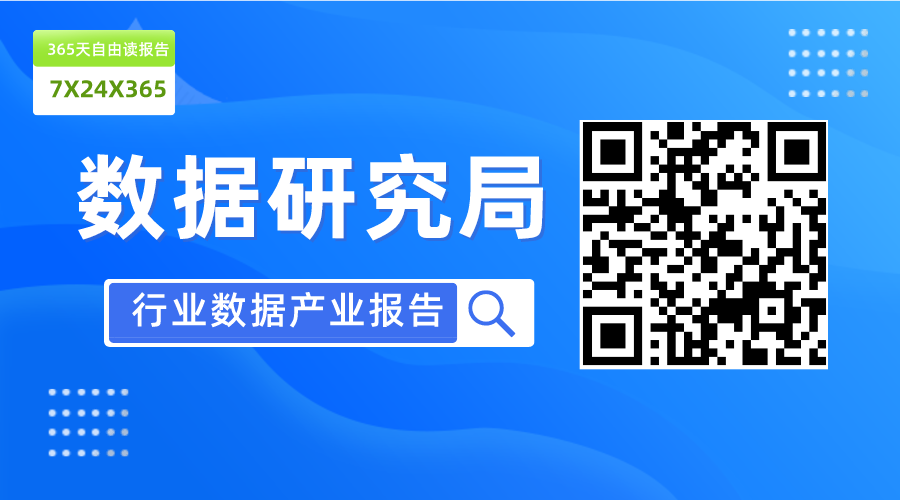
水泥行业碳减排技术指南、平板玻璃行业碳减排技术指南摘要:为深入贯彻落实党中央、国务院关于碳达峰、碳中和的重要决策部署,完整、准确、全面贯彻新发展理念,坚决遏制“两高”项目盲目发展,践行“宜业尚品、造福人类”建材行业发展目标,科学做好水泥行业节能降碳改造升级,推动水泥行业节能降碳和绿色转型,根据《关于严格能效约束推动重点领域节能降碳的若干意见》《高耗能行业重点领域能效标杆水平和基准水平(2021年版)》《高耗能行业重点领域节能降碳改造升级实施指南(2022年版)》,制定本技术指南。 ↓↓↓↓↓水泥行业碳减排技术指南 为深入贯彻落实党中央、国务院关于碳达峰、碳中和的重要决策部署,完整、准确、全面贯彻新发展理念,坚决遏制“两高”项目盲目发展,践行“宜业尚品、造福人类”建材行业发展目标,科学做好水泥行业节能降碳改造升级,推动水泥行业节能降碳和绿色转型,根据《关于严格能效约束推动重点领域节能降碳的若干意见》《高耗能行业重点领域能效标杆水平和基准水平(2021年版)》《高耗能行业重点领域节能降碳改造升级实施指南(2022年版)》,制定本技术指南。 一、总体要求 完整、准确、全面贯彻新发展理念,科学处理发展和减排、短期和中长期的关系,突出标准引领作用,深挖节能降碳技术改造潜力,按照“因业施策”“因企施策”“一线一策”的原则,加快推进水泥行业节能降碳步伐,带动全行业绿色低碳转型,确保如期实现碳达峰目标。 二、遵循原则 因地制宜,综合考虑技改投资与收益,不以提产为主要目标,采用适宜的技术方案,降低单位产品碳排放,以最优的技术经济指标运行。对拟建、在建项目,应对照能效标杆水平建设实施,推动能效水平应提尽提,力争全面达到标杆水平。对能效低于行业基准水平的存量项目,明确改造升级和淘汰时限(一般不超过3年),引导企业有序开展节能降碳技术改造,在规定时限内将能效改造升级到基准水平以上,力争达到能效标杆水平;对于不能按期改造完毕的项目进行淘汰。 三、现状分析 目前,全国水泥熟料生产企业1200多家,水泥熟料生产线近1700条,生产能力约18.4亿吨,其中新型干法水泥熟料生产企业1100多家,水泥熟料生产线约1585条,生产能力约18.2亿吨,日产2500吨水泥熟料生产线约占35%,日产5000吨水泥熟料生产线约占40%。根据《高耗能行业重点领域能效标杆水平和基准水平(2021年版)》,水泥熟料能效标杆水平为100千克标准煤/吨,基准水平为117千克标准煤/吨。按照电热当量计算法,截至2020年底,水泥行业能效优于标杆水平的产能约占 5%,能效低于基准水平的产能约占24%。据此推算,能效低于基准水平的水泥熟料生产能力约有4.5亿吨;按照到2025年,通过实施节能降碳行动,能效达到标杆水平的产能比例超过30%的目标,约有5亿吨的水泥熟料生产能力需要改造提升。水泥行业作为落实碳达峰碳减排的重点行业,节能降碳的压力较大,但通过采用先进的技术和装备,也具有较大的提升改造潜力。受工业和信息化部委托,中国建筑材料联合会选取了4家典型水泥企业,其中日产2500吨水泥熟料生产线1家、日产4000吨水泥熟料生产线1家、日产5000吨水泥熟料生产线2家,作为落实水泥行业碳达峰实施方案的“实验田”,开展“解剖麻雀”式的调查研究,这4家企业涵盖了占比较大的日产2500吨和5000吨水泥熟料生产线,在水泥行业具有一定的代表性、典型性,为本指南提供了主要的基础数据和节能降碳技术路径支撑。 四、主要目标 到2025年,水泥行业能效标杆水平以上的熟料产能比例达到30%,能效基准水平以下熟料产能基本清零,行业节能降碳效果显著,绿色低碳发展能力大幅增强。到2030年,能效基准水平和标杆水平进一步提高,达到标杆水平企业比例大幅提升,行业整体能效水平和碳排放强度达到国际先进水平,为如期实现碳达峰目标提供有力支撑。 表1 水泥行业能效标杆水平和基准水平(2021年版) 五、水泥行业节能降碳技术清单 水泥行业碳排放分为直接排放和间接排放,直接排放包括燃料燃烧排放和生产过程(碳酸盐分解)排放两部分;间接排放包括水泥生产环节中的电力消耗、以及发电、供热和运输等非生产环节的能耗所折合的二氧化碳排放。水泥行业二氧化碳排放主要源于熟料生产过程,其中碳酸盐分解所排放的二氧化碳,约占碳排放总量的60%;燃料燃烧产生的二氧化碳,约占排放总量的35%;电力消耗间接产生的二氧化碳,约占排放总量的5%。 目前水泥行业的燃料结构以煤为主,煤炭占水泥生产所消耗能源的85%左右。对照碳排放产生环节和影响因素,节能降碳技术包括低能耗烧成、高效粉磨、智能化、燃料类及原料类替代等,这些技术目前均较为成熟,分别具有不同的节能降碳潜力,可作为指导水泥企业进行碳减排优化改造实施的行动指南。 表3 水泥行业节能降碳技术清单 六、水泥行业节能降碳技术路径及预期效果 (一)提升能效技术 旨在提高现有水泥工业设备的性能和效率,通过技术优化和局部改进降低系统能耗,达到碳减排的目的,水泥企业可根据实际使用的设备及工艺状况组合使用。 1.生产过程能效提升技术 (1)水泥窑炉用耐火材料整体提升技术 技术路径:预热器及篦冷机内衬采用低导热系数的纳米隔热板代替传统硅酸钙板,回转窑内衬采用低导热系数的复合砖代替传统硅莫砖及高铝砖,或者采用气凝胶隔热材料等新型高效隔热材料,可降低烧成系统热耗。 预期效果:熟料烧成能耗降低1~3kgce/t(注:本文所有能耗指标与GB 16780中使用的能耗指标一致)。 (2)预热器分离效率提升及降阻优化技术 技术路径 :更换原有旋风筒蜗壳部分,增大旋风筒进口面积,合理设计蜗壳结构形式,以达到提高旋风筒分离效率、减小旋风筒内切风速和降低系统阻力的目的;采用预热器控制漏风、结皮技术,优化下料管及撒料盒结构,提升物料在预热器进风管道中的分散效果,增强气固换热效率,可大幅降低预热器出口温度和阻力,降低烧成系统热耗和电耗。 预期效果:熟料烧成综合能耗降低1~2kgce/t。 (3)五级预热器改造低能耗六级预热器技术 技术路径:在土建条件允许的情况下,将传统五级预热器增加一级旋风筒变为六级预热器,预热器塔架新增一层楼面,原有顶级旋风筒上移一层;通过增加一级换热及提高预热器换热效率、分离效率,从而提升预热器整体的换热效率,降低废气排放热量损失,实现水泥烧成节能减碳。 预期效果:熟料烧成综合能耗降低4~5kgce/t。 (4)分解炉自脱硝及扩容优化技术 技术路径:增大原有分解炉炉容,优化进入分解炉的三次风、尾煤及入炉物料下料点位置,创造分解炉自脱硝还原区,改善分解炉内煤粉的燃烧及生料分解,提高煤粉燃尽率和生料的分解率,从而降低烧成系统热耗和提高分解炉自脱硝效率。 预期效果:熟料烧成综合能耗降低1~3kgce/t,减少氨水用量30%~50%。 (5)冷却机升级换代技术(三代更换为四代) 技术路径:将原有三代篦式冷却机整体更换为第四代步进式冷却机,增加篦床面积,同时优化固定斜坡的布置形式、篦板及供风方式,提高冷却机的热回收效率,降低熟料温度,可降低烧成系统热耗。 预期效果:熟料烧成综合能耗降低1~3kgce/t。 (6)冷却机更换为中置辊破技术 技术路径:将原锤式破碎机改造为中置辊破形式,提高熟料冷却效果,增加余热发电能力,可提高篦冷机运转率,降低烧成系统综合能耗。预期效果:熟料烧成综合能耗降低0.2~0.5kgce/t。 (7)富氧燃烧技术 技术路径:由膜法、深冷法、变压吸附等方法获得高浓度的氧气,通入燃烧器一次风及窑头窑尾送煤风中,将一次风及送煤风的氧气浓度提升至28%~36%范围,以加强窑内煅烧温度,提高分解炉难燃燃料或替代燃料的燃尽率,降低系统综合能耗。 预期效果:熟料烧成综合能耗降低2~4kgce/t。 (8)窑头燃烧器优化改造 技术路径:根据燃料特性,进行窑头燃烧器结构优化或整体改造,强化回转窑燃烧器性能,提升窑内煅烧温度,降低一次风用量或改造成可使用生物质、塑料微粒、橡胶微粒等高品位替代燃料的多功能燃烧器,减少化石燃料使用量,降低系统综合能耗。 预期效果:熟料烧成综合能耗降低1~2kgce/t。 (9)生料易烧性和操作管理提升技术 技术路径:通过加入节煤剂、矿化剂等技术,改善燃料的燃烧特性或生料的易烧性,如磷渣、萤石等矿化剂明显降低熟料烧成温度,减少燃料的使用量,提升熟料质量。通过提升操作管理,减少系统漏风,均能降低综合能耗,降低水泥生产成本。 预期效果:熟料烧成综合能耗降低1~5kgce/t。 (10)立式辊磨生料外循环技术 技术路径:采用外循环立式辊磨系统工艺,将立式辊磨的研磨和分选功能分开,物料在外循环立式辊磨中经过研磨后全部排到磨机外,经过提升机使研磨后的物料进入组合式选粉机进行分选,分选后的成品进入旋风收尘器收集,粗颗粒物料回到立式辊磨进行再次研磨,系统气体阻力降低5000Pa,降低了通风能耗和电耗。 预期效果:系统单位电耗11~13kWh/t。 (11)辊压机生料终粉磨技术 技术路径:采用料床粉磨原理,不断优化辊压机设备结构并进行系统工艺创新,辊压机生料终粉磨系统比球磨机生料粉磨系统和立磨生料粉磨系统更节电。预期效果:系统单位电耗10~13kWh/t。 (12)水泥粉磨优化提升技术 技术路径:基于增加料床粉磨做功比重的理论方法,低能耗水泥粉磨成套技术装备进行了系统创新,有多种不同的选项如纯球磨改联合(辊压机、立式辊磨联合粉磨系统),小辊压机改大辊压机,增加高效三分离选粉或高效选粉机,可降低水泥粉磨系统电耗。 预期效果:系统单位水泥电耗23~26kWh/t。 表4 低能耗水泥粉磨成套技术装备 (13)钢渣/矿渣辊压机终粉磨技术 技术路径:以辊压机和动静组合式选粉机为核心设备,全部物料为外循环,除铁方便,避免块状金属富集,辊面寿命可达立磨的2倍,具有广泛的物料适应性,可以单独粉磨矿渣、钢渣,也可用于成品比表面积<700m²/kg的类似物料的粉磨,系统阻力低,节电效果明显。 预期效果:生产矿渣微粉时系统电耗小于33kWh/t。 (14)钢渣立式辊磨终粉磨技术 技术路径:采用料层粉磨、高效选粉技术,集破碎、粉磨、烘干、选粉为一体,集成了粉磨单元与选粉单元;通过磨内除铁排铁、外循环除铁、高压力少磨辊研磨等技术,使得钢渣中的金属铁有效去除。 预期效果:系统能耗≤40kWh/t。 (15)风机效率提升节能技术 技术路径:目前,随着风机/电机整体节能技术的进步,水泥工业使用高效风机、新型悬浮风机、永磁电机(低负荷运行时)、高效联轴器等节能通用设备能够起到很好的节电效果。近年来节能风机技术开始广泛应用,能够实现节能30%~40%,噪声由120dB降到80dB。 预期效果:风机效率达到82%~85%,实现节能30%~40%。 2.数字化、智能化技术 技术路径:围绕构建智能装备、智能生产、智能运维、智能运营、智能决策等五大维度,打造“数据、算力、算法、场景和全链路”的技术集群,实现水泥生产线层级的生产管控智能决策、自动化专家系统、智能优化控制及自主寻优,整体完成或分步完成四个维度的生产管控智能化平台建设。 (1)智能装备:实现原料自动配料、烧成系统智能优化控制、出磨生料智能控制,全自动化验室采样/送样/成分化验等过程全自动完成,石灰石、原煤辅料堆场无人值守,自动调车和自动堆取料、实现堆场数字化管理。 (2)智能生产:从石灰石破碎、原料磨、煤磨、脱硫脱硝、熟料发散、辅料原煤堆场均实现无人值守、一键启停、自动控制,各种异常工况均能全自动联锁保护,初步实现烧成系统自寻优控制,完成质量全自动闭环控制,实现智能自动配料,风、煤、料、窑速匹配,生料及窑况稳定性明显增强。 (3)智能运维:由视频巡检与主辅机振动在线监测、视频监控系统、油品在线监测系统、现场专业巡检融合构建一体化高效智能巡检体系;全自动智能润滑系统;设备巡检、检修、隐患处理通过自动工单流转方式实行闭环管控。 (4)智能运营:能耗分析过渡为自动取数、自动统计汇总、自动分析、自动能耗异常根源分析,改变数据分析模式,有效提升能耗分析效率、精准性。实现质量一体化管控,打通质量数据、质量管控和智能优化控制链路;安全管理由人工跟踪监管变为信息化多维度防控,中高危区域分级防控,在线验证防护措施及监管到位,实施电力运行安全监控系统。 (5)智能决策:逐步落地在线热工诊断、生料质量闭环控制、能耗分析及异常定位、在线物料平衡等算法;生产智能控制平台借助“APC+大数据+AI算法”,实现窑况异常工况识别、全局自主寻优、游离氧化钙和28天熟料强度预测;在窑头喂煤控制、篦冷机风量控制及与余热发电经济平衡控制方面,应用专家AI算法优势,进一步兼顾余热发电量、降低吨熟料煤耗。 预期效果:实现生产线定员定岗小于80人,熟料综合电耗降低1~5 kWh/t,标准煤耗降低1.0~3.0kgce/t。 (二)原燃料替代技术 水泥工业CO?排放的60%左右来自于碳酸盐分解,35%左右来自于燃料燃烧,5%左右来自发电的间接排放。用垃圾衍生燃料(RDF)、生物质燃料、塑料、橡胶、皮革、废弃轮胎等替代燃料来替代化石能源,可减少燃料产生的碳排放。另一方面用钙质工业固废来替代石灰石,可显著减少碳酸盐分解的碳排放。该技术方向旨在从原、燃料替代出发,通过采用不同的原料或燃料,从工艺角度减少水泥系统的碳排放量,需要水泥企业根据环境条件、自身情况,在国家鼓励政策下选择使用。 1.替代燃料协同处置技术 技术路径:替代燃料可分为固体、液体和气体替代燃料,其中固体替代燃料主要包括垃圾衍生燃料(RDF)、生物质燃料、塑料、橡胶、皮革、废弃轮胎等;液体替代燃料主要包括矿物油和液压油等;气体替代燃料主要包括焦炉气、炼油气、裂解气和氢能源等。积极开展氢能和生物质燃料煅烧水泥熟料关键技术及示范应用研究。目前,RDF、废油、废轮胎及污泥等用作替代燃料较为普遍。将废弃物进行破碎、筛分、风选等预处理,直接喂入水泥烧成系统的不同位置。通过预处理工艺降低废弃物的细度、水分等,提升其燃料特性,可作为燃料替代使用,从而减少化石燃料的使用量。对于替代燃料比例高且Cl?含量等有害成分比较高时,可设置旁路放风系统。 预期效果:燃料替代率20%~60%,CO?排放量降低约10%~20%,水泥熟料生产综合能耗降低10%~50%。 2.替代燃料预煅烧装备及技术 技术路径:采用预煅烧设备直接处理适宜于改造现场的生活垃圾、生物质、固体废弃物等,替代燃料预煅烧设备可实现原生废弃物的干燥、气化及焚烧过程,实现废弃物的预处理及预燃烧,可大幅提升水泥烧成工艺的替代燃料使用量及替代率。 效益说明:燃料替代率达到50%以上,CO?排放量降低约10%~20%,水泥熟料生产综合能耗降低10%~40%。 3.新能源替代技术 技术路径:利用水泥厂的自然环境和地理位置,使用风电、光电技术、风光储技术,吸收工业领域新能源技术探索经验,通过绿色能源技术途径减少水泥生产过程中的电力消耗,结合余热发电,改造现有水泥厂使其实现“零购电”或“近零购电”,促进水泥生产的绿色能源低碳转型。 预期效果:增加一套1.5MW风力发电项目,则年发电量约150万kWh,电力消耗减少1kWh/t;建设多套风力发电或者光电、垃圾发电,可实现水泥企业“零购电”。 4.电石渣替代石灰石质原料生产水泥熟料技术 技术路径:采用电石渣全部替代石灰石原料、采用新型干法水泥生产技术生产水泥熟料,解决电石渣废渣污染环境的问题;电石渣替代石灰石质原料,变废为宝,节省石灰石矿山资源;实现水泥工业绿色、低碳发展。 预期效果:1吨电石渣(干基)可以代替1.23吨优质石灰石生产1吨熟料,CO?排放量降低约40%~50%。 5.超细冶金渣立式磨粉磨装备技术 技术路径:采用立式磨粉磨工艺对大量矿渣、钢渣等固体废弃物进行资源化处置,提升其利用领域和经济价值。为地方消化大量矿渣、钢渣等固体废弃物,促进水泥生产熟料减量化技术发展,降低碳排放总量。 预期效果:吨水泥熟料系数降低≥5%,CO?排放量降低约6%~8%。 (三)低碳水泥技术 低碳水泥旨在降低生产水泥熟料所用碳酸盐,或减少熟料用量。 1.高贝利特硫铝酸硅酸盐(铁铝酸硅酸盐)水泥技术 技术路径:水泥熟料特殊配料烧成技术,通过改变原水泥烧成配料和工艺工况控制,可将常规水泥生产线改为高贝利特水泥生产线,该高贝利特水泥抗压强度等参数与常规水泥相当或更优。 预期效果:降低水泥熟料烧成工艺过程CO?排放量20%~30%。 2.低热硅酸盐水泥与中热硅酸盐水泥及其制备技术 技术路径:降低硅酸盐熟料中C3S含量,提高C2S含量,并采用C2S活化和稳定技术提高水泥强度。采用该技术,石灰石用量比普通水泥降低约10%左右,并可使用较低CaO含量的石灰石进行配料。该水泥是具有低水化热、较高后期强度、耐蚀性好等特点,适用于水工大坝等超大体积混凝土工程。 预期效果:降低水泥熟料烧成工艺过程CO?排放量5%左右。 3.分级分别水泥粉磨技术 技术路径:围绕水泥中熟料水化有效利用率低、碳排放强度高的问题,重构水泥颗粒组成,开展新型水泥低碳粉磨技术研究,实现料床粉磨能耗持续降低。预期效果:开展分级分别高效粉磨制备低碳水泥技术研究,达到相同的硅酸盐水泥强度,实现熟料系数降低10%以上。 4.高岭土煅烧生产低碳水泥 技术路径:LC³低碳水泥是一种基于煅烧活性高岭土和石灰石耦合替代水泥中部分熟料的石灰石煅烧粘土水泥,其技术关键是高岭土的煅烧活化,采用悬浮煅烧技术、回转煅烧技术或类似低温改性工艺进行高岭石粘土脱水得到活性高岭土,在保证水泥性能的同时降低熟料掺量。 预期效果:低碳水泥中熟料掺量可降低至50%,与传统硅酸盐水泥相比,CO?排放量降低约30%以上。 5.工业副产石膏制硫酸联产水泥成套技术 技术路径:采用工业副产石膏立式烘干脱水装置、预热器、回转窑、冷却机等水泥技术装备,形成工业副产石膏制硫酸联产水泥新工艺,大幅降低烧成系统热耗,显著提高制酸烟气的SO?浓度,实现工业副产石膏资源化利用的节能减排并降低生产成本。 预期效果:采用工业副产石膏替代天然石灰石,CO?排放量降低约50%。 (四)碳捕集封存技术 碳捕集封存技术直接将水泥生产过程中产生的CO?进行捕集提纯,用于其他工业领域或食品加工、化学利用或者直接封存等,直接减少了水泥企业的CO?排放。 1.全氧燃烧耦合低能耗碳捕集技术 技术路径:采用制氧设备制造的高浓度纯氧气体与烧成系统产生的循环烟气混合再送入烧成系统中作为燃烧助燃气体使用,由此可大幅提升烧成系统排出气体中的CO?浓度,干基CO?浓度可达80%以上,大幅降低CO?进一步捕集提纯的成本。 预期效果:单位CO?能源消耗小于1.6GJ/t.CO?。 2.水泥窑炉烟气捕集CO?技术 技术路径:利用化学、物理方法直接捕集水泥窑炉烟气中二氧化碳,并采用吸收法进行高浓度纯化,达到CO2捕集提纯的目的。 预期效果:单位CO?能源消耗小于2.3GJ/t.CO?。 七、不同能耗水平水泥企业技术改造提升建议 本指南仅以试点企业提出碳减排技术方案,不同原燃料条件的水泥企业根据其实际使用的工艺、设备进行个性化的选择,以达到最大化的节能降碳为目标。各水泥企业在实际实施中宜查漏补缺,补短板增强项,最终实现综合能耗及碳排放的降低。 本指南以GB 16780—2021《水泥单位产品能源消耗限额》中定义的1级、2级、3级能耗标准为碳减排技术应用目标,为不同能耗等级的水泥企业提供对应的碳减排技术应用方案。指南中所列举的碳减排技术方案仅为建议方案,水泥企业在实际应用中可根据具体情况选择使用。 (一)能耗3级以下企业节能降碳技术改造建议能耗3级以下企业往往采用较落后的设备或工艺,通过设备升级或工艺优化可以降低水泥生产综合能耗,使其达到综合能耗3级或2级水平。 以综合能耗120kgce/t的水泥生产企业为例,使其达到综合能耗3级或2级水平可以采用以下技术(见表5)。 表5 综合能耗达到3级或2级水平可采取的技术措施 为达到3级能耗,需要将水泥生产的设备及工艺提升至目前主流的高效低阻预热器、大炉容分解炉、第四代篦冷机、生料辊压机终粉磨等某些技术组合,可降低综合能耗7~10kgce/t。在达到3级能耗的基础上进一步选择耐火材料整体提升、五级预热器改六级、冷却机中置辊破、富氧燃烧等某些技术组合,进一步降低热耗,整体可降低综合能耗6~8kgce/t,最终达到综合能耗2级水平。 (二)能耗2级以下企业节能降碳技术改造建议 能耗达到3级但未达到2级的水泥企业大都采用了部分先进的设备或工艺,但局部需要进行优化提升。 以综合能耗112kgce/t的水泥生产企业为例,使其达到综合能耗2级或1级水平可以采用以下技术(见表6)。 表6 综合能耗达到2级或1级水平采取的技术措施 达到2级能耗的技术方案,可在表6中依据实际需要选择几项组合使用,可降低综合能耗5~8kgce/t。采用五级改六级、富氧燃烧技术可在常规技改优化的基础上进一步降低4~8kgce/t,如采用替代燃料、生料易烧性提升、电石渣替代、新能源等技术可大幅降低综合能耗,直接达到1级能耗。 (三)能耗1级以下企业节能降碳技术改造建议 能耗达到2级但未达到1级的水泥企业基本已经采用了先进的设备或工艺,如需进一步提升能耗水平需要采用替代燃料、生料易烧性提升、电石渣替代、新能源等技术。 采用替代燃料、电石渣替代、新能源替代、高贝利特低钙水泥中的一项或多项可大幅降低能耗水平及CO?的排放量,使不同能耗水平的水泥企业直接达到1级能耗水平。 八、未来水泥企业碳减排技术展望 (一)水泥熟料新型循环悬浮煅烧技术。新型循环悬浮煅烧技术将回转窑内堆积态变为流态化,因而系统内部气固两相充分接触,换热效率提升,与现有同规模新型干法水泥熟料烧成工艺相比,热耗降低10%以上,电耗降低5%以上。 (二)清洁电能煅烧水泥的研究。在国家政策的推动下,未来全国范围内逐步走向控制高碳能源消费,以低碳电力替代高碳电力,推进非化石能源。在这种情况下,水泥工业可能会向绿色电力的电气化发展。如果考虑未来水泥生产线全部采用清洁电能的绿电,实现水泥厂电气化煅烧水泥,可以起到大幅度减排效果。 (三)绿色生态智慧矿山。绿色生态智慧矿山采用的技术途径包括:矿区生态环境和谐,矿区可绿色化区域绿化覆盖率和生态修复率达到100%;矿山固体废物零排放,资源利用率100%;矿山生产设备智能化,生产现场无人化;矿山安全生产和智能配矿。最终建成生态环境和谐友好的公园式矿区,提高矿区生态系统碳汇能力,实现“零碳”矿山。 (四)提升水泥产品利用效率。水泥产品利用效率的提升,可有效减少水泥产品的使用。目前应在保证混凝土性能的基础上,尽可能减少水泥用量,可以通过提高建筑及基础设施中混凝土的有效使用率,在建筑领域采用木材及其他建筑材料替代水泥,回收水泥、回收混凝土并经处理后再利用、开发使用水泥用量较低的新的混凝土产品等方式降低水泥需求量。因此需要对相关的技术规范、施工规范、设计规范做进一步修订,提高水泥产品使用效率。另外,在工程管理上也需要在水泥利用效率上加强控制,通过更优、更细的管理促使水泥用量下降,给予水泥碳中和直接支持。 (五)实现熟料替代,调整水泥产品原材料结构。寻找一些活性材料替代或减少熟料使用也是节煤减碳的一种方式。在工程建设过程中,根据混凝土性能需要,有差别的使用水泥,也是碳减排的重要途径。例如,在砌筑,抹墙等非承重结构上推广使用砌筑水泥。 (六)碳捕集技术由于碳封存或碳利用技术局限,目前尚不能直接大幅度降低碳排放水平,但由于该技术可直接降低最终的CO?排放,达到最大的CO?减排效果,在相应标准支持下可得到更多水泥企业的青睐。-附 言 本指南参加单位及人员: 中国建筑材料联合会:陈国庆、孙星寿、曹会保、宋有崑、刘杨、张娅妮、张凯博、冯帅、周鸿锦、秦松、石红卫、罗宁、刘新琪、王勇。 中国中材国际工程股份有限公司:李荧琳、林莉。 中材国际研究总院:彭学平、聂文海、赵亮、马娇媚、李波。 天津水泥工业设计研究院有限公司:刘涛、俞为民、许芬、郭玉兴、张良宏、姬广彬、李宁、王娜、徐自强、李红雨、张松、洪卓、张江涛、李华军、张建国、贺朋、石国平、董蕊、胡敬民、郭建设。 中国中材国际工程股份有限公司(南京):张健、高星、陈建坤、殷昭波、吴瑶瑶、宁建根、黄锋、吕满根、姬洪宇、庸登明、熊建华、景国泉、樊猛猛。 合肥水泥研究设计院有限公司:王虔虔、郑青、张自力、褚彪、崔洪坤、刘春杨、蔡业堃、华俊、田艺、王浩、刘银杰、张宏图、徐从战、朱飞、李辉、丁浩、陈高升、文友强、刘运华。 成都建筑材料工业设计研究院有限公司:陈涛、刘建、高敏、蔡顺华、董贝、张象刚、程宏伟、朱战岭、李鹏斌、王国鸿、汤跃、黄伟、杨腾飞、马旭。 中材建设有限公司:张超、曾计生、姚秀丽。 中国中材海外科技发展有限公司:高超、于洋、梁丽鹏。 南京凯盛国际工程有限公司:钟根、钟永超、罗超。 北京凯盛建材工程有限公司:魏文荣、彭延松。 中材国际环境工程(北京)有限公司:胡斌、郭彦鹏。 中国建筑材料工业规划研究院:白云峰。 中国国检测试控股集团股份有限公司:鹿晓泉、易帅。 中国信息通信研究院:胡景楠。 中化地质矿山总局化工地质调查总院:屈云燕。 北京国建联信认证中心有限公司:武庆涛、尹靖宇、张晋、杨中周、钱建荣、王瑞蕴、方群。 唐山冀东水泥股份有限公司:魏卫东、林云、姜雨生、龚建贵。 冀东水泥滦州有限责任公司:王俊星、易明波、曹庆杰。 重庆华新地维水泥有限公司:杨宏兵、盛建华、汪宣乾、袁兵、王洪宝、章鹏。 冀东海德堡(泾阳)水泥有限公司:张永林、柳拉、王政军、王辉。 本指南在编写过程中得到了阎晓峰、李叶青、彭寿、隋明洁、包玮、隋同波、蔡玉良、刘成雄、刘起英、张冲、刘世民等专家及其他相关单位的指导和帮助!工业和信息化部原材料工业司等有关部门全程参与并予以指导!-平板玻璃行业碳减排技术指南 为深入贯彻落实党中央、国务院关于碳达峰、碳中和的重要决策部署,完整、准确、全面贯彻新发展理念,坚决遏制“两高”项目盲目发展,践行“宜业尚品、造福人类”建材行业发展目标,科学做好平板玻璃行业节能降碳改造升级,推动平板玻璃行业节能降碳和绿色转型,根据《关于严格能效约束推动重点领域节能降碳的若干意见》《高耗能行业重点领域能效标杆水平和基准水平(2021年版)》《高耗能行业重点领域节能降碳改造升级实施指南(2022年版)》,制定本技术指南。 一、总体要求 完整、准确、全面贯彻新发展理念,科学处理发展和减排、短期和中长期的关系,突出标准引领作用,深挖节能降碳技术改造潜力,按照“因业施策”“因企施策”“一线一策”的原则,加快推进平板玻璃行业节能降碳步伐,带动全行业绿色低碳转型,确保如期实现碳达峰目标。 二、遵循原则 对拟建、在建项目,应对照能效标杆水平建设实施,推动能效水平应提尽提,力争全面达到标杆水平。对能效低于行业基准水平的存量项目,明确改造升级和淘汰时限(一般不超过3年),引导企业有序开展节能降碳技术改造,在规定时限内将能效改造升级到基准水平以上,力争达到能效标杆水平;对于不能按期改造完毕的项目进行淘汰。 三、现状分析 目前,全国平板玻璃生产企业200多家,玻璃熔窑约350座,生产线约450条,生产能力12亿重量箱。根据《高耗能行业重点领域能效标杆水平和基准水平(2021年版)》,平板玻璃(生产能力>800t/d)能效标杆水平为8千克标准煤/重量箱,基准水平为12千克标准煤/重量箱,平板玻璃(500≤生产能力≤800t/d)能效标杆水平为9.5千克标准煤/重量箱,基准水平为13.5千克标准煤/重量箱,截至 2020年底,平板玻璃行业能效优于标杆水平的产能占比小于 5%,能效低于基准水平的产能约占 8%。据此推算,能效低于基准水平的平板玻璃生产能力约有1亿重量箱;按照到2025年,通过实施节能降碳行动,能效达到标杆水平的产能比例超过20%的目标,约有2亿重量箱的平板玻璃生产能力需要改造提升。平板玻璃生产过程中需要消耗燃料油、煤炭、天然气等能源,不同平板玻璃企业生产能耗水平和碳排放水平差异较大,但通过采用先进的技术和装备,也具有较大的节能降碳改造升级潜力。受工业和信息化部委托,中国建筑材料联合会选取了3家典型平板玻璃企业,其中日熔化能力600吨生产线企业2家、日熔化能力900吨生产线企业1家,作为落实平板玻璃行业碳达峰实施方案的“实验田”,开展“解剖麻雀”式的调查研究,这3家企业既有日熔化能力大于500吨的生产线企业,也有日熔化能力大于800吨的生产线企业,技改完成后,既有生产普通玻璃的生产线,又有生产在线镀膜、超白高档玻璃生产线,在行业中具有一定的代表性、典型性,为本指南提供了主要的基础数据和节能降碳技术路径支撑。 四、主要目标 到2025年,玻璃行业能效标杆水平以上产能比例达到20%,能效基准水平以下产能基本清零,行业节能降碳效果显著,绿色低碳发展能力大幅增强。 表1 平板玻璃领域能效标杆水平和基准水平(2021年版) 五、平板玻璃行业节能降碳技术路径及预期效果 (一)熔窑 玻璃熔窑能耗占玻璃工厂总能耗的95%左右,熔窑的能量消耗主要有玻璃液生成热,熔窑表面散热、烟气带走热量三部分。随着窑炉结构优化、规模提高,优质玻璃生产线玻璃生成热目前占比40%~52%,烟气带走热量低于25%。要降低熔窑能耗,需要在四个方面进行优化。 1.整体提高传热效率 技术路径:(1)采用先进技术手段对窑炉整体结构、材料进行优化,综合技术措施效率最大化。(2)采用0#氧枪、富氧或全氧燃烧技术。通过富氧代替部分或全部空气助燃风,提高火焰燃烧温度,增加火焰辐射效率,加强配合料的预熔、减少烟气生成量,减少烟气带走热量。(3)采用电助熔技术,利用高效率的电能代替部分火焰加热,同时可减少烟气生成量,减少烟气带走热量。(4)采用多级池底台阶结构,配合卡脖水包控制进入成型和回流的玻璃液量,减少玻璃重复加热。(5)采用单排或多排鼓泡,加强玻璃液的强制对流,提高玻璃液吸热效率。 2.加强配合料系统研究,减少玻璃液生成热 技术路径:(1)控制原料颗粒度及化学成分。原料颗粒大时会导致熔化困难,而过细的颗粒容易造成配合料飞扬、结块,导致配合料混合不均匀,原料化学成分稳定及严格控制杂质含量有利于配合料熔化。(2)采用配合料块化、粒化和预热技术,调整配合料配方,控制配合料的气体率,调整玻璃体氧化物组成,开发低熔化温度的料方,减少玻璃原料中碳酸盐组成,降低熔化温度,减少燃料的用量,降低二氧化碳排放。(3)配方优化。在不影响玻璃性能的前提下,减少燃料用量。(4)适度增加熟料比例。每增加1%碎玻璃,可减少熔窑的能耗约5kcal/kg玻璃液。 3.减少玻璃窑炉表面散热量 技术路径:(1)加强全窑保温及密封。采用新型梯度保温材料对熔化部大碹、胸墙、山墙、小炉、蓄热室进行保温。加强烟道保温和密封,减少散热和漏风。增加熔化部池底保温厚度、优化设计池壁保温,减少池壁暴露面。(2)加强冷却部保温。改变传统冷却部不保温的方式,通过调整卡脖水包尺寸,增加冷却部池壁、胸墙、大碹等部位的保温,减少冷却部表面散热。(3)通过在熔化部大碹及胸墙等部位内表面喷涂高温红外辐射涂料的方式,增加窑内辐射效率,减少碹顶散热。(4)投料口采用挡焰砖代替传统的水包,减少用水量及水带走的热量。(5)投料口设置密封罩,对投料口进行全密封设计,减少投料口处散热。 4.提高余热回收效率 技术路径:(1)通过提高格子体高度,减少格孔孔径,优化蓄热室分隔方式等途径增加格子体换热面积,提高助燃空气温度,降低出蓄热室烟气温度。(2)增加生产线余热资源的计量设施,蒸汽量单独计量。(3)鼓励蒸汽优先直接用于生产线设施,直接用于厂区生活、办公区采暖或制冷。(4)加强烟道保温、防水、防漏措施。 表3 熔窑节能技术改造预期效果 (二)工艺 优化熔窑、锡槽,退火窑及公用工程的工艺控制,提高全厂工艺用能效率。 技术路径:(1)熔窑燃烧系统采用精确控制、小炉燃料量智能化分配、助燃风-燃料量交叉限幅优化控制,实现自动比例调节。设置在线氧量仪,优化燃料消耗,降低能耗。(2)采用先进的喷枪系统,提高火焰燃烧效率。(3)窑炉控制系统能保持窑炉温度、压力、液面、泡界线等稳定在最优工况。(4)风机、水泵类负载采用变频控制,并采取节能自动控制措施。(5)增加燃料热值分析装置,监控燃料的品质稳定,提高熔窑燃烧控制的准确性。(6)增加在线测氢装置,监测锡槽内部微量氧,精确控制保护气比例。(7)退火窑冷却风余热利用,可引至熔窑助燃风提高燃烧效率或用于生产蒸汽及厂区内采暖。(8)利用余热蒸汽直接拖动氮站的原料空气压缩机或代替其它电动机,提高整体效率及减少用电量。 预期效果:通过优化全厂工艺控制,预期可节能约3%,减少CO?排放0.6kg/重量箱玻璃。 (三)电气自动化 技术路径:(1)淘汰高耗能机电设备,空压机、风机、水泵选型符合有关节能规定。电动机、变压器等电气设备采用高能效产品。接触器、继电器、电磁阀等元器件采用低功耗产品。(2)提高熔窑自动化水平,窑温、窑压、液面等重要工艺参数自动控制,全面监测窑内玻璃液和耐材温度,对燃烧状况大数据分析,进行优化控制。(3)优化熔窑换向过程,协调控制助燃风吹扫、烟道调节闸板动作,缩短换向时间,换向过程工艺参数最小扰动。(4)提高锡槽自动化水平,锡槽玻璃板宽监控数字化,锡槽自动化改板缩短改板时间。(5)退火窑控制系统应能提供准确、稳定和易于调节的退火温度曲线控制手段。在保证产品质量的前提下,宜采用加热量少的退火温度作业制度和节能控制措施。(6)冷端采用优化系统,可多订单优化切割。(7)车间照明采用高效LED灯,厂区可采用太阳能蓄电池路灯;照明宜分区分组控制;照明功率密度应符合相关规范规定。(8)采取措施减少无功损耗,功率因数不低于0.95。宜采用高压补偿与低压补偿相结合,集中补偿与就地补偿相结合的无功补偿方式。宜采用滤波方式抑制高次谐波,谐波限制符合电力部门有关规定。(9)能源计量满足全厂和各子系统单独计量考核要求。 预期效果:可减少单位产品用电量约1kWh/重量箱玻璃,减少CO?排放0.58kg/重量箱玻璃。 (四)新能源替代技术技术路径:利用平板玻璃企业的自然环境和地理位置,使用风电、光电技术、风光储技术,吸收工业领域新能源技术探索经验,通过绿色能源技术途径减少平板玻璃生产过程中的电力消耗,结合余热发电,分布式发电等,提升企业能源“自给”能力,减少对化石能源及外部电力依赖,促进平板玻璃生产的绿色能源低碳转型。(五)智能化工厂 智能玻璃工厂是充分利用互联网、云计算、大数据、物联网等技术和设备监控技术现实工厂信息管理和服务,实时掌握产销流程、提高生产过程可控性、消除信息孤岛,实时精准采集生产线各项数据,实现玻璃工厂降本增效,节能减排,为企业提供生产计划管理、生产调度管理、库存管理、质量管理等管理平台,实现资金流、物流、信息流的统一管理。推广自动化配料、熔窑、锡槽、退火窑三大热工智能化控制,熔化成形数字仿真,冷端优化控制、在线缺陷检测、自动堆垛铺纸、自动切割分片、智能仓储等数字化、智能化技术,推动玻璃生产全流程智能化升级。 1.生产管理与智能优化 技术路径:融入指标、绩效、成本管理等先进管理理念,通过生产日志、台账、报表等方式将人、机、料、法、环有效融合,通过DCS、PLC生产线数据采集,将生产管理全过程的数据进行汇总、分析,实时反馈生产订单的产量、完成率、班组绩效。有效提升玻璃生产数字化、智能化水平,提高企业整体管控水平。对生产数据进行大数据分析,对生产过程进行智能优化控制。在中央控制室对各子车间生产进行智能化集中监控和统一管理,在原料、水泵房、空压站、油站等分车间实行就地无人化操控。 2.设备管理 技术路径:以统一的资产编码为纽带,建立完善的设备台账;精确的设备分级分层管理、备品备件管理,建立标准化设备故障停机考核体系,提升设备综合效率,降低对产能及品质影响。 3.安环管理 技术路径:安全管理模块提供隐患排查与治理体系,推动安全隐患治理,降低企业安全事故发生率。环保管理模块可实现对排放数据、环保控制设施运行数据的耦合关系建模和参数调控,降低企业环保管理成本。 4.能源管理 技术路径:采用能效管理系统是对燃料、电、水、蒸汽、压缩空气、氮氢气等能源的实时能耗数据采集、监视,通过大数据分析,找出企业管理、设备、工艺操作中的能源浪费问题;核算企业节能效果,明确企业节能方向,降低单位能耗成本,提高企业综合竞争力。 六、不同能耗水平玻璃企业技术改造提升建议 本指南仅以试点企业提出碳减排技术方案,不同原燃料条件的平板玻璃企业根据其实际使用的工艺、设备进行个性化的选择,以达到最大化的节能降碳为目标。各平板玻璃企业在实际实施中宜查漏补缺,补短板增强项,最终实现综合能耗及碳排放的降低。 本指南以GB 21340—2019《平板玻璃单位产品能耗限额等级》中定义的1级、2级、3级能耗标准为碳减排技术应用目标。指南中所列举的节能降碳技术方案为建议方案,平板玻璃企业在实际应用中可根据具体情况选择使用。 以综合能耗低于标杆值,但优于2级能耗,使其达到标杆值水平,可采用如下技术措施。 (一)熔窑技改建议 1.对熔化部大碹、胸墙、后山墙及小炉、蓄热室采用低导热率的新型梯度保温措施,通过保温材料的导热系数计算不同保温厚度方向的界面温度,并选用相匹配的保温材料,提高保温材料寿命,降低保温材料衰减速度。对烟道采用保温棉加外包钢板形式减少烟道散热和漏风。增加熔化部池底保温厚度,优化池壁保温,减少池壁暴露面。 2.采用多级台阶池底结构,并配合适当的卡脖水包压入深度后,对冷却部池壁、胸墙、前后山墙及大碹进行保温,减少冷却部表面散热。 3.通过在熔化部大碹及胸墙等部位内表面喷涂高温红外辐射涂料的方式,增加窑内辐射效率,减少碹顶散热。 4.热点附近设置单排或多排鼓泡,进一步加强玻璃液的对流吸热效率。 5.优化蓄热室分隔方式,减少格子体孔径,增加格子体体积,提高蓄热室换热效率。 6.投料口采用挡焰砖+密封罩形式,加强投料口密封。 7.适当增加碎玻璃比例,可减少玻璃液生成热,降低熔化温度,每增加5%碎玻璃比例,可节能约1%。 8.采用富氧代替部分空气助燃风,提高火焰燃烧效率。富氧代替比例10%~20%,可节能约2%~5%。 9.设置池底电助熔系统,对于600吨/天熔窑,若安装电助熔功率3000kW,使用绿电可代替约20%燃料,节能约5%。 (二)工艺技改建议 1.设置在线氧量仪,优化燃料消耗,降低能耗。 2.风机、水泵类负载采用高效节能变频电机,并采取节能自动控制措施。 3.池壁冷却风风嘴设导风板,避免冷风吹入窑内。 4.各种物料输送均采用高效、节能、低耗的工艺设备,以便最大限度地节省电耗。 5.投料机采用料垄分隔装置,使配合料横向和纵向成垄,增加配合料吸热表面积,提高火焰辐射效率。 6.除尘风机电机不满足能效要求的均更换或新增除尘设备。 (三)电气自动化技改建议 1.淘汰高耗能机电设备,空压机、风机、水泵选型符合有关节能规定。电动机、变压器等电气设备采用高能效产品。接触器、继电器、电磁阀等元器件采用低功耗产品。 2.熔窑燃烧系统采用精确控制、小炉燃料量智能化分配、助燃风与燃料量交叉限幅优化控制,实现自动比例调节。 3.退火窑控制系统应能提供准确、稳定和易于调节的退火温度曲线控制手段。在保证产品质量的前提下,采用加热量少的退火温度作业制度和节能控制措施。 4.车间照明宜采用高效LED灯,厂区可采用太阳能蓄电池路灯。 5.冷端采用优化系统,可多订单优化切割,可提高成品率从而降低单位产品综合能耗。 6.采取措施减少无功损耗,功率因数不低于0.95。宜采用高压补偿与低压补偿相结合,集中补偿与就地补偿相结合的无功补偿方式。宜采用滤波方式抑制高次谐波,谐波限制符合电力部门有关规定。 7.能源计量满足全厂和各子系统单独计量考核要求。 8.部分厂房新建改造,可新增部分屋顶光伏发电装机功率。 (四)智能化技改建议 1.设置智慧工厂网络系统及生产管理数字化系统,打通信息孤岛,提升玻璃生产数字化、智能化水平,完善设备管理系统,提高企业整体管控水平。 2.采用能效管理系统对燃料、电、水、蒸汽、压缩空气、氮氢气等能源的实时能耗数据采集、监视,通过大数据分析,找出企业管理、设备、工艺操作中的能源浪费问题;核算企业节能效果,明确企业节能方向。 3.在中央控制室设置数据及控制中心,对各子车间生产进行智能化集中监控和统一管理,在原料、水泵房、空压站、油站等分车间实行就地无人化操控。 七、未来平板玻璃企业碳减排技术展望 (一)加快研发玻璃熔窑利用氢能成套技术及装备、浮法玻璃工艺流程再造技术、玻璃熔窑窑外预热工艺及成套技术与装备、大型玻璃熔窑大功率“火-电”复合熔化技术、玻璃窑炉烟气二氧化碳捕集提纯技术、浮法玻璃低温熔化技术、再生热化学蓄热器(TCR)技术等,加大技术攻关力度,加快先进适用节能低碳技术产业化应用,进一步提升玻璃行业能源使用效率。 (二)研发玻璃生产超低排放工艺及装备,探索推动玻璃行业颗粒物、二氧化硫、氮氧化物全过程达到超低排放。-附 言 本指南参加单位及人员: 中国建筑材料联合会:陈国庆、孙星寿、曹会保、宋有崑、刘杨、张娅妮、张凯博、冯帅、周鸿锦、秦松、石红卫、罗宁、刘新琪、王勇。 中建材玻璃新材料研究总院有限公司:江龙跃、吴琼辉、李道云、张卫、陆晨、盛文彬。 秦皇岛玻璃工业研究设计院有限公司:赵恩禄、陈轶韬、周城。 中国新型建材设计研究院有限公司:程华、沈克俭。 中国建筑材料科学研究总院有限公司:何捷。 中国建筑材料工业规划研究院:郝梅平、白云峰。 中国国检测试控股集团股份有限公司:鹿晓泉、易帅。 中国信息通信研究院:胡景楠。 中化地质矿山总局化工地质调查总院:屈云燕。 北京国建联信认证中心有限公司:武庆涛、尹靖宇、张晋、杨中周、钱建荣、王瑞蕴、方群。 河北南玻玻璃有限公司:张清山、李博、贺杰峰、杨再兴、王振刚。 滕州金晶玻璃有限公司:辛明、曹国、高自强、马西传、高波。 洛玻集团洛阳龙昊玻璃有限公司:刘志刚、陆志强、胡松涛、王磊、魏星。 本指南在编写过程中得到了阎晓峰、李叶青、彭寿、刘成雄、刘起英、张冲、刘世民、隋明洁、包玮、隋同波、蔡玉良等专家及其他相关单位的指导和帮助!工业和信息化部原材料工业司等有关部门全程参与并予以指导!资料来源:http://www.cbmf.org/cbmf/yw/7193696/index.html
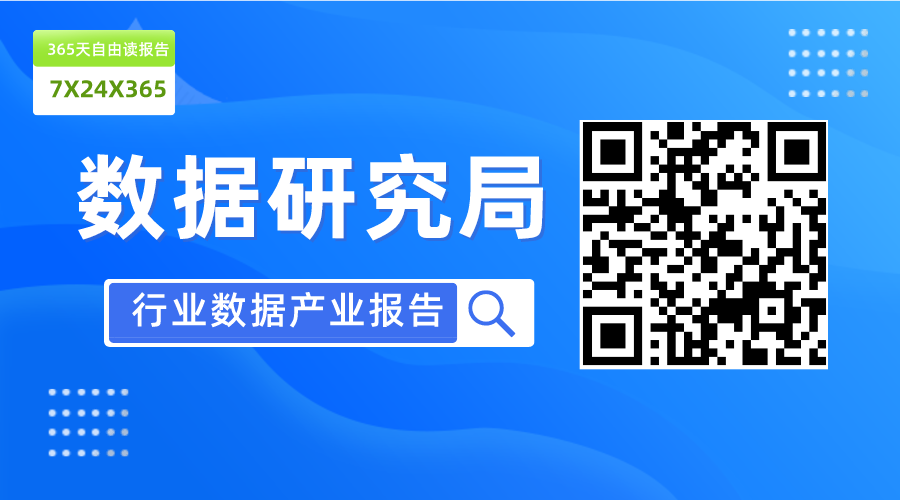
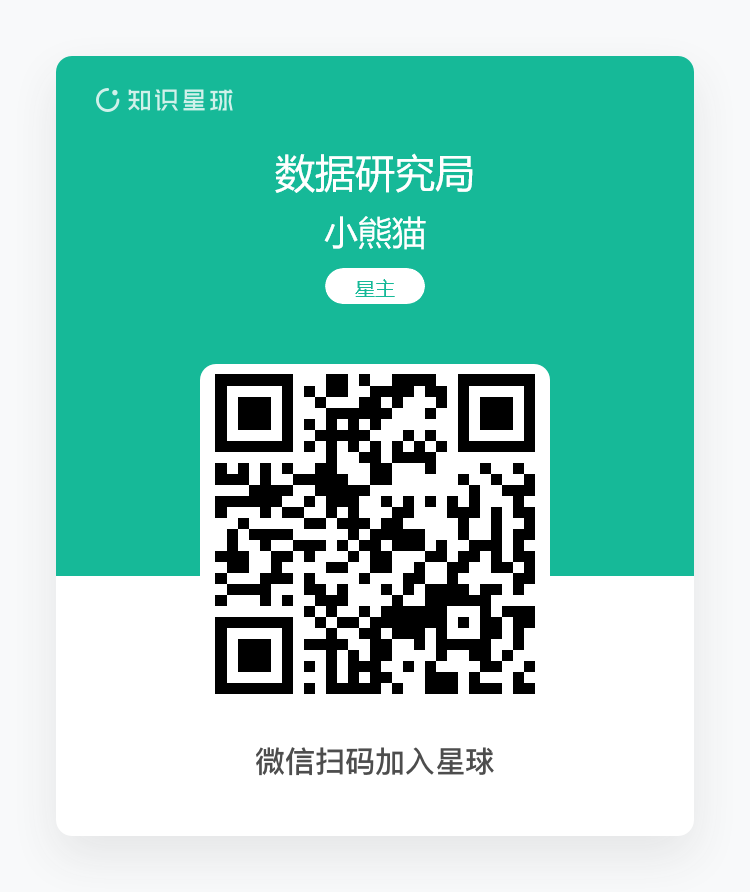