby further reducing costs. Inverters have continued to grow in capacity, with central invertersSchematic structure of the tandem solar cell stack in 3D courtesy of Eike Koehnen/HZB. In January 2020, a group at the Helmholtz Zentrum Berlin (HZB) set the world record for tandem cell efficiency at 29.15%16Developments in solar PV 2reaching 5 MW and string inverters at 250 kW. Central inverter architectures are competing with distributed networks of string inverters by becoming easier to service and including multiple maximum power point controllers to maximize system yield. As large format modules with different current/voltage outputs enable longer strings, the DC current input of inverters will increase relative to standard string voltage and will be adapted to maximize the value of new module technologies.Manufacturers are developing advanced single-axis tracking algorithms and independent row designs for large PV arrays. These maximize energy production by minimizing shading on neighbours in each row even in cloudy illumination or uneven terrain.Fixed tilt racking solutions are also advancing. Manufacturers are reducing installation costs and materials, maximizing ground coverage ratios, and optimizing system yield through numerous innovations. These may significantly reduce near-term capex costs, while leveraging the continued decrease in module cost to rapidly put more PV capacity in the field6.Future advancements To move module efficiencies beyond 25%, technology roadmaps for both crystalline silicon and thin film modules are increasingly looking toward tandem solar cell architectures. Tandem cells combine two different semiconductors that more efficiently convert different parts of the light spectrum into electrical energy. These include perovskite solar cells being developed in research labs for more efficient conversion of the visible part of the spectrum, and silicon, CdTe, or CIGS semiconductors in tandem cell configuration converting infrared light into electrical energy. These systems to date have shown cell efficiencies approaching 30%, which is not achievable with commercial single junction technologies7.Solar generation is also finding new applications. Floating solar PV projects, for example, are attractive in many areas with limited available land to reduce land acquisition costs or to uniquely couple to hydro or pumped storage facilities, with added benefits ofreducing evaporation of the hydro reservoirs. Building-integrated PV (BIPV) and co-generation with agricultural practices are also being explored with some pilot projects already underway. These will continue to integrate solar generation into built and rural environments, while increasing the total value and productivity of land (or water) use overall.Lastly, there continues to be rapid development in data analytics for monitoring and asset management platforms. These analytics can reduce system losses and optimize system revenue against operation and maintenance costs. Operational analytics, predictive maintenance, and active control of dispatchable solar assets will ensure future projects continue to operate efficiently throughout their useful life8.DNV perspective We anticipate substantial growth in solar capacity, driven primarily through cost reductions and the competitiveness of solar assets against traditional electricity generators. Rapid technology development across the industry will continue to underpin cost and efficiency improvements. Taking advantage of new technologies as they come online can bring opportunities to further improve the value and resilience of solar assets for the decade to come.In order for PV to meet the needs of the energy transition, the industry will need to look beyond PV technology and cost improvements. The value of solar generation in the coming decade and beyond must be maintained as installed capacity increases. This can be accomplished through the integration of storage into the electricity grid or via hybrid solar and storage systems, as well as through dynamic energy markets that can respond to low cost or low carbon signals to better match load to local or regional PV generation. It is clear that PV will play a key role in the energy transition, but integration of complimentary technologies, markets, and regulations can help accelerate our solar future.Durable, high performance PV generation is a major stepping-stone to the energy system of the future, and DNV is eager to contribute our expertise in accelerating its buildout.17TECHNOLOGY PROGRESS REPORT Energy Transition Outlook 20213 WASTE TO FUEL AND FEEDSTOCKWaste is increasingly being viewed as a resource in the wrong place. This applies particularly to the growing mountain of municipal solid waste (MSW) – over two billion tons of it annually worldwide, which, with rapid urbanization, is set to increase by more than 60% by 20501. Most of this waste is biogenic and along with other combustibles, such as plastic, has long been tapped as a source of energy via incineration. In recent decades attention has shifted to include MSW as a source of fuels, principally methane and biodiesel.Separating and valorising MSW streams into higher value fuels like hydrogen and sustainable aviation fuels (SAFs) will likely be hot topics over the next five to ten years as technology solutions for decarbonizing hard-to-abate sectors become ever more urgent. With the intensifying social and policy focus on circularity and reuse, feedstock recycling of separated waste is also gaining currency. This applies especially to plastic waste, where technology for the chemical recycling of post-consumer plastic to effectively produce a virgin resin equivalent is attracting interest from leading brands and policymakers.Waste-to-energy (WTE) Energy recovery from waste in the form of electricity and/or heat is on the rise worldwide, driven both by the increased availability of waste and by technological improvements. In addition, policymakers are increasingly aware of the contribution of waste to GHG emissions both directly (mainly through methane emissions from landfills) and indirectly through inefficient linear use-and-dispose consumption. UNEP has estimated that global GHG emissions could be reduced by some 10–15% through improved solid waste management18Waste to fuel and feedstock 3(recycling, waste diversion from landfill and energy recovery from waste)2.The waste-to-energy (WTE) market was valued at some USD 30bn in 2019 and is expected to grow at a CAGR of 4.6% over the next five years3, with the fastest rate of growth in the Asia Pacific region (~15% CAGR) where there is limited space for new landfill sites to cope with a rapidly growing amount of waste4.Options for the recovery of energy from waste generally follows a trade-off between low cost / low energy capture and high cost / high energy capture. Strategies at the lower end of the scale may include incineration and landfill gas capture, while the high end of the scale may involve the production of sustainable aviation fuels through advanced thermo-chemical processes. Exceptions to this continuum of options do occur, and are generally linked to one of three factors:— Policy intervention: a WTE plant might benefit from the diversion of high gate fees for landfilling such that waste for the plant arrives at a significant negative cost; at a state or national level, carbon pricing or environmental goals may lead to significant subsidies and incentives for WTE operators.— Technology competence: either in plant design and/ or operating competence can make a large difference to the techno-economics of a project. We may well be witnessing some technology breakthroughs (see discussions below) but these generally remain scale constrained as prototypes and/or as closely guarded commercial secrets.— Location: waste composition and waste management practice differ notably between high-income regions and low-income regions, where financing even basic solid waste management systems is a significant challenge5. A WTE plant might benefit greatly from advanced pre-processing that reduces feedstock variability. This makes a significant difference to advanced, high capex projects.Landfill gas (LFG) Waste management currently accounts for some 12% of global anthropogenic methane emissions, with roughly two thirds coming from solid waste and the remainder from wastewater treatment6. There are considerable regional variations. In the US, for example, landfills were responsible for 15% of the nation’s methane emissions in 20197. There, and in China, recovering of LFG is on the rise, while in Europe, LFG recovery is in steady decline in line with the EU’s policy aim to limit the share of municipal waste to landfill to 10% by 2035.19TECHNOLOGY PROGRESS REPORT Energy Transition Outlook 2021Solid waste in landfills typically decomposes anaerobically into LFG, comprising 40-60% methane, with the remainder CO2 and trace amounts of hydrogen and hydrogen sulphide. Recovery of LFG involves covering the landfill and extraction by a series of wells and a blower/flare (or vacuum). Cover systems have evolved from simple soil covers to near-impermeable multicomponent layers. The collected LFG can be cleaned and treated for use in electricity generation or further refined to produce biomethane.The World Bank estimates that globally 33% of waste is open dumped, while 37% is disposed of in some form of a landfill. One fifth of these are engineered or ‘sanitary’ landfills with gas collection systems8. There is considerable potential, therefore, for methane ‘mining’ in landfills worldwide. In the US, the EPA data shows that 20% of the country’s 2600 landfills have LFG energy projects in various stages of development, and there is potential for this number to double9.Tellingly, the biggest LFG company in the US, Archaea Energy, was recently (April 2021) acquired by the Rice Group, who funded the acquisition by selling their holdings in natural gas fracking. Rice explained the pivot by noting that LFG ‘mining’ of large landfills is a longterm investment involving 20-year contracts for renewable natural gas, currently priced at 5x natural gas. The income justifies investment in membrane technology to separate out CO2 and investigate the possibility of hydrogen production through SMR with CO2 sequestration in deep wells below landfills10.Incineration The World Bank estimates that 11% of waste worldwide is incinerated, although this ratio varies markedly by region. It is well established in Europe (42% of waste is burned), and is a growing waste management solution in Asia; China already has 300 WTE incinerators with another several hundred planned11. With the rising costs of landfills worldwide, the future would seem to be set fair for a growth in WTE plants. However, there are considerable restraints linked to the high cost of pollution control in WTE plants, the inhomogeneity of the waste itself and the need to match capacity carefully to waste calorific value to prevent financial drawbacks, and low electricity prices12.Even with high gate fee subsidies, incinerators will struggle to compete with lower-cost energy sources, particularly renewables. Incinerators also face growing public opposition, and campaigns for environmental justice have shuttered a number of incinerators located near low-income communities in the US13. Containerized incinerator plants for use in developing economies or remote areas to prevent open dumping or burning, and to produce power locally, sound like a good idea, but are far from commercial or technical readiness. A more viable growth possibility is through CCS which produces a net-negative result owing to the biological fraction of the treated waste, but development is contingent on high carbon prices.Biogas Biogenic materials typically represent some 70% of municipal solid waste, and it is that component that is broadly considered a source of renewable energy. It can be used as a feedstock for the production of biogas – as can a variety of organic wastes, including manure, sewage and industrial waste from slaughterhouses, dairies and breweries.The technology for biogas production – anaerobic digestion – is mature and need not be detailed here. However, there are persistent technology challenges in making robust, cheap, small-scale digesters for deployment in the developing world. Considerable success has been achieved recently in India with ultra-cheap biodigesters, fuelled with dung and food waste, constructed from durable geomembrane material14. In its SDS scenario, the IEA foresees an enormous growth in household-scale biogas generation – annual additions of over 5 million biodigesters in developing economies over the period to 204015. For this to occur, biogas projects require substantially more state support that recognizes the co-benefits of biogas as a fuel, especially when it replaces charcoal and wood-fired stoves, and the use of the digestate for soil amendment.While there are some concerns that waste reduction efforts and recycling could reduce biogas waste-to-energy projects, empirical studies suggest the opposite. The EU’s framework for waste management introduces a hierarchy starting with waste prevention, and then reuse20Waste to fuel and feedstock 3and recycling, followed by energy recovery from waste (incineration and biochemical treatment), and finally disposal. Even within this framework, research suggests that there is a potential to lift energy recovery from waste in the EU alone by an additional two thirds16. Europe already produces a little more than half of the world’s biogas, and the proportion of biogas sourced from waste is likely to grow given the EU’s concern that bioenergy production should not compete with food production17.Waste-to-fuels In the developed world, a more pressing concern than the availability of organic waste is that biogas might be constrained or edged out of the electricity market by the plunging costs of renewables and batteries. The focus is therefore likely to shift to further purifying biogas, removing CO2 (some 30-40% of biogas) and other trace impurities, including water vapour, toproduce biomethane. The most common biogas ‘cleanup’ technologies include pressurized water scrubbing, catalytic absorption/amine wash, pressure swing absorption, cryogenic liquefaction and highly selective membrane separation18. Biomethane (sometimes referred to as renewable natural gas) can be spiked into natural gas distribution networks and used in hard-to-abate sectors, not least industrial heat, aviation, trucking and shipping.Recent research in the US has shown that instead of producing biogas through anaerobic digestion of wet waste, methanogenesis can be arrested during fermentation to instead produce C2 to C8 volatile fatty acids (VFA) for catalytic upgrading to sustainable aviation fuel. This could open up a significant new feedstock for SAF, the commercial production of which is currently limited to hydrotreatment of esters and fatty acids from virgin vegetable oil and waste fats and grease19.A plant controller at Recycling Technologies, Swindon, UK, holding a bottle of Plaxx® - a liquid hydrocarbon feedstock produced by chemical recycling of waste plastic. After refinement, Plaxx can be used to make virgin quality plastic resin. (Image courtesy Recycling Technologies.)21TECHNOLOGY PROGRESS REPORT Energy Transition Outlook 2021focus here is on recycling technology. Clearly, however, the more efficient and profitable the recycling process, the greater the incentive to collect post-consumer plastic waste.Recycling Technologies' RT7000 modular plant for feedstock recycling of plastic waste by thermal cracking. (Image, courtesy Recycling Technologies.)Gas can also be produced thermochemically from organic waste via gasification to produce syngas (hydrogen and carbon monoxide) which can then be converted by the Fischer-Tropsch (FT) process into long chain hydrocarbon molecules that make up higher end fuels such as synthetic diesel and bio-jet fuel. Barriers to thermochemical treatment of waste have been scale and cost, but there have been several breakthroughs in recent years. Among the more successful is BP’s US-based Fulcrum bioenergy, using so-called ‘baked bean can’ reactors and a proprietary catalyst to boost the commercial viability of FT technology20.Waste to feedstock (Plastics) It is roundly agreed that the worldwide plastic recycling rate of, at best,15% is unacceptable. Almost all of this is done by mechanical recycling, which, plainly, is not up to the job of dealing with the world’s growing plastic mountain. Without radical intervention, annual plastic waste globally will grow from 250 million tons in 2020 to close to 350 million tons in 203021. This chapter does not cover the collection and sorting of plastic – whether mechanical or manual – which is a prerequisite for recycling of any kind. Challenges to collection, assortment and cleaning are largely policy linked, while ourMechanical recycling Although improvements have been made to mechanical recycling over the last 50 years, changes in chain length and material degradation during recycling remain consistent challenges across all polymers22. A number of solutions exist to prevent polymer chain scission during extrusion including antioxidants and chain extenders, but there is a lack of standards and knowhow as to the effect of these processes on the quality and safety of recyclates. Similarly, the presence of impurities in the waste plastic also leads to material degradation, and although solutions exist, for example degassing and filtering of the polymer melt, they do not wholly solve the problem. The principal difficulty with impurities is the need to presort polymers by type and colour; once sorted, however, individual polymers may still be contaminated by inks, glues, lubricants and by other plastics and paper used in labels. These issues affect even the most recyclable resin – polyethylene terephthalate (PET) – such that in PET bottle recycling, the virgin resin to recyclate ratio is often 70/30 by weight23.Mechanical recycling is very rarely ‘bottle for bottle’ recycling, and much of what is called recycling is in fact downcycling into secondary products such as textiles, carpets and building materials. Once included in these products or as layers in packaging, recycled plastic becomes more difficult to recycle again – owing to further chain shortening, and difficulties with sorting and contamination. After a few cascading cycles, the plastic becomes suitable only for incineration or landfill.Despite the growing demand for recycling, with targets set by leading brands for recycled content and a substantial tax recently placed on recyclable plastic waste by the EU and the UK, the techno-economics of recycling remain challenging24.Chemical recycling Many, if not all, of the challenges facing mechanical recycling are solvable through chemical recycling of waste22Waste to fuel and feedstock 3plastic. There are a number of chemical recycling methods, but broadly speaking it involves depolymerization of waste plastic through pyrolysis, or through the use of solvents or catalysts, and the repolymerization of monomers into virgin-quality resins (‘feedstock recycling’) or other useful petrochemicals, including fuels for transportation. Moreover, chemical recycling can be applied to a mixture of plastic waste, including the large percentage not covered by mechanical recycling, without the need for pre-sorting.With these advantages, chemical recycling should be taking off like a rocket. And that is true to some extent: the American Chemical Society lists 66 ‘advanced recycling’ projects announced in the US alone since July 201725. It stands to reason therefore that there are hundreds of chemical recycling projects active worldwide. Does this mean that a wave of technological change is building that will disrupt and transform an industry that hasn’t changed substantially for the last 50 years?In the developing world, enormous potential exists for an expansion to small-scale biogas to displace traditional, biomass-fuelled cookingChemical recycling has strident detractors, including Greenpeace26. The principal objection is that chemical recycling is being used to produce fossil fuels. While that is true, DNV takes the view that the production of fuel from waste plastic is preferable to no recycling at all.The carbon footprint of pyrolysis is also listed as a concern. Pyrolysis generally requires high heat, which is typically supplied by burning a proportion, some 10% of by weight, of the waste plastic. However, there are ongoing efficiency improvements being made, including the reuse of non-condensable gases from the pyrolytic process to heat the reactor. In addition, the carbon black pyrolysis by-product can be sold to cement plants and refractories. Definitive, full life cycle analyses (LCAs) are difficult to come by for this young industry, but there is no doubt that improvements can, and will, be made, including the possibility of using renewable electricity.Finally, the commercial viability of chemical recycling start-ups is questioned. As with any industry start-up phase, a high number of failures is to be expected. However, DNV is aware of several examples of chemical recycling firms that are enjoying considerable commercial success, not least because they are partnered with or backed by global brands. These include Agylix in the US, the Dutch start-up CuRe Technology and Recycling Technologies in the UK. Recycling Technologies in particular addresses a key business model challenge, which is that plastic recycling should be done where the waste is generated – hence the development of a commercially viable, containerized pyrolysis plant, the RT700, designed to recycle the volume of plastic waste typically produced by a medium-sized town.DNV perspective We expect significant progress over the next five years in waste to fuel technologies, and, in the case of plastics, waste-to-feedstock via chemical recycling. However, achieving meaningful scale needs to be accelerated, and requires industry collaboration, standards development, and ‘joined up’ policy support from governments. In developed countries, LFG and anaerobic digestion biogas will remain long term primary energy sources, but there is growing emphasis on the production of biomethane and as fuels for hard-to-abate sectors. In the developing world, enormous potential exists for an expansion to small-scale biogas to displace traditional, biomass-fuelled cooking.Chemical recycling is likely to scale and complement other aspects – reduction and substitution – of the War on Plastic such that demand for virgin resin from oil and gas sources will flatten and then decline over the next 30 years. Finally, comprehensive understanding of the full life cycle of recycling options is needed. For example, biodegradable alternatives to single use plastic are predicted upon the idea that the material will in fact be left to biodegrade after use; our analysis shows that it is likely to end up as biogas, and hence be burned as a fuel. That compares unfavourably with (potentially) infinite cycles of chemically-recycled resin, especially if the original plastic item was bio-derived. In such cases, chemically-recycled bio-derived plastic could become an important net-negative contribution to decarbonization.23TECHNOLOGY PROGRESS REPORT Energy Transition Outlook 20214 PIPELINES FOR LOW-CARBON GASESWith stakeholder pressure increasing, and governments passing net zero legislation, industry is accelerating its solutions for decarbonizing production and consumption of the molecular energy – hydrocarbons – that the world needs. Pipelines will play a critical role in transporting this energy, but carry safety and financial risks if new design, construction, and operational considerations are not taken into account.Why do we still need pipelines? Although great strides are being made in decarbonizing the electricity and transport systems through renewable power and EVs, the energy sector still relies heavily on molecular energy. The DNV ETO1 forecasts that some 50% of the energy system will still be hydrocarbon based in 2050. Pipelines will remain critically important for transporting molecular energy from the point of production or storage to the point of consumption.Pipelines are also being used in new applications like transporting lower carbon materials such as hydrogen, or assisting in industry decarbonization through Carbon Capture Utilization & Storage (CCUS) by transporting CO2 from emission locations to permanent storage or end use locations.Will we need more pipelines? Increasing capacity by repurposing existing infrastructure for gases such as hydrogen and CO2, rather than constructing new pipelines, can reduce both project riskand commercial burden. However, these projects are mainly at the pilot stage. Larger-scale deployment of hydrogen and CCS is likely to require linking production and CCUS, through hubs and newly-built “backbone” pipelines that connect facilities that previously would not have had any reason for being connected such as steelworks, chemical plants, and power stations. In addition, many inland facilities will need to be connected to coastal hubs for hydrogen supply or CO2 export.The DNV ETO and the International Energy Agency2 forecast CCUS demand in 2050 will be roughly 100 times larger than collective capacity of the roughly 6,500 km of CO2 pipelines that exist today.What is different about these new gases? Many design, construction, and operational considerations go into developing future low-carbon gas pipelines. Research is underway to determine how new and existing pipeline materials will react to the different compositions, pressures, and temperatures these24Pipelines for low-carbon gases 4TABLE 4.1 Key considerations for new and repurposed hydrogen and CO2 pipelinesHydrogenRepurposed• Pipeline velocities • Pipeline cleanliness/hydrogen purity • Metering • Repair system design • Brittle fracture mechanisms in steel lines • Toughness and tensile strength parameters • Cleaning/purging of existing lines • Area classification of electrical systems • Update emergency response plans • Impact on compressorsNew• Pipeline material selection, steels, plastics, composites • Gas/Syngas composition • Pipeline routing and permitting • Public consultation • Metering • Pipeline sectioning • Autoignition risk on depressurisation • Welding/jointing issues • Valve design and selection • Compressor design and selectionCO2• The design pressure & temperature of the pipeline• Pipeline routing and permitting.(avoiding the two-phase region)• Operating mode (gaseous, liquid or supercritical)• Impurities in the CO2 changing fracture propagation propertiesand mass density • Public consultation• Water dew point in the pipeline.• Possible cryogenic effects• Dense phase CO2 acting as a solvent (elastomer effects) • Fatigue/cycling effects• Pressure maintenance (boosting for long pipelines) • Startup/shutdown impacts• Life extension of pipelines• Metering• Blowdown/venting provisions• Pipeline sectioning• Cleaning/purging of existing lines• Linepipe selectionpipelines will operate under. Table 4.1 highlights some of the key considerations and different requirements for new and repurposed pipelines transporting hydrogen and CO2. Note that there are several features that are common to all options. DNV’s recommended practices provide full guidance on pipeline design and operation3, 4.CO2 pipeline issues CO2 transportation by pipeline links the process activities for capturing CO2 at an emitter facility (e.g., power station, steel manufacturer, refinery) and the activities needed to inject it deep underground for permanent geological storage. Critical issues are as follows:Impurities in captured CO2 affect critical pressure, critical temperature, and phase behaviour and have a significant impact on pipeline design parameters. When CO2 pipelines for CCUS applications were first considered,they were mainly intended to capture constant CO2 streams: post-combustion capture from coal-fired power stations or for pressurising existing oil reservoirs for enhanced oil recovery. These streams were not pure CO2, but the potential contaminants were generally consistent. The current demand for rapid growth in CCUS to support deep decarbonization of industry will result in CO2 being captured from a much wider range of emission sources, with a much broader range of contaminants than previously encountered. The pipeline network will have to establish clear standards for minimum CO2 purity and specify a maximum level of each potential contaminant. For repurposed pipelines, the inspection and operational history of the pipeline is necessary to understand which contaminants may be present, either from the fluids themselves or the interaction of the previous fluids with the pipeline, which could result in corrosion/erosion products.25TECHNOLOGY PROGRESS REPORT Energy Transition Outlook 2021Capturing CO2 from wide range of sources, many of which are geographically dispersed, introduces pipeline routing and Right of Way (ROW) issues. This will need to be studied and regulatory and regional authorities will need to be consulted to arrive at acceptable ROW rules. These issues are far more complex for onshore pipelines than offshore pipelines, due to the number of likely crossings and interactions.Pipeline capacity and size also needs careful consideration. It is tempting to design the pipeline for the maximum flow capacity that could be needed, but oversizing the pipeline carries significant risks given that industry may pursue fuel switching or technologies that could significantly reduce the demand for CO2 pipeline capacity. For example, if a major steel plant switched from blast furnaces to electric arc furnaces, or a blue hydrogen production facility were replaced by green hydrogen, CO2 transport demand would drop dramatically. Pipelines with small diameters can be used to transport high flow rates with sufficiently high velocities, but they may suffer high pressure losses and erosion of the internalpipeline wall. Larger pipeline diameters reduce pressure losses and have lower velocities, but they can be very expensive and risk becoming stranded assets.Transporting relatively pure CO2 as either a liquid or a gas is preferable to managing a pipeline flowing a two-phase, less pure mixture. It is preferable to transport CO2 either in the gas phase at about 35 bar or as a dense liquid phase above 100 bar. This must be carefully modelled to avoid CO2 phase changes along the pipeline by ensuring the CO2 is maintained at optimum pressure/temperature range. Fewer design optimization opportunities makes this a more difficult problem to solve in repurposed pipelines than in new pipelines.Contaminants and the need to avoid phase change in pipelines transporting CO2 away from industry emitters make metering and monitoring in CO2 pipelines even more important than in traditional hydrocarbon pipelines. Impurities have significant effects on the properties of CO2 and can present challenges not only in phase change, but also in fracture toughness and crack propa-FIGURE 4.1 The vapour cloud from a DNV test of CO2 pipeline failure at Spadeadam, UKFIGURE 4.2 Hydrogen Pipelines26Pipelines for low-carbon gases 4gation. CO2 flows are unlikely to be steady, so physical metering and pipeline monitoring will be essential for both single and multiphase flows. Further modelling and metering developments are needed to both forecast impacts and adequately monitor operating conditions.A leak from a large CO2 pipeline is potentially life threatening to people caught within the dispersing cloud. Figure 4.1 shows the outcome of a test conducted by DNV at its Spadeadam research facility to investigate CO2 dispersion following a pipeline failure. Major accident risks from CO2 pipeline systems can be low if rigorous hazard management processes are adhered to and the properties and behaviours of CO2 are adequately understood.Hydrogen pipeline issues As opposed to CO2, which can be considered as a waste stream, hydrogen is a valuable energy carrier and feedstock which can be used in a variety of applications. The purity requirements of the end application therefore have a significant impact on pipeline design parameters.While most industrial and domestic applications can accept a 98% purity level5, applications such as fuel cells, and semiconductor manufacturing typically require a 99.9999% purity. Pipeline design requirements may therefore need stainless steel construction, internal coatings, corrosion protection, and in-line filters. If repurposed pipeline records are not available, additional inspections may be necessary.The hydrogen atom is small and more prone to leakage compared with other hydrocarbons. Therefore, flanged joints should not be used in new pipelines and any flanged joints in existing pipelines should be replaced by welded joints. Hydrogen is also especially prone to auto-ignition of leaks and atmospheric vents. This is due to hydrogen’s low ignition energy and the fact that, unlike most gases, hydrogen increases in temperature when it expands. This tendency towards auto-ignition, combined with a difficult to see flame, make small hydrogen leaks a serious potential risk that require careful management.In its pure state, hydrogen has unique corrosion properties. When combined with even small levels of impurity (ppm), those corrosion concerns can increase dramatically. Many metallic materials — including steels (especially high strength steels), stainless steel, and nickel alloys — suffer embrittlement in hydrogen gas environments. Purity, temperature, and pressure can affect the severity of the embrittlement. Embrittlement can be avoided in most hydrogen transmission pipelines by operating at pressures below 85 bar and using low strength steels.DNV perspective The role of pipelines in a decarbonized future is often not well understood. As we move through the energy transition, and both industrial and domestic consumers move from methane to hydrogen, both older and new systems will need to operate side by side. Building these systems and vastly increasing CCUS network capacity will significantly increase the demand for pipeline expertise.Whether new or repurposed, a well-designed and maintained pipeline can safely transport low-carbon gases or CO2. The main challenge is the increasing need for pipelines to secure land use planning approval and societal acceptance, particularly in the onshore environment.27TECHNOLOGY PROGRESS REPORT Energy Transition Outlook 2021Energy infrastructure and nano materialsMuch of the energy landscape relies on the building of large infrastructure: drilling to great depths and piping fuel vast distances. Renewable power is also scaling up. The largest wind turbine now in operation is the GE Haliade-X, which has a capacity of 14 MW, and stands at 248 m tall1. It will soon be eclipsed by the 15 MW Vestas V236, standing at a height of 260 m high2.However, advances in technology on the smallest scale also have great potential to impact the energy sector. Nanotechnology has become something of a catch-all term to describe developments in science and engineer-ing operating on the nano- or micro-metre scale. In the case of material science, the effect of tiny features of a material’s greater structure has long been understood to have significant impacts on the whole component.As society focuses on sustainability, one of the potential areas in which nano-scale developments can support the energy sector is through the development of self-healing materials. An area of particular interest within civil engineering is the development of effective self-healing concretes. That may sound futuristic, but there is much that can be learned from the past.28Pipelines for low-carbon gases 4Recent scientific analysis has revealed that the incredible longevity of Roman harbour structures is due to a synergistic relationship between the concrete and seawater.Learning from the Romans Energy players are well aware of how harsh the marine environment can be on man-made structures. However, the Mediterranean has many examples of concrete Roman harbours dating back over 2000 years. Recent scientific analysis has revealed that the incredible longevity of these structures is due to a synergistic relationship between the concrete and seawater3. The salts present in seawater have reacted over time with the concrete, forming microscopic plate-shaped crystals which act as a reinforcement and creating a composite material. These crystals can flex when loading is appliedto the structure, preventing the concrete from cracking. This highlights the possibilities for offshore structures to benefit from their environment, rather than simply challenging it.Work is ongoing to develop modern equivalents of the Roman-style concrete and related novel approaches. For example, research projects are looking at incorporating bacteria into concrete mixtures with the aim of achieving a similar effect4. Some species of bacteria can convert calcium into the mineral calcium-carbonate. Bacteria are also extremely hardy and can survive being encased in concrete by entering a state of dormancy. When a crack forms in the concrete the ingress of water causes the exposed bacteria to become active, leading to the production of the mineral component which plugs the crack, maintaining concrete integrity.Learning from nature In this case the presence of bacteria is designed to have a beneficial effect, while more often the identification of bacteria and other microbes is a cause for concern. The issue of Microbiologically Influenced Corrosion (MIC) has long been accepted as part of the operating challenge in oil and gas infrastructure. Corrosion mechanisms can be accelerated by the presence of attached communities of bacteria onto a material surface – these are known as biofilms. If you have ever left some vegetables in the fridge long enough to accidentally produce a slimy deposit, then you already have some first-hand experience of how unpleasant these biofilms can be.29TECHNOLOGY PROGRESS REPORT Energy Transition Outlook 2021Renewable energy infrastructure is not immune to this issue, indeed any environment (unless sterilized) where water and metal meet will lead to the formation of a biofilm which could go on to cause MIC. Corrosion prevention is always preferable to curing an established issue. Here, nanotechnology offers some exciting possibilities for modifying the surface of pipelines or monopile structures to prevent the attachment of bacteria and even the presence of water which greatly reduces the corrosion risk. DNV is already supporting clients in the renewable sector who are experiencing corrosion issues in their offshore renewables infrastructure.Looking beyond the energy sector, preventing the adherence of bacteria to material surfaces is also of great interest to the medical community. Here, the challenge is to adapt the surfaces of materials that are known to be well-tolerated by the body to enhance their biofilm fighting capabilities. Borrowing from structures in nature, cutting-edge research into the effect of different microscopic patterns on the surfaces of materials, such as mimicking the patterns found on shark fins and crab shells, have been effective in reducing bacterial adhesion5. One such pattern has been developed into functional products which reduce the transmission of bacteria from surfaces such as door handles by adding a microscale surface texture6.Applications in the energy sector Despite these successes, the practicality of manufacturing pipe or structural materials on the scale needed for energy infrastructure using these novel surface patterning technologies is unlikely to make commercial sense. Rather, the ability to treat established materials to achieve the same effect is of far greater interest. Here, nano-material based coatings may provide interesting possibilities.Wettability is a term used to describe how easy it is for a liquid to maintain contact with a surface. Low wettability is a useful property for outdoor clothing and camping equipment, where water forms beads and rolls down a surface rather than saturating the fibres. Reducing the wettability of a pipeline surface, for example, reduces theinteraction of that material with any surrounding water. This has the dual benefit of reducing the risk of general corrosion, and making the surface much less hospitable for bacteria which reduces the risk of MIC.The potential to develop super-hydrophobic coatings that could be applied to existing assets would be of huge benefit to the industry.Super-hydrophobic coatings allow the modification of a wide variety of base materials, greatly reducing surface wettability. Researchers are exploring these coatings, which incorporate a broad range of nanomaterials such as titanium and silicon oxides for self-cleaning and anti-icing applications, as well as biofouling and corrosion reduction7. These coatings can be applied through several different routes including those suitable for mass production, such as dip coating.The “icing” of wind turbines can be hugely detrimental to their function and efficiency. Anti-icing coatings can be produced based on super-hydrophobic structures, as well as ice-phobic systems or electrically conductive carbon nano-tubes as incorporating nano-technology. These are all options for wind turbine manufacturers for the protection of not only the turbine blades from an icy build up, but also the telemetry and monitoring equipment that is a vital part of wind farm operation8. Another application where nano-materials based technologies are expected to make a huge impact is in the protection of components from the effects of wear9. The resulting increases in efficiency and possible life extension of treated components should allow operators to produce more energy while using the same amounts of raw structural materials.Though the addition of coatings such as these to new energy infrastructure is exciting, the potential to develop super-hydrophobic coatings that could be applied to30Pipelines for low-carbon gases 4existing assets would be of huge benefit to the industry. Developments in understanding the complex interactions between surface chemistry and different molecules has seen a rise in the production of self-assembled monolayers (SAMs). The great thing about SAM is that the chemistry of the components is designed to interact with the substrate material to create a regular ordered structure, on a molecular level, as part of the coating process. Tiny quantities of material form single layer structures that are commonly only tens of atomic distances wide, and yet their effect on the wettability of a surface is significant10. While not yet developed, a tantalising opportunity exists to develop a system by which a mixture of nano-materials and solvents could be used to “treat” an existing pipeline or vessel which could then benefit from enhanced corrosion resistance.Concrete is still widely used throughout the energy infrastructure, as shown here as the bases for someoff-shore wind turbines are inspected.31TECHNOLOGY PROGRESS REPORT Energy Transition Outlook 20215 MESHED HVDC GRIDSMeshed and multi-terminal HVDC grids are low impact, cost-effective methods for integrating large scale and remote renewable energy resources. While HVDC projects are limited by onshore grid compatibility and a lack of interregional and international cooperation models, HVDC grids in Asia have demonstrated their technical feasibility. In this chapter, we discuss various methods for HVDC grids and potential barriers to their implementation.Offshore wind turbines (Denmark) with substation in the foregroundRenewable energy integration To meet IPCC climate targets, we need a grid that can support ever-expanding renewable energy resources. Offshore wind in particular is growing quickly. The European Commission strategy seeks to increase Europe’s offshore wind capacity from its current level of 12 GW to at least 60 GW by 2030 and to 300 GW by 20501. The US is planning a large rollout of offshore wind with 30 GW to be built by 2030, mostly off the New York coast.However, onshore grids are not yet ready to handle this scale of offshore wind energy buildout. Integration and interoperability concerns include connection methods, available technology, balancing local and regional needs, interconnectivity, market coupling, cost, and other parallel emerging technologies.Connection concepts HVDC technology – Connecting and integrating the growing capacity of renewable energy sources requires overhauling the existing onshore transmission grids and building entirely new transmission systems in remote and difficult to reach areas such as offshore and deserts. The need to cover long transmission distances with ever increasing transmission capacities is driving a rapid uptake of HVDC transmission technology. HVDC transmission systems have low losses and are highly controllable compared with traditional AC systems. These properties inspire visions of super-grids which span continents and connect renewable energy resources to load centres across multiple national borders. These super-grids can carry out multiple32Meshed HVDC grids 5transmission functions, including exporting renewable energy from remote sources, supplying remote loads such as offshore oil and gas platforms, reinforcing onshore AC synchronous grids, and integrating energy markets by enabling energy exchange and trade across national borders. Figure 5.1 shows three possible arrangements of HVDC systems.Point-to-point HVDC systems – Traditional HVDC systems are built to serve a single purpose. This is typically accomplished with point-to-point systems with converters at each end of the HVDC line or cables. Such systems can be developed as a single project and procured from a single vendor. Multiple point-to-point systems can be built in parallel or in series and coupled at the AC side to increase the link capacity or distance. A contingency on one of the DC links can be selectively cleared by opening the AC converter breakers on either end without affecting the other connected point-to-point HVDC links. However, incrementally building grids consisting of separate point-to-point HVDC links requires a large number of converters which are costly to build and operate and incur a significant power loss.Multi-terminal HVDC systems – Multi-terminal HVDC technology couples multiple parallel or series HVDClinks on the DC side, instead of on the AC side. These systems minimize the number of converters needed and optimize asset utilization by combining many transmission function systems. This reduces both development and operating costs.There are two basic multi-terminal network topologies. “Radial multi-terminal” HVDC, has no parallel DC transmission paths (i.e., any two terminals or nodes are connected by at most one transmission path). If there is an outage in one path, there are no redundant parallel paths to guarantee continuity of supply (this is the case in the N-1 redundant AC transmission systems onshore). Several radial multi-terminal HVDC grids with up to 5 terminals are in operation today in China and more are under development in Europe.The second HVDC topology, ‘meshed multi-terminal’, does have parallel DC transmission paths, and can continue transmission even when one of the transmission paths experiences an outage. Full N-1 redundancy can be achieved if the parallel paths have sufficient redundant capacity. Currently, only one meshed multi-terminal HVDC grid with four terminals is in operation in China.Multi-terminal HVDC grid protection – One important design parameter for HVDC grids is the maximum lossFIGURE 5.1 Possible configurations of HVDC systems====Point-point systems — Easier project development– Single vendor procurement – Singel purpose — Mature and widely applied==Radial multi-terminal system — Fewer converters– Lower cost – Lower footprint – Lower losses — A few projects in opration==Meshed multi-terminal system — Reduced impact on AC grids — Requires DC protection systems — One full-scale demo project incomissioning33==TECHNOLOGY PROGRESS REPORT Energy Transition Outlook 2021of infeed at the connected AC grids. The single largest contingency in the HVDC grid, such as a cable fault, should never exceed the maximum loss of infeed at an AC grid interface. This is automatically the case when the total transmission capacity of the HVDC grid to a synchronous zone does not exceed the local maximum loss of infeed. In case of radial multi-terminal HVDC systems, this puts an upper limit on the ratings of individual HVDC circuits and requires selective fault clearing (protection) within the HVDC grid.Selective fault clearing splits the HVDC grid in case of an emergency. This allows the unaffected part of the grid to continue operation, limiting the size of the contingency and the maximum loss of infeed. In meshed multi-terminal HVDC grids, the protection system also automatically reroutes the power transmission to a redundant path to ensure continuity of transmission of all or some of the power. Meshed multi-terminal HVDC grids are therefore more applicable to situations where no loss of power can be permitted (e.g., supplying large load centres) or when individual circuit capacities exceed the maximum loss of infeed.Selective HVDC fault clearing requires state-of-the-art equipment such as HVDC circuit breakers, fault blockingconverters, and high-speed switches. Standards and guidelines for integrating these systems are currently still lacking and real operational experience remains scarce and limited to China. Hence, their adoption and the implementation of large multi-terminal HVDC grids, remains rare in an industry which is often technically conservative.Cable capacity – In order to minimize cost and impact on the environment and local communities, multi-terminal HVDC grids should minimize the number and length of cables/lines by using cables rated for the highest voltage available. However, the maximum rating of produced cables is the limiting factor for HVDC grids with submarine or underground cable links. Currently, the highest available capacities are the 525 kV extruded insulation cable systems in development in Europe which provide up to about 2.6 GW of transmission capacity. This exceeds the maximum loss of total infeed of several European grid zones bordering the North Sea (e.g., UK = 1.8 GW, DK1 = 0.7 GW, NO = 1.2 GW, etc.), demonstrating the need for multi-terminal HVDC grid systems with fault clearing in Europe. A similar situation can be found in the northeastern US. Renewable energy targets that exceed current maximum capacity are driving development of higher rated power cables.FIGURE 5.2Voltage rating of various cable technologies in operation and under developmentUnits: Power per circuit 3 000 MW2 500 MWContinental Europe2 000 MW 1 500 MW 1 000 MW500 MWUKNordicsDenmark (DK2)220 kV 275 kV 400 kV 320 kV 400 kV 525 kV Three-core submarine cables Offshore HVDC systemsTechnical potential In development In operationSingle largest contingencyDrivers and barriers for multi-terminal grids – The transition in HVDC grid design from multiple interconnected point-to-point HVDC systems to radial multiterminal HVDC systems is motivated by the potential to reduce both investment and operating costs. Developing remote renewable energy resources, coupled with the need to strengthen existing transmission grids and integrate energy markets, creates a need for transmission systems like multi-terminal HVDC grid technology. The development of meshed HVDC grids, as compared to radial, is motivated more by technical and system integration arguments than by cost.Interoperability of onshore and offshore grids Offshore wind integration levels are approximately 10% of national capacity peak load with capacity factors of 39.5% by 2020 in first moving markets. This will increase to more than 25% by 2030 in a potentially weaker transmission grid situation, with large scale coal fired34Meshed HVDC grids 5stations decommissioned going forward. There is an opportunity for meshed and interconnected systems to accommodate even more offshore wind. Single offshore wind hubs of up to 3 GW will bring the overall system to its controllable limits. Here new market rules need to be developed to clearly define how power system responsibility will be shared between major actors in different control areas.DNV perspective The envisaged multi-purpose, multi-actor, multi-vendor, multi-national, and multi-terminal HVDC grids will notbe planned, designed, and built all at once. Instead, they will grow in a step-wise, organic fashion. The equipment and systems require technical, regulatory, and economic compatibility and interoperability. This should be achieved through a set of explicit technology and purpose-agnostic minimum requirements which all actors in the super-grid development adhere to. This will require far-reaching coordination on many different levels. Policymakers, grid planners, and designers will need to collaborate to determine regulatory agreements, functional requirements, technical parameters, and project aspects.Meshed Offshore HVDC grid in Europe – the PROMOTioN JIPThe challenges facing deployment of meshed offshore HVDC grids in the European Union encompass a variety of different aspects. The PROMOTioN (Progress on Meshed HVDC Offshore Transmission Networks) project has identified various necessary prerequisites including cost-effective and reliable converter technology; HVDC grid protection systems; Compact HVDC switchgear; and financial frameworks for infrastructure development.The absence of a coordinated deployment plan and a regulatory framework, as well as missing agreements between manufacturers, developers and operators of the grid also represent current obstacles to the deployment of a meshed HVDC offshore grid.The PROMOTioN project sets out to solve these challenges, with the ultimate aim of unlocking the full potential of Europe’s offshore resources.The PROMOTioN project, led by DNV, is funded under the framework EU Horizon 2020 programme and involves 34 partners from 11 different European countries, who have collaborated intensively over the last 4 years.The organizational structure of the project has been based on 15 work packages, each looking into different aspects of the challenges. By connecting key stakeholders from industry, academia, consultancies and transmission system operators, PROMOTioN both provides a platform for interdisciplinary development and increases acceptance of required novel technologies and frameworks. Further information is available at: https://www.dnv.com/ research/review-2020/featured-projects/promotionmeshed-offshore-hvdc-grids.html35TECHNOLOGY PROGRESS REPORT Energy Transition Outlook 20216 NEW BATTERY TECHNOLOGYLi-ion batteries have reshaped portable electronics, enabled EVs, and will be an essential part of the renewable energy infrastructure. First described in the 1970’s and commercialized by Sony in the early 1990’s for portable electronics, these lightweight and power-dense batteries have mostly replaced the old alkaline cells that powered the flashlights and radios of the 20th century. Manufacturing at scale has quickly reduced cost and increased the energy density of Li-ion batteries, making long-lasting portable electronic devices and EVs possible. Thanks to these improvements, we expect half the passenger cars sold globally in 2032 to be electric1.Lithium-Ion battery technology Most of today’s Li-ion batteries have a graphite anode and a cathode made of blends of metals such as nickel, cobalt, aluminum, manganese. During charging, lithium ions and electrons flow to the anode (the Li-ions through a liquid electrolyte and the electrons through an external electric circuit). When lithium ions arrive at the anode, they ‘intercalate’, settling between the layers of graphite structure without changing it. When the battery is discharged, this process is reversed and stored chemical energy is released as electrical energy.There is a trend to reduce or eliminate the amount of cobalt in cathodes for ethical and cost reasons (most of the world’s cobalt is mined in the Congo which has been heavily criticized for its unethical and environmentally damaging labour and mining practices). High cobalt batteries also have lower energy density which is not attractive to the EV sector. We have seen a shift in industry to NMC and NCA Li-ion batteries with smaller proportions of cobalt, and lithium iron phosphate (LFP) cells which contain no cobalt. Although LFP cells have lower energy density, they have gained in popularity for use in vehicles and home storage because of their increased safety, and reliance on iron which is more abundant than cobalt.Li-ion batteries have become a staple of today’s electronic society and research is continuing to improve energy density and reduce costs. The cost learning rate for Li-ion batteries has been 19% and is expected to maintain that rate going forward. Large companies like China’s CATL have made substantial investments in new battery technologies that will continue this trend. In 2020 Tesla CEO Elon Musk and SVP Drew Baglino held a ‘battery day’ event where they discussed several aspects of improvement including the introduction of silicon to batteries as part of their strategy2.Improvements in Li-ion technologies Research into Li-ion batteries is focused on improving energy density, size, and safety while reducing cost. Several of these areas of research address fundamental limits of the material currently being used in Li-ion batteries. In particular, changing the electrolyte and replacing the graphite electrode with silicon.Solid-state batteries replace the liquid electrolyte with a solid material. This could increase energy density and durability while removing the most flammable element of Li-ion batteries, making them ideal for high-risk applications like pacemakers. However, solid-state36New battery technology 637TECHNOLOGY PROGRESS REPORT Energy Transition Outlook 2021Li-ion batteries are currently much more expensive than traditional liquid-electrolyte batteries.Another approach is a lithium-metal battery which removes the need for a substrate to intercalate lithium on the anode. In this approach, lithium metal atoms plate themselves atop each other directly to form the electrode. Creating an anode predominantly out of active electrochemical material as opposed to structural material greatly improves energy density. However, this technology still has challenges to overcome. The design suffers from dendritic formations, which can potentially cause cell shorting along with safety concerns, and delithiation where reactions with the solid electrolyte material remove lithium atoms, reducing the useful capacity of the battery.The graphite in the anode can hold a limited amount of lithium ions, putting an upper bound on the energy density of graphite-based Li-ion batteries. Silicon holds lithium ions in much the same way as graphite but at approximately 12 times more lithium per unit weight. However, silicon expands 300% while doing so, whereas graphite expands only 10%. This expansion negatively impacts performance and causes physical degradation.Various approaches including graphene coated silicon nanoparticles may hold the secret to mitigating crystallographic expansion, while increasing the capacity of the anode and the overall energy density of the battery.At the larger system level, cell-to-pack technology is a new design principle which drops the process of aggregating cells into modules and modules into packs. This is a manufacturing and design philosophy that reduces packaging and wiring that doesn’t ‘add value’ but adds weight and cost3.New batteries - beyond Li-ion Today’s battery landscape is dominated by lithium, but alternative storage methods for low-cost, long duration storage are coming. These include non-battery storage and novel battery chemistries. While lithium may be the best battery chemistry for transportation and mobile applications, these new batteries are especially useful for stationary applications like grid scale energy storage.Flow batteries are a type of long-duration battery technology that work by flowing an electrolyte through a series of plates4. The fluid volume dictates the energy and the electrode plates dictate the power. There are aFIGURE 6.138New battery technology 6variety of flow battery startups at various stages of commercialization. Notable chemistries are vanadium redox, iron flow, and zinc-based. The difficulty with many of these systems is the movement of reactive liquids or liquid/solid slurries which challenge the pumps, valves, and seals needed to move these reactants. Compared with lithium-ion batteries flow chemistries also have lower round trip efficiencies.These new battery technologies have yet to overcome their design challenges and demonstrate commercial viability. For them to be successful in stationary energy storage, they must first demonstrate that lower USD/ kWh installed costs are possible. This is a prerequisite for competing against energy dense, efficient, and mass-produced lithium batteries.Electric Vehicles It is unlikely that EVs will move away from Li-ion battery technology in the foreseeable future. The energy density of Li-Ion batteries align well with mileage needs and notable advancements, like solid electrolyte designs and the adoption of new anode chemistries, are coming to production. We expect EV adoption to increase as costs continue to fall and vehicle range is extended.DNV perspective Beyond commercially available technology, there are also step-change improvements for lithium batteries which are moving from labs and R&D departments to prototype stage. These improvements will continue to reduce cost and increase energy density. Li-ion battery advances will be fueled by the massive increase in EV production and a continuous quest to lower cost and boost range. Long-duration energy capture is critical to fully meet the needs of the energy transition.In the future, we expect to see Li-metal anode batteries with solid electrolyte and high-nickel/low-cobalt cathodes for the performance EV sector and an LFP variant for low-cost lower range EVs and stationary applications. We may see a sector coupling with transportation and industrial heating via green hydrogen technologies for very long duration energy storage.Non-chemical storage technologiesThere are several companies looking to commercialize energy storage that uses potential energy associated with pressure, temperature, phase change, mass, and gravity5, 6. Many of these non-chemical storage options have lower round-trip efficiency than lithium batteries butmay provide low-cost solutions for long duration storage needs as renewable energy further penetrates the grid. One advantage they provide that batteries cannot is electrical ‘inertia’ which helps the grid maintain its frequency due to the spinning mass of a turbine or other rotor attached to a generator. If this sounds strange, consider that the only source of energy storage for the grid until recently was pumped storage which still accounts for the vast majority of installed storage capacity of over 150 GW globally.39TECHNOLOGY PROGRESS REPORT Energy Transition Outlook 20217 NOVEL SHIPPING TECHNOLOGIESOur Maritime Forecast to 2050 aims to enhance the decision-making of shipowners as they navigate the technological, regulatory and market uncertainties surrounding decarbonization. In 2020, we developed a library of scenarios, projecting fleet composition, energy use, fuel mix, and CO2 emissions to 2050. We modelled 16 different fuel types and 10 fuel technology systems. In 2021, we will refine and expand on this work, but for the purposes of the present report we have selected novel shipping technologies we have hitherto not covered in depth: fuel-cell technology and nuclear power. In the latter case, next-generation nuclear technology is not a near-term commercial reality for shipping, but there are important developments underway in both fission and fusion that make these technologies worth watching as one of many longer-term zero-carbon options for the world’s future fleet.Marine fuel cellsFuel cell technology has a long history, stretching back to the 19th century, but were first practically applied by NASA in space missions from the 1960s onwards. The technology was subsequently used for Air Independent Propulsion in submarines. Since the turn of the millennium, fuel cell technology has matured and is in commercial use in forklifts, standby generators/ uninterruptible power supply and combined heat and power systems. Fuel cells have advanced to near-commercial use for cars, buses, trucks and rail applications. The technology is a contender for the long-term decarbonization of aviation. Piloting of fuel cells for maritime applications has been ongoing during the last decade, but the use of fuel cells in shipping is still in its infancy.Fuel cells combined with alternative fuels such as hydrogen can efficiently reduce and even eliminate emissions and noise, while energy efficiency can be increased compared with conventional combustionengines. Furthermore, fuel cells have other potential benefits such as reduced maintenance, modular and flexible design, and improved part load operation efficiency. However, fuel cells come with significant disadvantages related to cost and durability. These challenges will have to be overcome before fuel cells can make a meaningful contribution to compliance with the stricter emission requirements that are being introduced to decarbonize shipping.In simple terms, a fuel cell power pack consists of the fuel being supplied from a fuel storage tank; a gas processing system; and, a fuel cell stack that converts the chemical energy in the fuel to electric energy (and heat) through electrochemical reactions (Figure 7.1). The fuel cell produces electric energy, and the onboard power system must therefore be designed accordingly, allowing for the utilization of the electricity produced.40Novel shipping technologies 7Fuel cell types A variety of fuel cell types are available, and their names reflect the materials used in the electrolyte membrane.The properties of the membrane affect the permissible operating temperature, the nature of electrochemical reactions, and fuel purity requirements. Depending on fuel cell type, an electrical efficiency of 50–60% is expected. Some fuel cell types operate at high temperatures, enabling heat recovery that can increase the electric efficiency to 70%. Some types of fuel cells can run on several fuels, including options such as LNG and methanol, as well as their bio-based and electro-based equivalents. This is predominantly the case for the high-temperature fuel cell types such as Solid Oxide (SOFC) and Molten Carbonate (MCFC). Low-temperature fuel cells such as Proton-Exchange Membrane (LTPEMFC) need hydrogen as a fuel, but other fuels can be used if reforming of these is deployed upstream of the fuel cell to produce hydrogen which can then be fed to the fuel cell stack. The reforming and purification process for low-temperature fuel cells using non-hydrogen fuels lowers the overall system efficiency and,importantly, does not contribute to decarbonization if the CO2 from the reforming process is not captured. The large number of processing steps will also impact the power density and transient response time of the overall system. For this technology, the direct use of hydrogen offers the highest energy efficiency on the ship.Fuel cell evaluation for maritime DNV2 has previously evaluated seven technologies, nd concluded that SOFC, LT-PEMFC and the hightemperature PEM cell (HT-PEMFC), are the most promising for marine use. The LT-PEMFC maturity is high, while moderate for the HT-PEMFC and SOFC (key characteristics, see Table 7.1). Testing and evaluation of these fuel cell types have been performed in projects focused specifically on marine usage. Use of MCFC has also been demonstrated by marine projects. The FellowSHIP project was the first large-scale installation and demonstration of a fuel cell in a merchant vessel, the offshore supply vessel Viking Lady. The project, which involved installation of a 320 kW MCFC system fuelled by LNG provided auxiliary power to the ship, reaching a total of 18,500 hours of operation.FIGURE 7.1 Basic principles of fuel cells (redrawn from FuelCellToday, DNV1)Vessel Membrane CathodeFIGURE 7.2The world’s first hydrogen-powered car ferry, Norled’s MF NESVIK, undergoing sea trials in March 2021. (Image, courtesy Westcon/ Økland foto.)HydrogenNatural Gas Ethanol Methanol AmmoniaHydrogenAirH2 H+ O2e-e-WaterCO2e41TECHNOLOGY PROGRESS REPORT Energy Transition Outlook 2021Fuel cells with low operational temperatures are more tolerant of dynamic load variations than high-temperature fuel cells. Smaller and medium applications in the short-sea segment may favour low- and medium-temperature technology, such as LT-PEMFC and HT-PEMFC. Vessels in the short-sea segment are typically smaller, with more varied operational profiles and a greater share of their time and energy is spent on purposes other than steady propulsion. For these ships, the shorter distances and highly variable power demands often make electric and direct use of H2 highly relevant. This is reflected by the world's first hydrogen powered car ferries (see Figure 7.2), planned to be put into operation this year in Norway.For application on larger deep-sea ships, which can more easily accommodate waste heat recovery solutions, high temperature fuel cell systems such as MCFC or SOFC should be explored. Deep-sea shipping comprises large ocean-going ships, and a very large proportion of their energy consumption relates to propulsion of the ship at steady speed over long distances. Combining fuel flexible high-temperaturefuel cells with a battery (or other hybrid configurations) and waste heat recovery solutions for deep sea ships will ensure a more flexible operation, reduce thermal strain on the fuel cells and increase the energy efficiency of the system. For deep-sea ships with high energy demand and long bunkering intervals, non-hydrogen fuels with higher volumetric energy density such as ammonia, methane and methanol should be considered. The demonstration of the world’s first high-temperature ammonia-based fuel cell systems will also be important for maturing the high temperature fuel cell technology, as well as for introducing zero-carbon fuels3. In addition, alternative bunkering arrangements and storage mediums for H2, such as Liquid Organic Hydrogen Carriers (LOHC), should be considered.Costs and uptake Currently, costs and lifetime of the fuel cell stack are the primary barriers hindering uptake of fuel cells for maritime applications. Recent literature reviews by DNV4 and Veldhuizen et al5. concluded that fuels cells are currently many times more expensive than internal combustion engines. This is due to significantly higherTABLE 7.1Key characteristics: Proton-exchange membrane fuel cell (PEMFC); high-temperature PEMFC (HT-PEMFC); solid-oxide fuel cell (SOFC)4.Technical characteristicsStack lifetime Electrical efficiency on hydrogenOperation temperatureTolerance for load variationsSensitivity of fuel impuritiesMaturityEnergy densityAir emissions reduction potential on hydrogen (GHG, SOx, NOx, PM)Relative cost (among fuel cells)PEMFC Moderate 50%-60% 50-90°C High High High HighLowHT-PEMFC Moderate 50%-60% 140-200°C Medium Low Low High100%ModerateSOFC Moderate ~60% 500-1 000°C Low Low Moderate ModerateHigh42Novel shipping technologies 7capital costs. That said, falling costs have been reported in relation to increased land-based uptake of some fuel cell technologies, and projections suggest further cuts in costs due to expected scaling up and mass production. The increased volume and weight of marine fuel cells compared with diesel engines has been a competitive disadvantage. This is compounded by the fact that fuel cells will use alternative fuels which also have increased volume and weight compared with conventional fuels.More work should be carried out assessing life cycle impacts of the different fuel cell types operating on various fuels, and comparing these to conventional internal combustion engine solutions. Studies have indicated that the manufacturing stage has a relatively large impact, and the environmental gains depend on the lifetime of the stack and recyclability of the stack6, 7.DNV perspective The future uptake of fuel cell technologies is hard to project owing to high market and regulatory uncertainties, as well as uncertainty in the anticipated reductionin investment costs for installing fuel cell systems onboard vessels. The most promising marine application in the short term are for short sea shipping such as ferries (e.g. LT-PEMFC), as well as for auxiliary/harbourmode solutions, where ships will benefit from reduced local and GHG emissions, as well as from the reduction of noise and vibrations. From the auxiliary/harbourmode solutions, it will also be possible, eventually, to scale up to hybrid fuel cell configurations for deep-sea shipping.Use of fuel cells with LNG as fuel could be an future option for deep-sea ships This is contingent on a significant reduction in the unit cost of installed fuel cells from today’s high levels, which could be achieved as the technology matures and productions is scaled up. Shifting gradually from conventional internal combustion engines and use of fossil fuels over to fuel cells on zero- and carbon neutral fuels will help the industry to meet the global GHG target trajectories set by IMO.Class rules and regulationsDNV published the first class rules for Fuel Cells in 2008 and other classification societies have followed suit. These rules include requirements for the design and arrangement of fuel cell power installations and the spaces containing such installations. They cover all aspects of the installation, from primary fuel supply up to, and including, the exhaust-gas system. Requirements for fuel storage and supply are not included in the Fuel Cell Rules. These requirements are covered by the Class Notations for the relevant fuels. Currently DNV has Rules for LNG, LPG, Low flashpoint Liquid Fuels (covering e.g. methanol) and is in the process of developing rules for ammonia. DNV is also looking into thesafety issues related to using hydrogen as fuel, with an aim to be able to develop prescriptive class rules in the future. Statutory regulations are fully developed for LNG as a fuel in the IGF Code, and Interim Guidelines for methyl/ethyl alcohols (methanol/ethanol) has recently been approved by IMO. Regulations for fuelcell installations are currently under discussion in IMO but has not been completed. Consequently, flag administrations will have to resort to the Alternative Design approach laid out in the IGF Code for approval of fuel cell installations using alternative fuels, and for all alternative fuel systems other than LNG and methanol. Class rules may be used to ease the alternative design approach mandated by the IGF Code if accepted by the flag administration.43TECHNOLOGY PROGRESS REPORT Energy Transition Outlook 2021Nuclear-powered shipsNUCLEAR FISSIONNuclear fission, the workhorse of the atomic age, is highly controversial due to its links with atomic weapons and accidents like Chernobyl and Fukushima. However, through ongoing innovation in small modular reactors, nuclear fission is, arguably, set for a comeback - driven by the need for baseload energy to complement renewable energy sources1. Could a nuclear renaissance benefit deep sea shipping?Technologies under consideration Nuclear power could be an effective way for the larger ships in the world fleet (container ships, bulk carriers, and possibly tankers and cruise ships) to cut emissions. A relatively small number of nuclear vessels would make a significant impact on global emissions. The largest 1,000 ships account for about 10% of global shipping emissions2, and about 0.3% of global emissions3. Nuclear power also scales well with minimal cost so ship speed can be higher (e.g., 30-35 knots) leading to reduced transit times and increased transport capacity. With the increased transport capacity, a nuclear-powered ship could also handle a larger portion of the world’s shipping demand, and as such have a positive environmental impact beyond that of the individual ship itself.Older nuclear power systems used pressurized water reactors (PWR), and have operated since the 1950s with very good safety record in naval and ice breaker vessels4. However, they require active safety mechanisms. New nuclear designs are inherently safe, meaning that a meltdown cannot happen even when active cooling/ control is lost.As we explain below, the Small Modular Reactor (SMR) concept covers many types of reactors. Among these are Molten Salt Reactors that boast unique safety features associated, which, as we detail makes them potentially attractive for deep sea vessels.Small Modular Reactors (SMRs) SMRs are currently the subject of Intense research and development efforts. The IAEA lists about 70 SMR designs in various readiness levels from conceptual design to operational, with 6 of those intended specifically for marine applications5. These reactors are small compared with traditional reactors, with power outputs from ~5 MW to 450 MW, and can be series-produced in factories and transported to the location where power is in demand. A single SMR could power smaller or remote locations, while several SMRs can be linked to power a large city. This makes them less expensive and more flexible than traditional nuclear reactors.Molten Salt Reactors (MSRs) Molten Salt Reactors have some unique and attractive features, but the technology is still immature. In an MSR, the fuel (e.g. Th-U or U-Pu) is a fluid, a molten salt, e.g. UF4 dissolved in Li2BeF4 (FLiBe). There are two categories of MSR design: open or closed fuel cycle.In a closed cycle, the reactor core may be fully enclosed and encapsulated. A secondary molten salt circuit, carrying no radioactive isotopes, flows through the reactor and extracts heat to be used directly in a steam turbine to generate power and propulsion. As such, containment in the reactor can be handled very well. The reactive fuel in a closed system can be changed every 5 years or so.In and open cycle, the fuel is added and extracted/ reprocessed during operation. Adding and extracting/ reprocessing fuel during operation is significantly more44Novel shipping technologies 7complex and requires a fuel reprocessing plant to handle radioactive material.As such, a closed cycle reactor is the most feasible on a deep-sea vessel as the likelihood of any leak can be made very small and reduces the proliferation risk since obtaining weapons material can only happen by extracting the reactor core from the ship.Liquid fuel provides some unique safety features.— First, a “freeze plug” is a reactor drain plug which must be actively cooled to keep the fuel in and the reactor running6, 7. If anything goes wrong, the reactor fuel is safely drained and the reaction stops.— Second, the molten salt intrinsically slows the reaction if it becomes overheated because it is a neutron moderator with small capture cross section and a negative temperature coefficient of reactivity7. This property also allows engineers to tune the reactor to the current power need (i.e., if the power requirement increases, more heat is extracted, temperature is lowered and the reaction rate increase, and vice versa if less or no heat is extracted).— Third, the operational temperature of MSRs is 600-700°C at ambient pressure, while the boiling point of the molten salt is ~1,400°C7. This is a large safety margin that makes the MSR inherently safe against melt-down and thermal runaway.The three fundamental nuclear safety requirements are control, cooling and containment, and in an MSR the control and cooling are covered by these inherent and passive features. MSRs have advantages over PWRs with regards to waste as well. Using low enriched uranium fuel, one producer, Transatomic Power, claims that less than half of the long-lived waste is produced compared to PWRs, due to higher utilization of the energy in uranium8. Although a less mature technology, thorium fuel reactors will produce even less waste with an even shorter half-life that requires only 300 years of storage9. As such, the thorium fuel cycle may be the best option for MSRs for shipping if and when this technology is sufficiently mature.Risks Historically, land-based nuclear power is among the safest and arguably cleanest ways of producing power10. Novel SMR and MSR technology with their inherent safety features seemingly have even fewer hazards than previous designs, although there is no consensus on this point. The Union of Concerned Scientists recently published a report claiming that novel advanced reactor designs such as MSRs, while being generally more sustainable, have novel hazards which make them significantly worse with regards to both safety and proliferation issues11. Public perception does not reflect the excellent safety record of existing nuclear, nor do proponents of novel nuclear concepts fully appreciate the associated novel hazards. However, considering the excellent historical safety record of nuclear power on land and at sea, and the promise of significantly safer reactor technology in the future, there is reason to think that the risks are manageable.The current licencing and regulatory regime for nuclear power may also pose a barrier. However, there is movement toward a revised international licensing procedure for small modular reactors, which alleviate this12.Nuclear proliferation risk is a concern for nuclear powered vessels, and while no nuclear technology has been shown to be completely proliferation resistant, several of the novel designs can potentially operate using unenriched uranium or thorium, or even spent nuclear fuel which is in storage today. The upside of using unenriched fuels is that enrichment facilities, which can make weapons grade uranium, can be avoided altogether. As such, nuclear technology on deep sea vessels should be chosen and developed to rely as little as possible on enriched fuels, and to produce the smallest possible amounts of weapons material in operation. In addition to technology that makes it hard and expensive to build weapons, there will likely still be a need for strict procedures and international oversight to keep proliferation well controlled.Cost Safety, reliability, and waste can be addressed suitably but cost remains a major consideration. A fair comparison for commercial nuclear shipping is zero emission alternatives45TECHNOLOGY PROGRESS REPORT Energy Transition Outlook 2021such as hydrogen/ammonia, synfuel, and possibly onboard CCS. Emblemsvåg13 presents an analysis comparing Thorium MSR (TMSR) with a 5-7 year refuelling cycle to HFO-fuelled two-stroke engines and finds that the investment cost of a TMSR powered ship is much higher, while OPEX is lower, and after about 8 years the TMSR-powered ship is cheaper. It is important to acknowledge that uncertainties are large and the that the comparison with HFO two-stroke is unfair considering the quest for zero emission technologies. Hydrogen or synfuel, with associated fuel infrastructure, are relevant examples that will be significantly more expensive than HFO 14. However, novel nuclear technology may be outcompeted for land use by very cheap solar and wind energy. As such the shipping sector, in which nuclear holds great promise, may not benefit from land-based nuclear developments.DNV perspective A SMR using molten salt reactor technology holds promise for reducing the emissions of the global shipping fleet. Additional and ongoing analysis will clearly be needed as the technology readiness level of modular nuclear technologies advances and as the cost of other zero emission solutions becomes clearer. Moreover, several novel reactor technologies need first to be developed and operated onshore before sufficient experience is available to guide the public perception, risk, and cost associated with taking shipping nuclear.NUCLEAR FUSIONPrivate companies are accelerating nuclear fusion technology towards commercial use in the current decade. As in the case for nuclear fission, shipping could benefit from developments in fusion.Illustration of a Tokamak fusion reactor 46Novel shipping technologies 7Advances in computing power, material science, and manufacturing, together with the rising availability of venture capital, have enabled recent progress in fusion technology. Once the domain of governmental players, private companies are now bringing much needed innovation as they seek to realize the potential of nuclear fusion as a zero-emission energy source. And, with nuclear fission reactors having a history of marine use, one could ask whether nuclear fusion could power ships in the future as well.Fusion reactors In parallel to the construction of the first large fusion reactor ITER15 aiming to begin Deuterium-Tritium operation in 2035, a group of well-funded start-up companies is working on small fusion reactors. Fusion reactors will be inherently safe, produce little radio active waste and have very low fuel costs (the main fuel, deuterium, exists abundantly in the Earth’s ocean: about 1 in 6,500 hydrogen atoms in seawater is Deuterium). From an operational perspective, all of these attributes make fusion tremendously attractive as a future source of energy. However, in contrast to fission reactors, a large amount of energy is needed to operate a fusion reactor, and thus far net positive energy has yet to be demonstrated with any fusion reactor.Current fusion reactor designs differentiate mainly on how the fusion condition with high plasma density and temperature for a sufficiently long confinement time can be achieved. In magnetic confinement designs, the density is very low, meaning that useful reaction rates require the temperature and confinement time to be increased. The best-known design is called Tokamak, employing a toroid that holds the plasma, and ITER is by far the largest example of this type, with about 50 experimental tokamaks operating today16. In inertial confinement designs, higher densities result in very small confinement time needs. Fusion is ignited by laser or x-rays and the largest reactor is called the National Ignition Facility17 located at the Lawrence Livermore National Laboratory in Livermore, California. There are also hybrid designs like, for example, magnetized target fusion which uses intermediate plasma density and confinement times, while plasma temperature is achieved with inertial compression. The start-upGeneral Fusion18 has an advanced design in this category and is the only technology today with a plausible way to harvest the energy.Market opportunities With the climate crisis at the forefront of society’s attention, zero-emission electricity generation needs to ramp up enormously. Renewables like solar and wind are predicted to grow exponentially over the next decades and replace existing thermal power production because they are more economically attractive. It remains to be demonstrated whether new generations of nuclear reactors can compete and add to these renewable sources.DNV perspective Even if small-scale nuclear become competitive with renewable energy, societal acceptance of nuclear power plants is certainly a risk in some countries, and it remains to be seen whether clean and safe nuclear fusion technology can sufficiently distance itself from fission to become acceptable.Private companies are now bringing much needed innovation as they seek to realize the potential of nuclear fusion as a zero-emission energy sourceSmall-scale nuclear could be an attractive replacement for small utilities running on gas and for remote installations. Other possible application areas are desalination plants, hydrogen production plants and mobile application such as, for example, large ships, offshore units, large floating multiuse platforms and, potentially, space vehicles. To explore this opportunity, a group of leading industry players including DNV have developed a concept for a fusion-powered large container vessel which is considered as an additional technical solution to advance decarbonization of maritime transport.47TECHNOLOGY PROGRESS REPORT Energy Transition Outlook 2021FUSION POWERED CONTAINER VESSEL (FPCV) CONCEPTThe general arrangement for a FPVC is based on the layout of a conventional 20000 TEU vessel. The main changes relate to the arrangement of the fusion engine amidships, below and forward of the deckhouse, in a sealed space. A steam plant comprising heat exchangers, steam turbines and generators is located adjacent to the fusion engine room. The nominal TEU capacity is reduced to 19,338 TEU compared to the reference ship due to a larger engine room below the deckhouse. Six electric motors in the aft engine room drive twin propellers. The auxiliary power plant is dimensioned to facilitate a cold start-up of the fusion system and is also arranged below the deckhouse.Fusion power plant The principal components of the proposed fusion power plant are the fusion engine, the fuel supply system including the plasma injector, the steam loop for the fusion engine pistons and the liquid metal loop connecting to the heat exchangers.A hazard identification has been performed and the highest risks to human life and property resulted from i) water ingress after a collision with liquid metal leaking to create a steam explosion, and ii) leakage of steam due to equipment failure. The highest commercial risk identified related to large volume of cooling water discharge in port which might not be acceptable.Economic analysis ULCVs trade today between east-Asia and Europe, passing the Suez Canal with frequent port calls. Average speed is about 18 knots. For FPCV, using its speed of 28General arrangement of fusion-powered container vessel. The fusion engine is located amidships in a sealedengine room below and forward of the deckhouse.(SCALE 1/1000)knots, trade routes with fewer port calls were considered, incl. round Cape of Good Hope (Table 7.3).Three fuel price scenarios were established for the reference case in the period 2031 to 2050, with a 1% annual increase. The low fuel price corresponds to a recent long-term crude oil price forecast by BP, while the high fuel price would be closer to the price of future alternative fuels.The cost-benefit analysis included capital costs (hull, outfitting, fusion plant, steam plant, electrical systems and motors) and operational costs (fuel, CO2, Suez Canal fees, maintenance, crew) as well as compensation for differences in TEU capacity and speed-induced inventory costs.FPCV offers lower cumulated costs than the conventional cases after 5 years, eventually saving about USD 1bn after 15 years compared to the reference case at reference fuel prices (Figure 7.2). The high/low fuel price scenarios change breakeven to 3/10 years, respectively. The difference of FPCV via Suez Canal and Cape of Good Hope is small.In summary, the fusion powered container vessel offers potential for lower transport cost, faster service and zero emissions to air. And fusion technology might offer an additional pathway for reaching IMO GHG targets while removing business uncertainty due to fuel cost volatility.About the partnership ABB, DNV, General Fusion, JMU and NYK agreed to explore the feasibility of a new technology promising1/3zero emission waterborne transport. They contributed according to their role in the industry.JAPAN MARINE UNITED CORPORATION WK -8/< 48TABLE 7.2 Principal dimensionsDeadweight at design draft (t) Container capacity (TEU) Ship design speed (kn) Propulsion power delivered (MW) Auxiliary power installed (MW)TABLE 7.3 Trade route and scenarios Route identifier Vessel Vessel average speed (kn) Roundtrip length (nm) Port calls per roundtrip Roundtrip time (h) no vessels, weekly dep.Novel shipping technologies 7Reference157 700 20 166 23.0 67.0 10.0FPCV147 700 19 338 28.0 92.8 20.0Traditional Conv 1822 652 111 848 11Reference Conv 1821 137 51 680 10SUEZ FPCV 28 21 137 5 1 176 7CAPE FPCV 28 28 071 5 1 344 849TECHNOLOGY PROGRESS REPORT Energy Transition Outlook 20218 EVs AND GRID INTEGRATIONTransport is a significant contributor to CO2 emissions and currently accounts for 27% (118 EJ) of global energy demand, with more than three quarters of that coming from road transport. By 2050, vehicle numbers on the road will have risen by some 60%, yet their energy demand will have dropped to 84% of today’s levels because of the EV revolution over this period. The three major drivers of this revolution are decarbonization, air pollution control, and cheaper EVs.50EVs and grid integration 8A typical battery-electric vehicle (BEV) today produces less than half the CO2 emissions of an average European passenger car over its lifetime (including manufacturing)1, 2. To reduce pollution levels, more than 30 cities globally plan to ban diesel and petrol vehicles by 2025 or 2030. The cost of battery packs is reducing by 19% for every doubling of production, resulting in passenger EVs achieving total cost of ownership parity with internal combustion engine equivalents next year.Car and battery technology In the early 1900s, approximately a third of vehicles on the road in New York city were electric. They were swifter to start and easier to drive than the noisy internal combustion engine (ICE) alternatives. However, as the cost of ICE vehicles fell with the Model T Ford and the starting issue – having to hand crank the engines – was resolved, ICE vehicles began to dominate, and have continued to do so through to the present.EVs only started to reappear in showrooms from around 2008, with performance and costs made possible by the development of lithium ion battery technology – largely driven by the consumer products industry. Yet uptake of these first models was tentative as real-world chargingand range issues became apparent, and high ticket prices limited sales to adventurous early adopters. Ten years on, the scene has changed dramatically. Advances in lithium ion (Li-ion) battery chemistry (see chapter 6), cell design, and battery management systems, combined with huge growth in production volumes, have led to cell energy density going from 150 Wh/kg in 2010 to 300 Wh/kg today and battery pack costs dropping from above 1,100 USD/kWh in 2010 to approximately 140 USD/kWh today. This combined with highly-specific BEV designs, improvements in motor efficiency, and the use of heat pumps for controlling cabin temperature, have led to the latest mass market passenger BEVs with total cost of ownership almost equivalent to a comparable ICE model and with ranges of 400 km or more.Within 5 years we expect passenger vehicle battery costs to be below USD80/kWh, average pack size to be above 100 kWh, and average vehicle range to be above 600 km. Assuming continued government incentives for EVs, we expect a massive switch to electric propulsion: in Europe, 50% of new vehicles sales will be BEVs by 2026, with North America, China and OECD Pacific following shortly thereafter (Figure 8.1).51TECHNOLOGY PROGRESS REPORT Energy Transition Outlook 2021Charger technology All these EVs will need a significant development and deployment of EV charging infrastructure. This technology has progressed from largely low power domestic charging to a broad range of options from 3.6 kW AC charging at homes and offices up to 350 kW DC chargers at dedicated en route charging locations. For electric buses and other commercial vehicles there are chargers currently able to provide 1 MW, and for ferries this goes up to as much as 10 MW. The typical AC and DC charging solutions implemented today can be summarized as follows:AC Charging Enabled by an AC/DC power converter onboard EVs, AC charging uses either a single phase or a three phaseAC connection. The charging power level is limited to 43 kW due to space and weight restrictions in the vehicle.Mode 1: Slow AC charging via a regular electrical socket, no communication between the vehicle and the charging point.Mode 2: Slow AC charging from a regular electricity socket, with In-Cable Control and Protection Device (IC-CPD).Mode 3: Slow or semi-fast charging via a dedicated electrical socket (a wall box or a charge pole) commonly used for public charging stations. The charging station is responsible for the control, communication and protection of the charging process, and can facilitate integration with smart grids.MODE 1AC MODE 2AC MODE 3ACControl & Communication Control & Communication52MODE 4ACDCEVs and grid integration 8Control & CommunicationCable connected to chargerDC Charging Mode 4: DC charging enables charging power levels beyond 50 kW for EVs. DC charging uses a dedicated electrical socket for EV charging like AC Mode 3, a charging cable permanently fixed to the charger, and the AC/DC converter is located within the charging station. The control, communication and protection functions are built into the charging station.Mode 4 chargers are unrestricted by space and weight constraints of onboard chargers hence charging power levels of 350 kW (or even higher) can be achieved. There are primarily four types of DC charging systems currently utilized globally:— CCS (Combined Charging System)/COMBO. The key feature of CCS chargers is the ability to use a single connector for both AC and DC charging by using separate pins within the same connector.— CHAdeMO. The charger has 3 power pins and 6 signal pins. CHAdeMO uses controller area network (CAN) protocol in the communication pins for signalling.— Tesla. The charger is unique because the two power pins that are present are used for both single phase AC and DC charging.— GB/T standard DC connector for DC charging in China. It utilizes 5 power pins of which 2 pins are for DC power, 2 for low voltage auxiliary power and one for earth.Trends that we see in the development of charging infrastructure technology largely fall into three categories: power; location and interoperability.The power of DC chargers for en route locations has increased significantly in recent years from 50 kW up to 350 kW and above, and will continue to increase over the next 5 years as the range of new EVs increases and wider adoption results in increasing demand for en route charging, including commercial vehicles. Onboard equipment will have to evolve to cope with higher power charging – for example moving from 400 V to 800 V systems – and improved battery technology such as solid-state batteries.Most charging is currently at home, and although this will continue to be the case, there will be an increasing share at other locations.We also expect a move away from drivers having to carry multiple membership cards for charging networks and instead have interoperable solutions with appropriate standards to produce a seamless ‘plug & charge’ experience.53TECHNOLOGY PROGRESS REPORT Energy Transition Outlook 2021Grid integration The EV revolution will have a significant impact on increasing electrical demand, and on the demand profile. Figure 8.2 shows approximately 36% of road transport final energy demand being met by electricity by 2050. This will require substantial investment to deploy charging infrastructure and integrate it along with new load into tomorrow’s power systems. EVs will greatly assist integration, their batteries being used to help balance supply and demand through load shifting and frequency response.With V2G, the EV batteries function as electrical storage for the network, capable of modulating the charging profile as well as discharging energy into the grid. We anticipate V2G deployment at locations of longer dwell time, such as the home and fleet depots. The flexibility allows EVs to participate in a set of services beneficial to the grid. V2G technology has the potential to provide significant benefits to multiple stakeholders including vehicle owners, the network, and society. These include increased system flexibility; reduced grid costs; and additional revenue for individuals and fleet owners.Over the coming five years we expect vehicle-to-grid (V2G) services to move from trial phases to become a nascent market for vehicle manufacturers, energy suppliers, aggregators, and grid operators.Over the coming five years we expect vehicle-to-grid (V2G) services to move from trial phases to become a nascent market for vehicle manufacturers, energy suppliers, aggregators, and grid operators. Currently, the only mass market vehicles that have bi-directional charging capability are from Nissan, but other manufacturers are conducting trials and Volkswagen board member Thomas Ulbricht stated in an interview in April that “Beginning in January 2022, every electric car from the Volkswagen Group that uses the MEB electrical platform will be able to not only charge from the electrical grid but also be able to return electricity to the grid on demand”3. Coming from a company that aims to sell one million EVs this year and become the global EV market leader by 2025, this is significant news.Although there are currently barriers to the uptake of V2G such as a lack of capable chargers and vehicles, uncertain revenue, and insufficient or undeveloped regulations, none of these are insurmountable and the benefits are significant – we have no doubt that V2G will play an important role in the EV revolution and the broader energy transition.DNV perspective The huge investments currently being channelled into EVs and their associated charging infrastructure, the fact that they are three to four times more efficient than ICE equivalents, their much lower impact on our planet and the flexibility they can provide to aid their integration – as well as that of renewables – means that EVs are a vital part of the energy transition, and one that will ultimately lower the cost of transport, reduce GHG emissions, improve the air around us, and improve grid reliability.There is major potential for utilizing V2G technology and the energy capacity in the vehicles to provide flexibility as the uptake of EVs increases worldwide. We forecast the total capacity of EV batteries by 2050 to be over 150,000 GWh, more than 5 times the energy capacity of all stationary energy storage, including pumped hydro.54EVs and grid integration 8The fully vehicle-to-grid enabled JuiceBox 40 Smart EV Charger by Enel X. Its ‘JuiceNet’ platform managing charging demand from thousands of electric cars across US. Enel X estimates that when over 3 million EVs are on the road, “our JuiceNet virtual battery could grow to an estimated 26 GW nationwide and displace 47 carbon-emitting natural gas ‘peaker’ power plants.”(Image: courtesy Enel X - enelx.com)55TECHNOLOGY PROGRESS REPORT Energy Transition Outlook 20219 GREEN HYDROGEN PRODUCTIONThe hydrogen economy is on the rise, and DNV expects global demand for hydrogen as an energy carrier to grow from practically zero in 2019 to 24 EJ/ yr in 20501. Uptake will mainly be in the manufacturing and transport sectors, adding to the continued non-energy uses of hydrogen such as fertilizer and feedstock. Our upcoming ETO 2021 includes carbon price sensitivity affecting the use of hydrogen, which leads to a further increase in demand.Green hydrogen — How? Green hydrogen is produced through electrolysis. At a basic level, electrolysis splits water (H2O) into hydrogen (H2) and oxygen (O2) by applying an electric current. The four main green hydrogen technologies are summarized below. DNV is involved in numerous projects applying these technologies and is in continuous contact with manufacturers to keep track of recent developments.Alkaline Electrolysis (AE) AE is the most mature electrolysis technology and has been applied extensively in the 20th century for ammonia and fertilizer production using hydropower. The main characteristic of AE is the use of a liquid electrolyte mixed with potassium hydroxide (KOH) to improve conductivity. Atmospheric AE, where the system operates and produces hydrogen at atmospheric conditions, is the most common form. There are also pressurized systems with a hydrogen output pressure of <40 bar. Many applications need pressurized hydrogen, and the higher output pressure saves costs and energy over using compressors. Pressurized AE is also better equipped to respond to changes in power input (e.g., from renewable energy). However, these benefits come at the price of slightly lower efficiency and more challenging design and maintenance.Proton Exchange Membrane (PEM) The first PEM electrolyzers were used for oxygen production in submarines, but since the beginning of this century they have been used to produce commer-cial hydrogen. PEM is characterized by its solid electrolyte (the membrane) and quick response times, and is usually pressurized. While still less developed, the technology made large steps and is reaching maturity. The costs are roughly 30% higher than AE but efficiency is on par. The stack lifetime is also expected to reach similar levels as AE (70,000-80,000 hours) and is close to achieving this with systems approaching 60,000 hours, PEM is already deployed at MW-scale with the largest plant in Canada of 20 MW2.Solid Oxide Electrolysis (SOE) SOE has reached commercialization and recent investments have led to competitiveness in the market and upscaling of production capacity. The technology is mainly recognized for high operating temperatures (500-900oC), high efficiencies, and the use of steam instead of liquid water. The technology is commercially available but is still far behind AE and PEM in terms of scale and maturity. Lifetimes are still limited to 20,000 hours and costs need to be reduced to compete with AE and PEM. Furthermore, stack capacities are still only a few kW while AE and PEM are >1 MW.A unique advantage of SOE is its capability to directly form syngas using co-electrolysis of steam and CO2, and to produce a mixture of hydrogen and nitrogen with co-electrolysis of steam and air. The latter is advantageous combined with ammonia production, saving costs on air separation units to produce nitrogen and the possibility to use waste heat for steam production. SOE is also capable of operating in reverse, acting as a fuel cell.56Green Hydrogen production 9Hydrogen productionMeeting the growing demand for hydrogen production shown in Figure 9.1 requires an unprecedented upscaling of capacity involving brown, grey, blue, or green hydrogen production. Although all ‘colours’ will play a role in the future, ultimately green hydrogen is the most sustainableand truly carbon-free option. Green hydrogen furthermore supports the business case of renewable energy. Large-scale electrolysis may provide a significant supporting role for balancing the electricity market during periods of surplus production – frequently characterized by low- or close-to-zero prices – alongside battery storage, pumped hydro, and demand side management.Hydrogen colour paletteColour code Energy sourceBrown Coal or ligniteProcess of getting hydrogenHigest to lowest greenhouse gas emissionslowest to highest acceptance levelGasificationGray Natural gasBlueAny non-renewable energy sourceGas reformationGas reformation or gasification and carboncapture & storageTurqoise MethanePyrolysisGreen Any renewable energy sourceElectrolysis of water57TECHNOLOGY PROGRESS REPORT Energy Transition Outlook 2021TABLE 9.1 Main parameters electrolyzer technologies, current and predictedCurrent | 2030aAEPEMLCOHb€/kg3.00 | 2.753.50 | 2.75Capex (10 MW)€/kW<1 000 | 500<1 500 | 500EfficiencykWh/Nm³4.7 | 4.34.8 | 4.5Stack lifetimehours8 000 | 100 00050 000 | >80 000Pressurebaratm. or 40 | 7040 | 70a: Future predictions based on manufacturer indications, literature or FCH JU targets. b: Over a period of 20 years with 8,000 hours of operation annually, an electricity price of 40 €/MWh, 3% O&M costs and a WACC of 8% (real). Lower electricity prices will reduce LCOH even further.SOE 5.00 | 2.802 500 | <1,000 3.6 | 3.320 000 | >20 000 atm. | 20AEM -4.8 stack 5 000 35Anion Exchange Membrane (AEM) The least developed technology is AEM which is still in the phase of research and development. A system is commercially available but is only 2.4 kW3. This is far from the MW-scale required to produce hydrogen as an energy carrier or feedstock. The technology looks promising though because it shares a similar simple design as PEM but doesn’t require critical raw materials. The main issues are instability and limited lifetime. Until now tests exceed only 2,000 hours showing high degradation4. Some improvements could lead to a lifetime of 5,000 hours, but this comes at the cost of lower efficiency5.Developments It could be argued that AE will not see much more development owing to its relative maturity. However, the technology has a long track record, and the energy transition may provide a new development boost, with many doublings of its capacity, as AE must keep pace with other emerging technologies, particularly PEM.Both technologies are in a phase of performance optimization, focusing on efficiency, lifetime, and costs. While the optimization of one of these parameters usually occurs at the expense of the others, the goal is to reduce the levelized cost of hydrogen (LCOH). Our analyses show the main drivers for LCOH are the electricity consumption, investment costs, and degradation of the stacks. It is therefore no surprise that manufacturers focus on these three aspects.— For both AE and PEM, higher efficiencies are reached through thinner membranes, reducing internal resistance. Higher operating temperatures may also increase efficiency.— Improvements on plant equipment balance — the equipment for supplying power, water, and gas processing — will further increase efficiency.— Costs are reduced through larger capacities. Expected electrolysis plants approaching GW scale will allow for economies of scale.— Upscaling, standardization, and improvement of manufacturing processes will further drive down costs. Assembly is currently done manually but automation can be reached though standardized system design and upscaling of manufacturing capacity.— Further improvements include an increase of operating pressure to 70 bar for both pressurized AE and PEM.While AE and PEM are competing for commercial position, SOE has just entered the market via three manufacturers. SOE development mainly focuses on improving the stability and lifetime of the stack, increasing capacity, and reducing costs. Lifetime should be improved by reducing thermal cycling as much as possible and avoiding impurities such as silica, which cause electrode blocking. Higher capacities are also reached by increasing the cell area, the number of cells, and current density. In theory, there should be no major obstacles to making stacks of >1 MW, a significant increase compared with today’s stacks of <10 kW.58Green Hydrogen production 9Finally, costs are predicted to decrease by 50% solely on the basis of economies of scale6. This should enable SOE to compete with AE and PEM by 2030.AEM still requires the most development. The system is commercially available at present is too small to be commercially viable. Lifetime also needs to be significantly improved before it can start competing with other electrolysis technologies. The focus is therefore on achieving a stable membrane, which currently limits lifetime.A long runway for green hydrogen Cost competitiveness is currently the main challenge to green hydrogen. Electrolysis must compete with brown, grey, and blue hydrogen from relatively inexpensive fossil resources in the context of low CO2 prices. Consequently, hydrogen from fossil fuels is likely to play an important role in establishing hydrogen as a significant energy carrier. At some point, the upscaling and cost reduction in both renewable energy and electrolysis will render green hydrogen more competitive. We expect this to take at least another decade, and that cost parity is also contingent on government support. However, investors in brown, grey, or blue hydrogen shouldconsider the risk that green hydrogen will be more competitive before their assets are depreciated, especially in areas where low-cost renewable energy is available for electrolysis, since the cost of electricity is a key competitive factor for green hydrogen.The paths of different hydrogen colours will be dependent on available resources, policies, carbon prices, and the risks investors take – and all of these parameters will vary regionally (Figure 9.2). In last year’s ETO, we predicted that, initially, significant production of hydrogen will rely on fossil fuels, and that hydrogen from fossil fuels will continue to grow through 2050. After 2035, abundant renewable resources will lead to increasing production of green hydrogen.Electrification is replacing the role of carbon-intensive energy carriers and competing with green hydrogen59TECHNOLOGY PROGRESS REPORT Energy Transition Outlook 2021Simultaneously, electrification is replacing the role of carbon-intensive energy carriers and is competing with green hydrogen. It is generally believed that for low and medium heating temperature processes, electrification by heat-pump is a more efficient and less expensive option for decarbonization. This is most likely the case for low temperature (<100°C) applications like steam and hot water production however, not all processes are equally suited to electrification. Our analysis of Dutch industry found many processes that could allow for electrification, but require drastic modifications and show a higher total cost of ownership than hydrogen conversion. Hydrogen could be implem ented by replacing or retrofitting natural gas burners while the rest of the process equipment remains largely unchanged. These examples are foundin drying or baking processes such as in the brick and ceramics industry or smelting of glass. Similarly, imported streams of hydrogen, such as in refineries, could be relatively easily replaced with green or blue hydrogen.In contrast, directly delivering hydrogen to processes like fertilizer production – which will eventually be an important market for blue and green hydrogen – is more complicated. For example, the production of urea uses carbon and nitrogen streams from steam methane reforming which would be unavailable if hydrogen were directly delivered. These challenges add more uncertainty to industry decarbonizing methods and call for a more detailed bottom-up approach when assessing the most cost-competitive solution.Illustration of M4000 plant by the hydrogen firm, Nel — a scalable design that can be containerized. The M-series PEM electrolysers, featuring the new ‘Z’ stack, provide fast response times and production flexibility and are thus well suited for hydrogen generation utilizing renewable power sources. (Images courtesy Nel.)60Green Hydrogen production 9Electrolyser OEMs have little influence on electricity prices so the main tools for cost competitiveness in green hydrogen are economies of scale and improvements in the manufacturing process. This is the twin focus for manufacturers to drive down CAPEX. Upscaling is also needed as plans for large-scale electrolysis are growing and manufacturing capacity must grow to keep up with demand.Most notable is the target set by the European Commission to promote upscaling of electrolysis by setting a goal of 40 GW electrolysis in Europe and 40 GW in other parts of the world by 20307. This is a far cry from the roughly 3 GW/yr of the combined electrolyzer production capacity we have estimated through conversations with manufacturers and publicly available information. This capacity clearly needs acceleration, and manufacturers are already in the midst of upscaling campaigns, which vary from increasing the number of shifts to building larger or additional manufacturing facilities. Going with what has been announced publicly total electrolyzer production capacity should grow towards 9 GW/yr within 5 to 10 years or earlier if the market provides enough certainty.Other barriers to upscaling are the need for qualified technical personnel and the use of critical raw materials (CRM). Upscaling will create job positions that need to be filled, and there is a scarcity of qualified technicians at medium to high level needed to support the energy transition in general. Additionally, AE and PEM use CRM such as iridium, cobalt, platinum, and tantalum. All these materials are an issue, but iridium in PEM is especially concerning as large scale supply is constrained and a substitute is difficult to find. Manufacturers are aware of this and possible mitigation strategies include substitution, reduction of material use, and recycling. The latter has yet to be applied by manufacturers, as far as DNV is aware.DNV perspective Green hydrogen is one of the key roads to decarbonization. In the coming decade we see increasing cost competitiveness for green hydrogen from electrolysis by improving efficiency and decreasing capex. In areas with abundant renewable resources and low-priced electricity, the costs of green hydrogen will drop even further. DNV is involved in some projects in Latin Americaand Africa where we already see green hydrogen production costs in the range of 2-3 USD/kg using solar PV. This will further encourage a global green hydrogen import/export market. Hydrogen produced in areas with inexpensive renewable energy could be converted to a liquid, ammonia, methanol, or LOHC, and transported to, for example Europe, where inexpensive PV is less abundant. Here hydrogen carriers can be used directly or they could be converted back to hydrogen.AE and PEM are the most developed hydrogen technologies, but SOE and AEM may yet have a future. A role for all four technologies could be expected in different application areas. SOE will likely be applied in combination with a stable power supply, integrated with other processes in ammonia and synthetic fuel production, and possibly in reverse operation to convert hydrogen back into electricity.Successful development of AEM could allow the technology to join AE and PEM in applications across many sectors. Here electrolysis plants could be built onshore either as large centralized plants towards GW scale, or small and decentralized plants to supply local demand, in mobility for example. We might also see electrolysis offshore on (artificial) islands, platforms, or even integrated into wind turbines. Large wind farm operators are currently assessing the possibilities of integrating hydrogen with offshore wind. This introduces a whole new level of challenges and design concepts where systems need to be compact, highly reliable in offshore environments, and even more suitable for remote operation. In addition, fast-responding electrolyzers like pressurized AE, PEM, and possibly AEM can offer grid services to assure stable voltage and frequency levels.In Latin America and Africa, we already seegreen hydrogen production costs in therange of 2-3 USD/kg using solar PV. This willfurther encourage a global green hydrogenimport/export market61TECHNOLOGY PROGRESS REPORT Energy Transition Outlook 202110 CARBON CAPTURE AND STORAGE 2.0The IPCC and IEA stresses that large-scale implementation of Carbon Capture and Storage (CCS) technologies are a necessary part of reaching the Paris Agreement climate targets. Although CCS has long been considered an immature and risky distraction from other “better” decarbonization routes, today we see a renewed interest in this technology as it becomes an effective a tool for achieving net-negative emissions and transitioning to a net-zero emission future.Governments are implementing more effective climate policies and shareholders are pressuring companies to reduce their emissions. In response, DNV has seen a significant increase in commercial CCS project announcements and investment, especially in industrial sectors that have limited near-future technologyalternatives for abating large CO2 emissions (e.g., oil and gas, steel, cement, and waste-to-energy).In 2020, there were 26 commercial scale CCS facilities in operation across the globe capturing just under 40 MtCO21. The latest Net Zero 2050 IEA scenario requiresTABLE 10.1 The four major types of Carbon Capture Utilization and Storage technologies and their usesMain PurposeCCSCarbon Capture and StorageAvoiding CO2 emissionsBECCSBio Energy with CCSRemoving CO2 from atmosphereDACDirect Air CaptureRemoving CO2 from atmosphereCCUCarbon Capture and UtilizationUsing captured CO2 to replace the use of fossil carbonApplicationAchieve permanent CO2 removal?Contribute to circular economy?In industrial processes and power generationYesNoIn energy from biomass/waste andbiofuels (ethanol)StandaloneIn concrete curing synthetic fuels,polymers, EOR, greenhouses, and othersYes Yes, but only if the CO2 is stored geologically or used in EOR, concretecuring and mineralization.Yes, but only through to EOR, concrete curingand mineralization.NoYesYes, if the CO2source is biogenic(ie. from biomass)62Carbon Capture and Storage 2.0 10about 1.6 GtCO2 /yr to be captured globally by 2030, and 7.6 GtCO2 /yr by 2050. IEA forecast a marginal increase in the next 5 years, and rapid expansion over the following 25 years2.DNV also projects CCS to scale substantially over the next three decades thanks to the carbon price increase in Europe. However, because competitive carbon pricing in heavily industrialized countries such as China and India is not forecast to occur before 2035, DNV expects a more limited scale up compared with the long-term IEA scenario. DNV estimates that by 2050, CCS will account for only about 2.2 GtCO2 /yr3.Industrial CO2 capture The first part of any large-scale CCS project is capturing CO2 from an industrial facility. Mature CO2 capture technology exists for applying CCS to nearly all industries, but in recent years we have seen CCS focus shift away from the fossil fuel power generation sector to major industries like cement, steel, refining, hydrogen, and ammonia.The most established method for removing CO2 from gaseous emission streams is separation by chemical or physical solvents in a cyclic absorption-desorption cycle. Of these methods, amine-based solvents are most common. In the next ten years, we expect to see additional CO2 removing technologies scale successfully to commercial demonstration. These include advanced solvents for chemical separation, adsorption/desorption cycles using solid sorbents, supercritical CO2 cycles (e.g., Allam power cycle) for gas fired power generation, and indirect calcination for cement production.Current CO2 capture costs vary greatly across industries from USD 15 to 125 per ton of CO2, but these are expected to fall4. The largest savings will likely come from come from 1) the replication of projects and economy of scale, 2) process improvements, and 3) increased competition between technology providers. Widespread deployment of the technology is paramount to significantly reducing costs, where higher carbon prices will further strengthen uptake.CCS for Negative Emissions Negative Emission Technologies (NET) will offset the emissions from hard-to-decarbonize sectors and play a key role in restoring the atmospheric carbon budget. Negative emission can be achieved through Bioenergy with CCS (BECCS) or Direct Air Capture (DAC) coupled with geological storage. In the IEA Net Zero 2050 scenario, BECCS and DAC will need to be capture and geologically store approximately 1.9 GtCO2 /yr by 20505.BECCS captures CO2 from biomass energy generation processes (e.g., power and heat generation or biofuels production) and geologically stores it. Many bio-energy plants with access to a carbon transport and storage infrastructure could be retrofitted with BECCS which utilizes mature bioenergy and biofuel technology and can use the same CO2 capture technologies used for fossil fuel assets. The IPCC SR15 report emphasizes the role of BECCS in meeting climate goals by sequestering roughly up to 1 GtCO2 /yr by 2030 and 8 GtCO2 /yr by 20506. Worldwide, there are currently five active BECCS facilities capturing a total of 1.5 MtCO2 /yr7. The largest of these is the Illinois Industrial CCS facility in the USCarbon Capture Utilization and Storage (CCUS)connotes both a process for permanent CO2 storage and CO2 utilization routes where the CO2 is used for various purposes. Enhanced Oil Recovery (EOR) is the primary example of this. While CCS and CCUS are commonly used interchangeably, here we make a point of using CCS to emphasize that the primary focus of this chapter is on routes that lead to permanent storage rather than utilization.1 Definition of Commercial CCS facilities: 1) CO2 is captured for permanent storage as part of an ongoing commercial operation, 2) storage may be undertaken by a third party or by the owner of the capture facility, 3) the capture facilities have economic lives similar to the host facility whose CO2 they capture and 4) they must support a commercial return while operating and/or meet a regulatory requirement.63TECHNOLOGY PROGRESS REPORT Energy Transition Outlook 2021which captures up to 1 MtCO2 /yr from its bioethanol process8. Large-scale deployment of BECCS requires a sustainable bio-feedstock supply chain and similarly wide-scale deployment of CCS. A rapid scale up is possible using current technology and upcoming CCS infrastructures.DAC is a suite of technologies thatremove CO2 directly from the atmosphere. To achieve negativeemissions, DAC must be coupledwith permanent CO2 storage. The relatively low concentration of CO2 in ambient air (0.04%vol) comparedwith CO2 levels in industrial flue gases (5-30%vol) presents a bigIndustry facility with CO captureShip transportPower production with CO captureEnergy consumersCOIntermediate storageHydrogen production Hydrogenchallenge for DAC; lower concentrations require bigger installations and higher energy costs.Today, BECCS technologies can produce negative emissions at lower costs and larger volumes per site than DAC. Capturing CO2 through BECCS costs as little as USD 25/tCO2 (although some industrial processes can cost three times this) and a single facility can capture volumes of up to 1 MtCO2 / yr9. In contrast, capturing CO2 by DAC can cost as much as USD 600/ tCO2 and the largest DAC facility existing today only captures about 4 ktCO2 /yr10. This makes BECCS more economically attractive to investors looking to offset their emissions. Considering this, DNV expects BECCS to be the main NET technology in the short term.PipelineMonitoring1-3 kmCaprockCOPermanent CO storageIllustration of carbon capture from different industrial facilities and power production, transport by pipeline and ship, with geological CO2 storage. Image sourced from the Longship – Carbon capture and storage White Paper (Norwegian Ministry of Petroleum and Energy, 2020), originally sourced from Gassnova.64Carbon Capture and Storage 2.0 10CO2 transport and storage infrastructures Connecting CO2 sources to permanent geological storage sites is an essential part of the CCS chain. Today, CO2 is primarily transported through pipelines, but transport by ship and truck is also an option. Flexible CCS infrastructure using ship transport can adapt to future capture projects and storage sites. Ships are also preferable for smaller CO2 sources that cannot afford a dedicated pipeline.Studies have identified many suitable and safe sites for geological storage of CO2 across the world. However, sites must also be close to capture plants, and identification, assessment, and permitting of storage sites take up to 10 years. Therefore, short-term (e.g., 2030) development of CCS infrastructure will mainly occur in locations that already have tailored regulations (Northern Europe, North America, Australia).Building CO2 transport hubs in industrialized areas with access to storage sites under development, such as those in the Netherlands, Norway, UK, and Italy, will speed large-scale uptake of CCS by allowing industrial clusters to share transport and storage infrastructure, reducing costs and lead times. Norway’s Longship project, a public-private partnership that includes heavyweight businesses like Equinor, Total, and Shell, is currently building one of the largest ongoing CCS infrastructures11.If funded successfully, Longship will start by shipping CO2 captured from waste-to-energy and cement facilities to storage in offshore saline formations. They will later expand capacity by connecting new CO2 capture sites to this infrastructure. DNV has estimated that the costs of this value chain will fall by more than 50% as CCS scales from 0.8 MtCO2 /yr to 10 MtCO2 /yr12.CO2 Capture and Utilization CCU includes technologies that use captured CO2 for various purposes like synthetic fuel and chemical products, concrete curing, and algae. Permanently trapping the CO2 in the final product has the potential to positively impact climate change. However, methods that do not permanently remove CO2 from the atmosphere, or only remove it for a limited time, for instance utilising CO2 asan alternative carbon source to fossil fuels, have limited effect as a climate mitigation measure.The large-scale deployment of CCU technologies must be accompanied by a careful and a thorough life-cycle assessment of the utilization process’s carbon footprint. Although CCU could create a circular carbon economy and reduce dependency on fossil fuels, the scale-up potential in the short term is limited by economic constrains (e.g., higher costs of CO2 derived products compared to standard products) as well as the limited availability of conversion technologies that can process large volumes up to ktCO2 or MtCO2 at a single facility.DNV perspective CO2 capture technologies are mature and commercially available for large scale projects in all industrial sectors. Within the next decade, additional capture processes will reach commercial maturity. Capture costs, not technology, remain the major limitation for CCS implementation.Developing transport infrastructure and qualifying storage sites, is key to enabling CCS. In the coming years the development of CCS value chains is mainly expected in Europe which already has tailored regulations for CO2 storage as well as a favourable financial and political support.Atmospheric CO2 removal has limited application but can be accelerated by deploying BECCS at significant scales if supported by appropriate policies and certified offsetting methodologies. With the exception of EOR applications, CCU needs to develop commercially and technically before it can apply at significant scale (i.e. >500 kt/yr) to more than a few specific applications; for this reason it is not expected to be a major contributor to cutting CO2 emissions in the short term.CCS is growing at faster pace thanks to favourable conditions. However, the pace is not fast enough for a Paris-compliant energy future; that will require much more robust carbon pricing and other incentives at a global level. With the right support, CCS will be able to play the necessary role it has to aid the transition to a net-zero energy system.65TECHNOLOGY PROGRESS REPORT Energy Transition Outlook 2021REFERENCESChapter 11 DNV (2020), Energy Transition Outlook. Available: https://eto.dnv.com2 Equinor (2021) ‘Hywind Scotland remains the UK’s best performing offshore wind farm’. Press release, 23 March. Available: https://www.equinor.com/en/news/20210323hywind-scotland-uk-best-performing-offshore-wind-farm.html3 Renewables Consulting Group (2021) ‘France kicks off Brittany floating wind auction’. Perspectives, 13 May. Available: https:// thinkrcg.com/france-kicks-off-brittany-floating-wind-auction/Chapter 21 DNV (2021), Energy Transition Outlook (Forthcoming). Available: https://eto.dnv.com2 Smithsonian Magazine (2013) ‘Document Deep Dive: The Patent for the First Practical Solar Cell’. Written by Megan Gambino, 13 June. Available: https://www.smithsonianmag. com/innovation/document-deep-dive-patent-first-practicalsolar-cell-1-180947906/3 Lynch, Peter (2007) ‘2007: The Year of the Thin Film PV Stock’, Renewable Energy World, 2 May. Available: https://www. renewableenergyworld.com/solar/2007-the-year-of-the-thinfilm-pv-stock-48359/#gref4 DNV (2020) ‘Solar PV powering through to 2030’, in Technology Outlook 2030. Available: https://www.dnv.com/to2030/ technology/solar-pv-powering-through-to-2030.html5 Liang, Tian, S. et al. (2019) ‘A review of crystalline silicon bifacial photovoltaic performance characterisation and simulation’ in Energy & Environmental Science, Issue 16 Solar, Trina (2021) ‘BOS costs reduced by 6.3% – DNV GL reports on advantages of Trina Solar Vertex 210mm module with fixed tilt’ in PV-tech.org. 9 March. Available: https://www. pv-tech.org/industry-updates/bos-costs-reduced-by-6-3-dnvgl-reports-on-advantages-of-trina-solar-vertex-210mm-module-with-fixed-tilt/7 Hutchins, Mark (2021) ‘Tandem cells approaching 30% efficiency’ in PV Magazine, 30 January. Available: https://www. pv-magazine.com/2020/01/30/tandems-cells-approaching-30-efficiency/8 DNV GL (2016). Get Smart: Smarter strategies for operating solar assets. White Paper. Available: https://www.dnv.com/Publications/smarter-strategies-for-operating-solar-assets-69162Chapter 31 Kaza, Silpa et al. (2018) What a Waste 2.0 : A Global Snapshot of Solid Waste Management to 2050. World Bank: Washington, DC. Available: https://openknowledge.worldbank.org/ handle/10986/303172 UNEP (2015) IWMA: Global Waste Management Outlook. Available: https://www.unep.org/resources/report/global-waste-management-outlook3 Statista (2020). Projected waste-to-energy market value worldwide from 2019 to 2027. Available: https://www.statista. com/statistics/480452/market-value-of-waste-to-energy-globally-projection/4 KPMG (2019) Waste-to-energy: Green solutions for emerging markets. Available: https://home.kpmg/xx/en/home/ insights/2019/10/waste-to-energy-green-solutions-for-emerging-markets.html5 Kaza, Silpa et al. (2018) Op. cit6 Saunios, Marielle. et.al. (2020) The Global Methane Budget 2000–2017, Earth Syst. Sci. Data, Volume 12. Issue 3. Available: https://essd.copernicus.org/articles/12/1561/2020/#section37 EPA (2021) Landfill Methane Outreach Program (LMOP): Basic Information about Landfill Gas. Available: https://www.epa. gov/lmop/basic-information-about-landfill-gas8 Kaza, Silpa et al. (2018) Op. cit9 See https://www.epa.gov/lmop/lmop-landfill-and-project-database10 Forbes (2021). ‘Why the shale-fracking Rice Brothers are betting their SPAC on Zero-Carbon Landfill Gas’. Written by Christopher Helman. 8 April. Available: https://www.forbes.com/ sites/christopherhelman/2021/04/08/why-the-shale-frackingrice-brothers-are-betting-their-spac-on-zero-carbon-landfillgas/?sh=47d7407f956611 National Geographic (2019). ‘Is burning plastic waste a good idea?’. Written by Elizabeth Royte. 12 March. Available: https:// www.nationalgeographic.com/environment/article/shouldwe-burn-plastic-waste?cmpid=int_org=ngp::int_mc=website::int_src="/skin/images/loading.gif" data-original=ngp::int_cmp=amp::int_add=amp_readtherest12 Sintef (2019). ‘WtE – Producing new energy from old data – a Waste-to-Energy story’. Blog by Michäel Becidan. 2 September. Available: https://blog.sintef.com/sintefenergy/wte-waste-toenergy/6613 Power (2019) ‘Waste-to-Energy: A Niche Market in Decline?’. Written by Kennedy Maize. 1 June. Available: https://www. powermag.com/waste-to-energy-a-niche-market-in-decline/14 Nitaware, Himanshu. (2020) ‘This Startup’s Bio-Digester Helps 5000 Families Give up LPG, Saves 6 Million Trees’ for The Better India, 8 October. Available: https://www.thebetterindia. com/239446/sistema-bio-pune-startup-farmers-biogascheap-set-up-cost-company-savings-clean-energy-healthyhim16/15 IEA (2020), Outlook for biogas and biomethane: Prospects for organic growth, IEA, Paris https://www.iea.org/reports/ outlook-for-biogas-and-biomethane-prospects-for-organic-growthhttps://datatopics.worldbank.org/what-a-waste/16 Scarlat, N et al. (2019) Status and Opportunities for Energy Recovery from Municipal Solid Waste in Europe. Waste Biomass Valor 10, 2425–2444. https://doi.org/10.1007/s12649-0180297-717 European Environmental Agency (2009, last modified 2021) ‘If bioenergy goes boom — the switch from oil to bioenergy is not risk free’. Available: https://www.eea.europa.eu/articles/ if-bioenergy-goes-boom18 Leonidas Matsakas et al. (2017) Green conversion of municipal solid wastes into fuels and chemicals, Electronic Journal of Biotechnology, Volume 26, Pages 69-83, ISSN 0717-3458, https://doi.org/10.1016/j.ejbt.2017.01.004.19 Nabila A. Huq et al. (2021) Toward net-zero sustainable aviation fuel with wet waste–derived volatile fatty acids. Proceedings of the National Academy of Sciences Mar, 118 (13) e2023008118; DOI: 10.1073/pnas.202300811820 See: https://fulcrum-bioenergy.com/partners/partnersbp/21 Systemiq (2020) Breaking the plastic wave. Available: https:// www.systemiq.earth/wp-content/uploads/2020/07/BreakingThePlasticWave_MainReport.pdf22 Schyns, Z and Shaver, M (2020) Mechanical Recycling of Packaging Plastics: A Review, Macromolecular rapid communications (42(3), September. Available: https://www.researchgate.net/publication/345494289_Mechanical_Recycling_ of_Packaging_Plastics_A_Review23 Ibid24 McKinsey (2020) Plastics recycling: Using an economic-feasibility lens to select the next moves. Available: https://www. mckinsey.com/industries/chemicals/our-insights/plastics-recycling-using-an-economic-feasibility-lens-to-select-the-next-moves25 See https://www.americanchemistry.com/Media/PressReleasesTranscripts/ACC-news-releases/Advanced-Recycling-Already-Providing-a-Sustainable-Path-to-a-Circular-Economy-for-Plastics.html26 See: https://www.greenpeace.org/usa/research/deception-bythe-numbers/Chapter 41 DNV (2020). Energy Transition Outlook, https://eto.dnv.com2 IEA (2020) ‘CCUS in industry and transformation’, in Tracking Industry 2020. Paris: International Energy Agency. Available: https://www.iea.org/reports/tracking-industry-2020/ ccus-in-industry-and-transformation#abstract3 DNV (2021) DNVGL-RP-F104 Design and operation of carbon dioxide pipelines. Available: https://oilgas.standards.dnvgl. com/download/dnvgl-rp-f104-design-and-operation-of-carbon-dioxide-pipelines4 DNV (2019). ‘Safely Re-using Infrastructure for CO2 Transport and Storage’. Available: https://www.dnv.co.uk/Images/ FINAL%20Safely%20re-using%20infrastructure%20for%20 CO2%20transport%20and%20storage_White%20 paper_161019_tcm12-159389.pdf5 DNV (2021). ‘DNV delivers a minimum purity standard for the future use of hydrogen in UK homes and businesses’. Available: https://www.dnv.com/news/dnv-gl-delivers-a-minimum-purity-standard-for-the-future-use-of-hydrogen-in-uk-homes-andbusinesses-171458Energy infrastructure and nano materials1 https://www.ge.com/renewableenergy/wind-energy/ offshore-wind/haliade-x-offshore-turbine2 https://www.maritime-executive.com/article/new-world-slargest-wind-turbine-as-offshore-wind-scale-up-continues3 https://www.nature.com/news/seawater-is-the-secret-to-longlasting-roman-concrete-1.222314 Kunamineni, Vijay; MeenaMurmu, V.Deo Shirish (2017). ‘Bacteria based self healing concrete – A review’ Construction and Building Materials volume 152, October 2017 pp 1008 – 1014. Available: https://www.sciencedirect.com/science/ article/abs/pii/S0950061817313752)67TECHNOLOGY PROGRESS REPORT Energy Transition Outlook 20215 Scardino, Andrew J, de Nys, Rocky (2011). Mini review: Biomimetic models and bioinspired surfaces for fouling control. Biofouling 27(1):73-86, January 2011. Available: https://www. researchgate.net/publication/49659266_Mini_review_Biomimetic_models_and_bioinspired_surfaces_for_fouling_control6 https://www.sharklet.com/7 Ahmed Olanrewaju Ijaolaa; Peter Kayode Farayibib; Eylem Asmatulu (2020). Superhydrophobic coatings for steel pipeline protection in oil and gas industries: A comprehensive review. Journal of Natural Gas Science and Engineering Volume 83, November 2020, 103544. Available: https://www.sciencedirect.com/science/article/abs/pii/S187551002030398X#8 http://www.windengineering.eu/wind_power/nanotechnologies.html9 DNV Technology Outlook 2030 (2020). Available: https://www. dnv.com/to203010 Cho, H. (2013). A simple fabrication method for mechanically robust superhydrophobic surface by hierarchical aluminum hydroxide structures. Current Applied Physics. Volume 13, Issue 4, June 2013, Pages 762-767. Available: https://www. sciencedirect.com/science/article/abs/pii/ S1567173912004683Chapter 51 European Commission (2020). ‘Boosting Offshore Renewable Energy for a Climate Neutral Europe’. Available: https://ec. europa.eu/commission/presscorner/detail/en/IP_20_20962 The White House Briefing room (2021). ‘FACT SHEET: Biden Administration Jumpstarts Offshore Wind Energy Projects to Create Jobs’. Available: https://www.whitehouse.gov/ briefing-room/statements-releases/2021/03/29/ fact-sheet-biden-administration-jumpstarts-offshore-wind-energy-projects-to-create-jobs/Chapter 61 DNV GL (2020). 'Energy Transition Outlook 2020’. Available: https://eto.dnv.com2 https://www.tesla.com/2020shareholdermeeting3 https://www.catl.com/en/research/technology/4 https://www.sciencedirect.com/science/article/pii/ B978008102886500013X5 https://www.popularmechanics.com/science/green-tech/ a36300986/compressed-air-grid-energy-storage-system/6 https://spectrum.ieee.org/energy/batteries-storage/gravity-energy-storage-will-show-its-potential-in-2021Chapter 7 Marine Fuel Cells1 DNV (2012). ‘Fuel cells for ships’, DNV position paper 13, 2012.2 DNV GL (2017). ‘Study on the use of fuel cells in shipping’, for European Maritime Safety Agency (EMSA). Available: www. emsa.europa.eu3 Fraunhofer Institute (2021). ‘The world’s first high-temperature ammonia-powered fuel cell for shipping’. Available: https:// www.fraunhofer.de/en/press/research-news/2021/march2021/worlds-first-hightemperature-ammonia-powered-fuel-cell-for-shipping.html4 DNV GL (2019). ‘Comparison of alternative marine fuels’, for SEALNG, DNV GL rep. no. 2019–05675 Veldhuizen V., N., Hekkenberg, R. G., & Codiglia, L. (2020). ‘Fuel cell systems applied in expedition cruise ships: A comparative impact analysis’. In V. Bertram (Ed.), Proceedings of the 12th Symposium on High-Performance Marine Vehicles, HIPER '20 (pp. 170-188). Technische Universität Hamburg-Harburg. Available: https://research.tudelft.nl/en/publications/fuel cell-systems-applied-in-expedition-cruise-ships-a-comparativ6 Biert L. et al. (2016). ‘A review of fuel cell systems for maritime applications’, Journal of Power Sources 327 (2016) 345e364. Available: www.sciencedirect.com7 Xing, H., et al. (2021). ‘Fuel Cell Power Systems for Maritime Applications: Progress and Perspectives’. Sustainability 2021, 13, 1213. https://doi.org/10.3390/su13031213Nuclear-powered ships1 Soltoff, B. (2020). ‘Advanced nuclear: A climate-tech comeback story’. [Online]. Available: https://www.greenbiz.com/article/ advanced-nuclear-climate-tech-comeback-story2 Chryssakis,C. (2017). ‘Low carbon shipping towards 2050’. DNV GL, Oslo, 20173 International Maritime Organization (2020). ‘Fourth IMO GHG Study 2020 – Final report’, IMO, London, 20204 World nuclear association (2021). ‘Nuclear-Powered Ships’. [Online]. Available: https://www.world-nuclear.org/information-library/non-power-nuclear-applications/transport/ nuclear-powered-ships.aspx. [Accessed 27 04 2021]5 International Atomic Energy Agency (2020). ‘Advances in small modular reactor technology developments’, IAEA, Vienna6 Tiberga, M., et al. (2019). ‘Preliminary investigation on the melting behavior of a freeze-valve for the Molten Salt Fast Reactor’, Annals of Nuclear Energy, vol. 132, pp. 544-554, 20197 Elsheikh, B. M. (2013). ‘Safety assessment of molten salt reactors in comparison with light water reactors’. Journal of Radiation Research and Applied Sciences, vol. 6, no. 2, pp. 63-70, 201368Pipelines for low carbon gases 18 Transatomic Power (2021). ‘The Science – Transatomic'. [Online]. Available: http://www.transatomicpower.com/the-science/. [Accessed 27 04 2021]9 Flibe Enercy, Inc (2021). ‘Technology - Flibe Energy’. [Online]. Available: https://flibe-energy.com/technology/. [Accessed 27 04 2021]10 World Nuclear Association (2021). ‘Safety of nuclear reactors’ . [Online]. Available: https://www.world-nuclear.org/information-library/safety-and-security/safety-of-plants/safety-of-nuclear-power-reactors.aspx. [Accessed 29 04 2021]11 Lyman, E. (2021). ‘“Advanced" Isn't Always Better’. Union of Concerned Scientists, Cambridge, MA, 202112 Sainati, T. et al. (2015). ‘Small Modular Reactors: Licensing constraints and the way forward’. Energy, vol. 82, no. 15, pp. 1092-1095, 201513 Emblemsvåg, J. (2021). ‘How Thorium-based molten salt reactors can provide clean, safe, and cost-effective technology for deep-sea shipping’. Marinte Technology Society Journal, pp. 56-72, 202114 Brinks, H and Hektor, E.A. (2020). ‘Ammonia as a marine fuel’. DNV GL, Oslo, 202015 www.iter.org16 http://www.tokamak.info/17 https://lasers.llnl.gov/18 www.general-fusion.comChapter 81 Carbon Brief (2019). ‘Factcheck: How electric vehicles help to tackle climate change’. Available: https://www.carbonbrief.org/ factcheck-how-electric-vehicles-help-to-tackle-climate-change2 ICCT (2018). ‘Effects of battery manufacturing on electric vehicle life-cycle greenhouse gas emissions’. Available: https://theicct. org/publications/EV-battery-manufacturing-emissions3 CleanTechnica (2021). Avaiable: https://cleantechnica. com/2021/04/06/all-volkswagen-meb-based-electric-carswill-be-v2g-capable-beginning-in-2022/Chapter 91 DNV GL (2020), 'Energy Transition Outlook 2020’. Available: https://eto.dnv.com2 Air Liquide (2020). ‘Inauguration of the world's largest PEM electrolyzer’. Available: https://www.airliquide.com/magazine/ energy-transition/inauguration-worlds-largest-pem-electrolyzer#:~:text=The%20new%20electrolyzer%2C%20 located%20at,currently%20operating%20in%20the%20world3 Enapter EL2.1 datasheet (2021). Available: https://handbook. enapter.com/electrolyser/el21/downloads/Enapter_Datasheet_EL21_EN.pdf [accessed 2021-06-08]4 H. Miller and et al. (2020). ‘Green hydrogen from anion exchange membrane water electrolysis: a review of recent developments in critical materials and operating conditions’. Royal Society of Chemistry, 2020.5 IRENA (2020). ’IRENA (2020), Green Hydrogen Cost Reduction: Scaling up Electrolysers to Meet the 1.5°C Climate Goal.’6 A. Hauch, R. Küngas, P. Blennow, A. Hansen, J. Hansen, B. Mathiesen and M. Mogensen (2021). ‘Recent advances in solid oxide cell technology for electrolysis’.7 A. Van Wijk and J. Chatzimarkakis (2020). ‘Green Hydrogen for a European Green Deal: A2x40 GW Initiative’.Chapter 101 Global CCS Institute (2020). ‘Global Status report 2020’, p19.2 IEA (2021), ‘Net Zero by 2050’, IEA, Paris https://www.iea.org/ reports/net-zero-by-20503 DNV (2020). Energy Transition Outlook 2020. https://eto.dnv. com/20204 https://www.iea.org/commentaries/is-carbon-capture-too-expensive5 IEA (2021), ‘Net Zero by 2050’, IEA, Paris https://www.iea.org/ reports/net-zero-by-20506 IPCC (2018). ‘Global Warming of 1.5°C.An IPCC Special Report on the impacts of global warming of 1.5°C above pre-industrial levels and related global greenhouse gas emission pathways, in the context of strengthening the global response to the threat of climate change, sustainable development, and efforts to eradicate poverty’. Available: https://www.ipcc.ch/sr15/7 Consoli, C. (2019). ‘Bioenergy and Carbon Capture and Storage’. Global CCS Institute.8 https://www.iea.org/reports/ccus-in-industry-and-transformation9 https://www.iea.org/data-and-statistics/charts/current-cost-ofco2-capture-for-carbon-removal-technologies-by-sector10 https://www.carbonbrief.org/swiss-company-hoping-capture1-global-co2-emissions-202511 https://ccsnorway.com/12 https://ccsnorway.com/wp-content/uploads/sites/6/2020/07/ Report-Cost-reduction-curves-for-CCS-Gassnova-version-2b-1.pdf69TECHNOLOGY PROGRESS REPORT Energy Transition Outlook 2021ENERGY TRANSITION OUTLOOK 2021 REPORTS OVERVIEWJUNE Technology Progress Report A review of 10 technologies setting the pace of the energy transition over the next five years.SEPTEMBER Energy Transition Outlook 2021 Our main publication details our model-based forecast of the world’s energy system through to 2050.Financing the transition The challenges and opportunities facing the finance community in supporting an affordable, accelerated and just transition.Maritime forecast An independent outlook examining how the energy transition will affect the maritime industry – with a focus on the decarbonization challenge.OCTOBER Carbon reduction - a backcast to net-zero emissions DNV’s view on a possible net-zero emission energy pathway to 2050.Explore our reports and download our forecast data at eto.dnv.com70THE PROJECT TEAMThis report has been prepared by DNV as a crossdisciplinary exercise between our Group Research and Development unit and our business areas of Energy Systems and Maritime.Steering committee Remi Eriksen, Ditlev Engel, Ulrike Haugen, Trond Hodne, Liv HovemProject director Sverre AlvikProject manager Mats Rinaldo mats.rinaldo@dnv.comCommunications and editor Mark Irvine mark.irvine@dnv.comTechnology chapters – expert contributorsFloating Wind:Magnus EbbesenKimon ArgyriadisDevelopments in solar PV:Dana OlsonWaste to fuel and feedstock:Mark IrvinePipelines for low-carbon gases:Graham BennettEnergy infrastructureand nano materials:Sarah KimptonMeshed HVDC grids:Gunnar HeymannCornelis PletNew battery technology:Jason GoodhandNovel shipping technologies:— Marine fuelcells:Øyvind Endresen— Nuclear fission:Knut Erik Knutsen— Nuclear fusion:Pierre C SamesEVs and grid integration:Jeremy ParkesGreen hydrogen production:Jochum DoumaCarbon Capture and Storage 2.0:Guido MagneschiPipelines for lowThcearpbronjegcat steeasm171About DNVDNV is an independent assurance and risk management provider, operating in more than 100 countries, with the purpose of safeguarding life, property, and the environment. Whether assessing a new ship design, qualifying technology for a floating wind farm, analysing sensor data from a gas pipeline or certifying a food company's supply chain, DNV enables its customers and their stakeholders to manage technological and regulatory complexity with confidence. As a trusted voice for many of the world’s most successful organizations, we use our broad experience and deep expertise to advance safety and sustainable performance, set industry standards, and inspire and invent solutions. dnv.com/etoHeadquarters: DNV AS NO-1322 Høvik, Norway Tel: +47 67 57 99 00 www.dnv.comThe trademarks DNV® and Det Norske Veritas® are the properties of companies in the Det Norske Veritas group. All rights reserved.
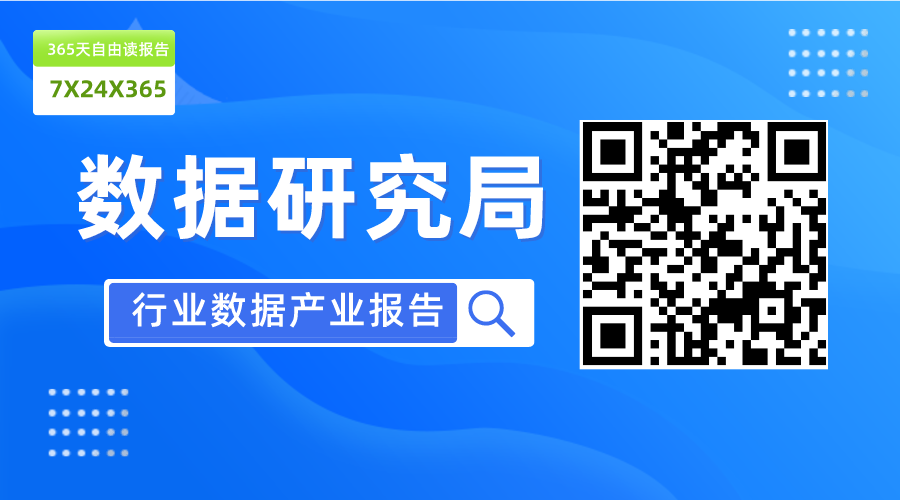
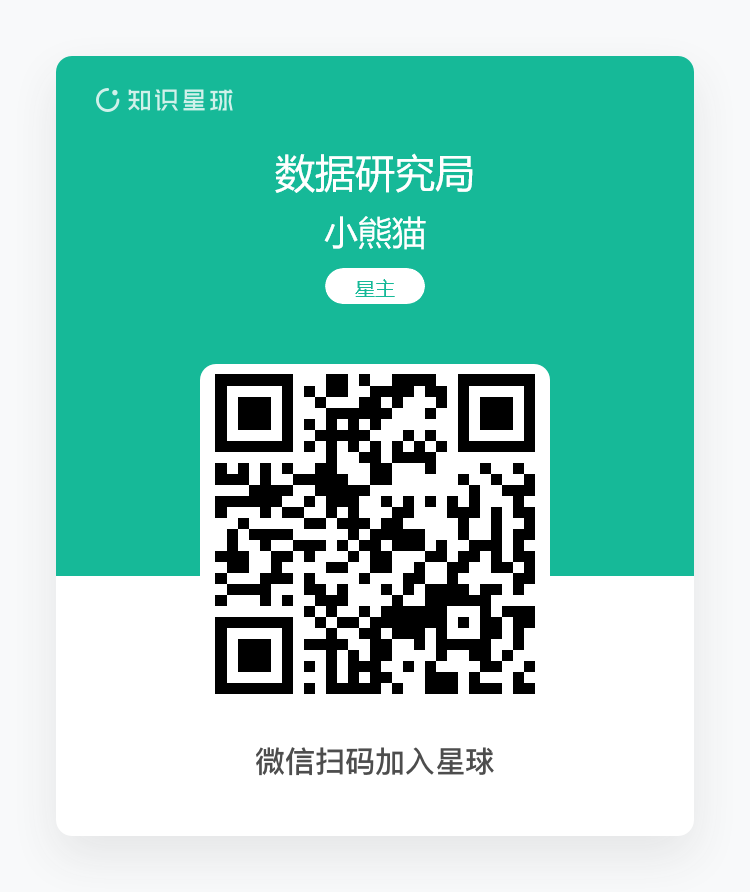